Transmission Component Descaling and Deburring
Application
A manufacturer of automotive drive train components needed a descaling and deburring autonomous solution to descale/polish shaft sections and deburr the “crown” section of an input shaft. The work cell had to be capable of taking the work piece from an incoming conveyor, through a work cycle and to an outgoing conveyor without human interaction. The customer agreed to handle the necessary safety fencing around the cell while CDMC was responsible for a sheet metal enclosure to aid with dust collection. A pedestal-mounted dust collection unit was also required.
This customer had a custom paint specification as well.
Solution
Machine Base
- A custom pedestal and work-station riser are fabricated from 1” steel plate and steel tubing. It is imperative that clearance holes are manufactured into this pedestal so that it can be tied down on site.
- A four-sided sheet metal enclosure is placed behind the work area. Sparks and debris are collected through a spark-arrested cutout in the backside of this enclosure.
Processing
- In order to work autonomously, part transfer and treatment are be handled by the robot. Once a shaft has arrived at the incoming conveyor nest, the robot positions its End of Arm Tooling (EOAT) so that custom grippers can lift the work piece and begin transfer to the work station.
- The work piece is placed onto the rotating part drive spindle. A spring-loaded pin finds a corresponding opening in the hub face and locks the work piece into place. A pneumatically actuated tail stock lowers to pin the shaft center in place and prepare it to be treated.
- The “crown” of the hub is deburred by a 6” twisted steel wire cup brush utilizing Auto Amp Compensation to determine the cutting force to be applied. The cup brush is directly driven by a large frame D.C. motor mounted to a pivot assembly. A linear NB rail package and electronic linear actuator are used to transport this brush to/from the feed/retract positions. Feeds and speeds of this assembly are adjustable on the HMI screens.
- Shaft descaling is performed by a 15” half-twist steel wire knot radial brush at the robot’s EOAT. The robot follows a program of positions taught by one of CDMC’s FANUC robot programmers. Auto Amp Compensation is utilized here through offsets programmed into the robot controller.
Customization/On Site Requirements
- Debris is carried to the DONALDSON dust collection unit via flexible hose. A separate pedestal keeps the dust collection unit off the ground and at a more serviceable height.
- The base has been sent out to one of our painting contractors per the customer’s paint spec. CDMC is willing to comply with most specs for a cost.
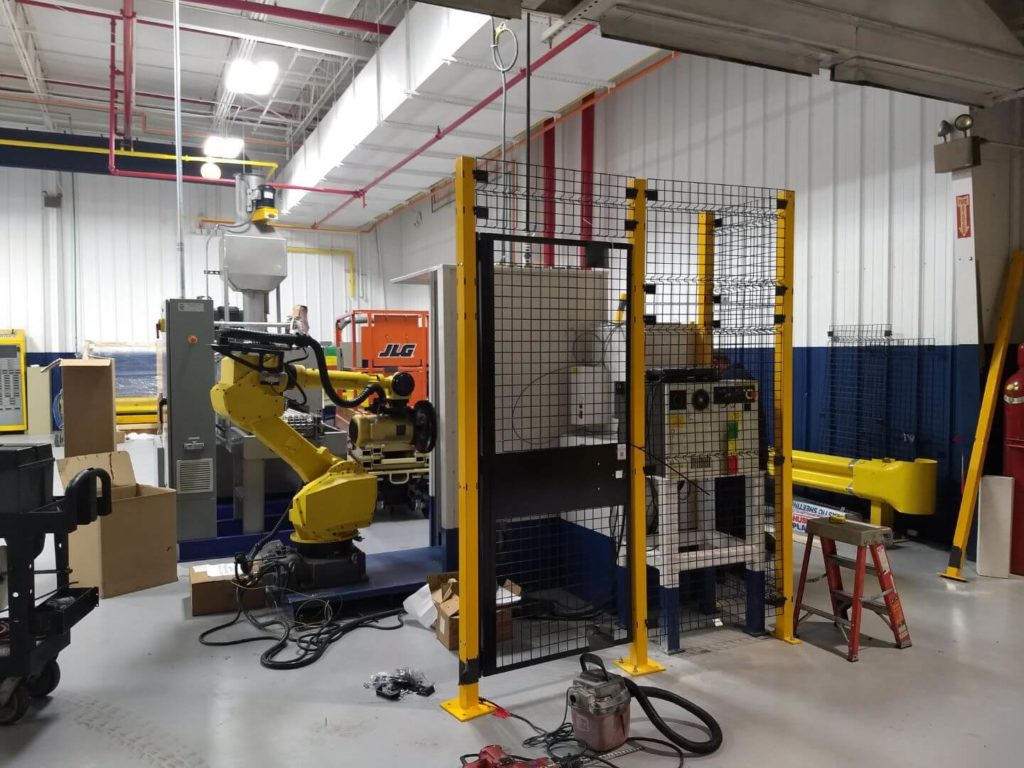
