Browse Categories
Browse Archives
Powdered Metal Parts Deburring
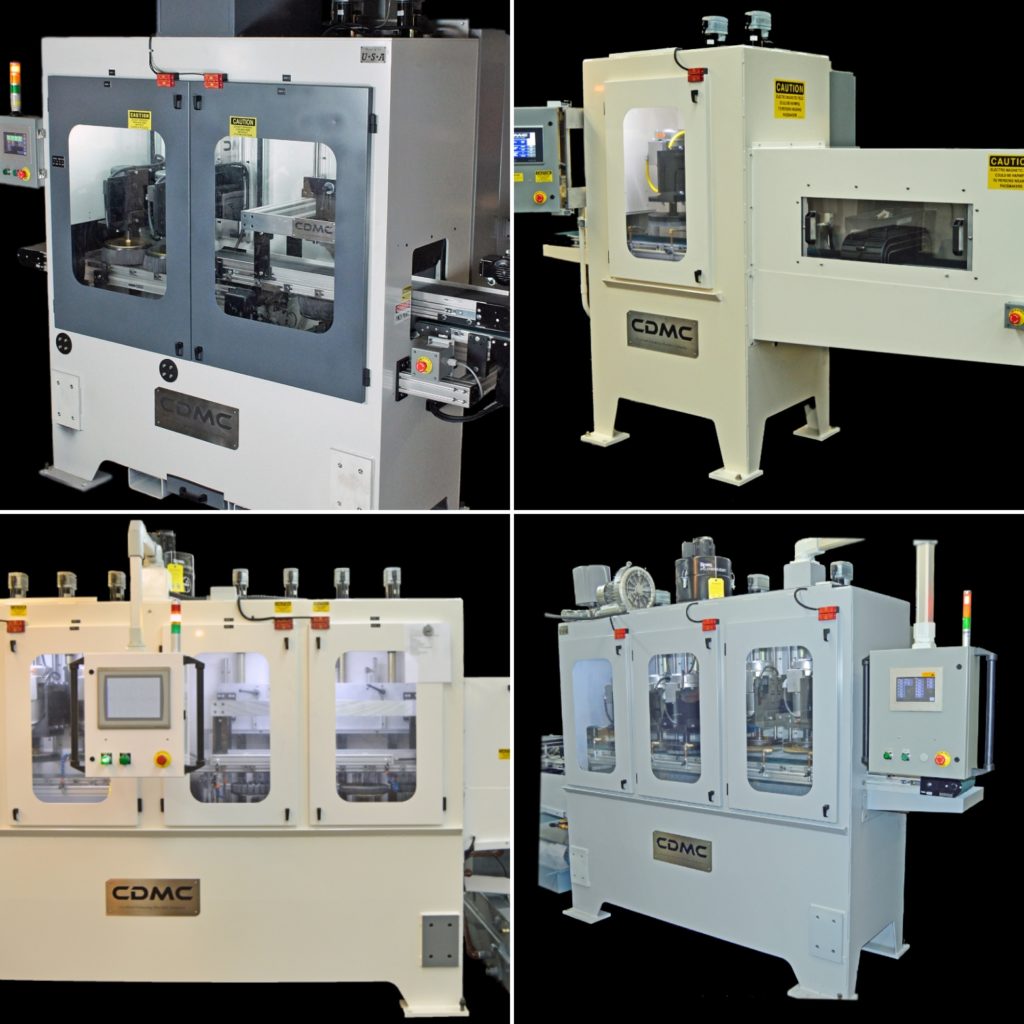
At the beginning of 2020, sustainability showed up on the trends lists of almost every major industry. But sustainability isn’t just a New Year’s buzzword. Increasingly, sustainability is becoming an achievable goal for a growing number of consumers and companies. Never one-size-fits-all, sustainability is incorporated into multiple elements, from the food we eat to the clothing we wear. Sustainability is also a continuing commitment in the manufacturing industry.
Working toward such a goal is easier when looking at the bottom line and there is a natural reason to emphasize the reduction of unnecessary waste. Therefore, manufacturers are always looking for ways to make their processes more efficient throughout the supply chain. One tried-and-true aspect of sustainability includes the use of powdered metal deburring on powdered metal parts.
Adaptable and Versatile
Powdered metal parts are an important part of the manufacturing landscape and because of varying levels of strength of greenware used, some options may be sturdier than others. When part strength is critical, consider the use of powdered metal deburring. The reliable process uses compacted metal powder that’s sourced from some of the sturdiest elemental metals. Heat at just below the point of melting joins the metal powders into a cohesion of strength. The use of powdered metal is preferred by manufacturers because it produces very little scrap metal waste. The reduction of waste supports comprehensive sustainability measures and offers versatility of design.
Although the use of powdered metals offers versatility, there are some issues in the process that CDMC set out to improve. The low profile of powdered metal parts requires deburring to remove burrs on both faces. Machines of the past employed nylon disc brushes, a method that required operators to use their hands to flip the object to its opposite side. With such a method came human error, which resulted in a loss of time and resources.
A Better Way
CDMC understood there was a safer and more efficient way to deburr these critical pieces. In response, the company created the Mag Series and the 4000 Series deburring machines to reduce downtime, boost optimization and improve consistency of operations.
Mag Series – Through-feed, in-line deburring machines are ready to tackle the high production of flat parts in need of deburring on both sides. Parts are conveyed using a series of magnetic conveyors and are available in 2-, 4- or 6-head platforms and in Mag T versions.
4000 Series Green Powder Deburring Machine – Adaptable through-feed deburring machines deburr parts on opposing sides and brushes offer simultaneous two-side deburring to accommodate almost any infeed/outfeed orientation, also available with OLS’s exclusive Auto Amp Compensation system.