Variable Cam Timing Component Deburring – Case A
Case A
JOB NO. 269
DUAL SIDE DEBURRING VIA MAGNETIC SYSTEMS
Application
A manufacturer of a variable cam timing component needed the ability to brush flat parts on both sides. This customer works in very high volumes and needed machines to satisfy thousands of parts per day. To aid with brush life and machine cleanliness, a wet process was required.
Solution
Machine Bases
- Bases are long and relatively slim to account for a large quantity of brush stations in succession. ½” steel plate is used to support robust brush heads capable of removing an aggressive burr. Wet machines must have fully welded seams to prevent coolant leakage. Sheet metal enclosures supplement machine bases at entry and exit to keep operators dry/safe. Large front doors are used to ease the burden of machine maintenance.
Processing
- Parts arrive at the incoming conveyor and are quickly engaged by rare earth magnets embedded in the conveyor’s frame. An incoming sensor reads a present part and initiates machine cycle. Numerous parts can be fed through this machine in rapid succession. If the stream of parts is continuous, the machine will cycle continuously unless a fault is detected.
- The incoming conveyor carries parts through a series of 2 (Mag 4) or 4 (Mag 8) 8”-10” nylon abrasive end brushes. A row of nozzles spray coolant onto the work/work surface to aid cutting and reduce heat. D/C brush motors are mounted to adjustable slide assemblies and carried by electronic linear actuators on a linear rail assembly. Auto Amp Comp settings are used to control depth/aggressiveness of cut.
- As parts exit the first set of brushes, they are picked up by second, inverted conveyor in order to expose their underside for brushing. The inverted conveyor is affixed to a linear rail/carriage assembly and manually height-adjusted via ball screw/crank handle, allowing a wide range of part thicknesses to be accepted.
- Once exited from all brushes, parts are transferred onto a cleated conveyor and taken through a demagnetizer. Depending on the application, a pneumatic blow-off or coolant wash down will be present just before exiting the machine.
Safety/On Site Requirements
- A variety of media can be used/staggered from station to station. Customers are able to alternate more/less aggressive cutting options or use both in the same application.
- A variety of HMI options are available upon request. HMI pendants can be solid wall mounted, swinging wall mounted or rail mounted for max mobility.
- Large machine casters are available upon request. These can be used to more easily transport a Mag machine but operating on casters is not advised.
- If coolant is to be used, CDMC offers cleaning systems such as bag filtration, oil skimmers, mist collectors and magnetic particle separation.
- If the application is dry, CDMC offers a wide range of dust collection systems.
- All manual doors are electronically interlocked. Breaking an interlock will stop machine cycle and cause a fault state.

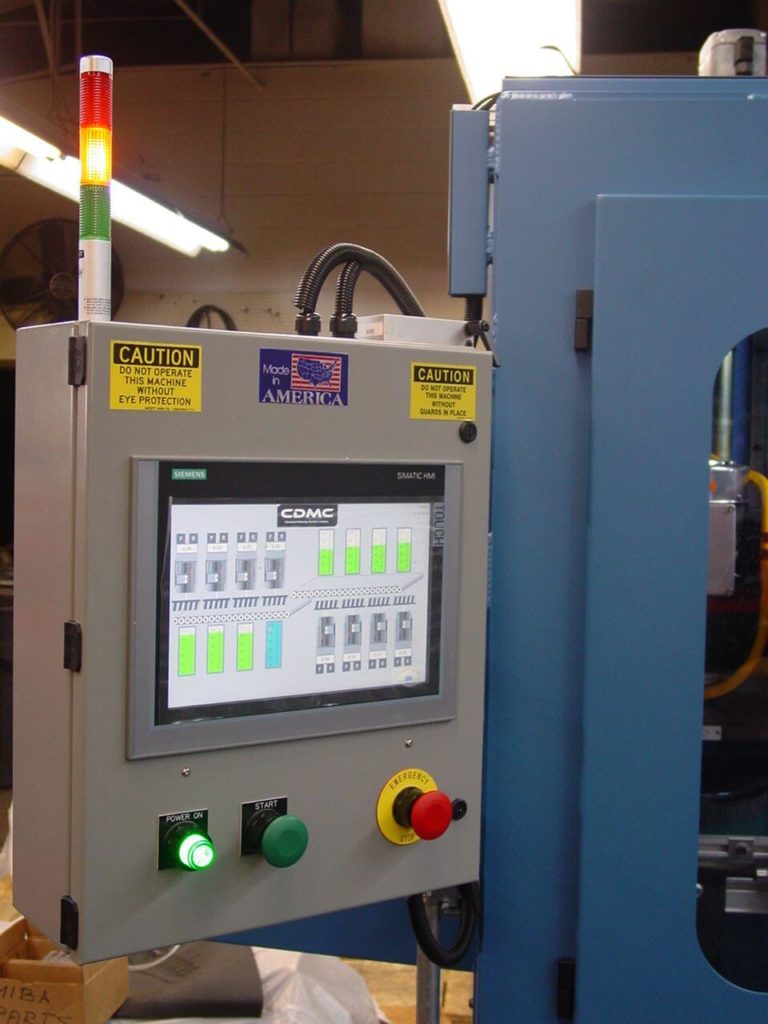
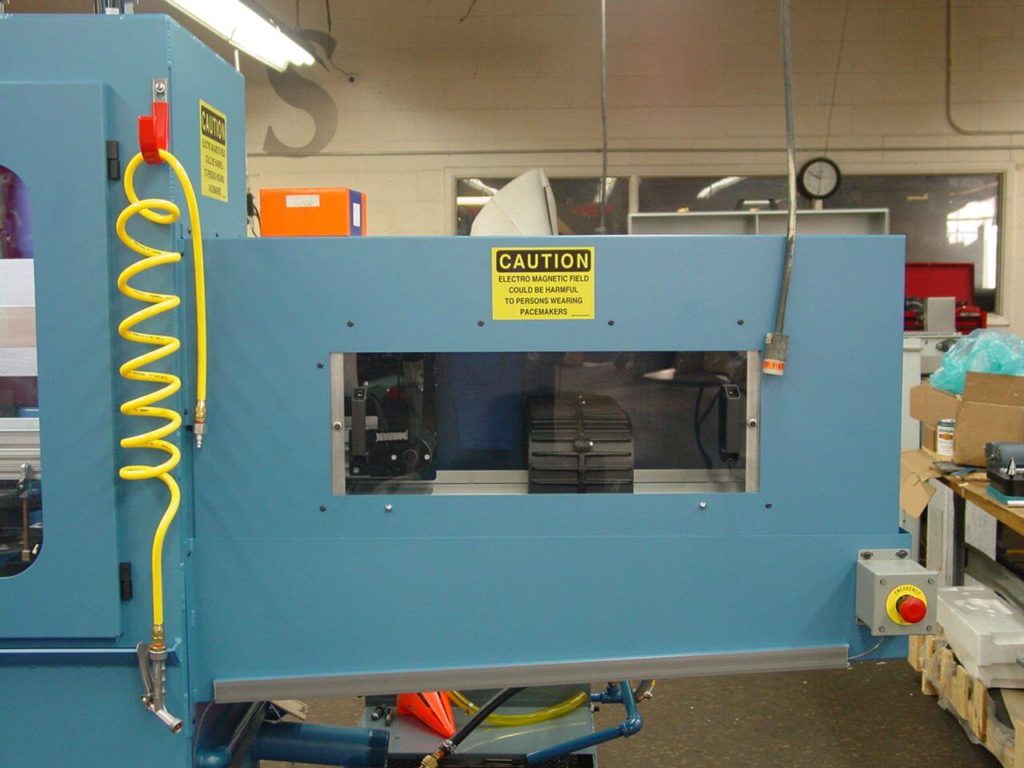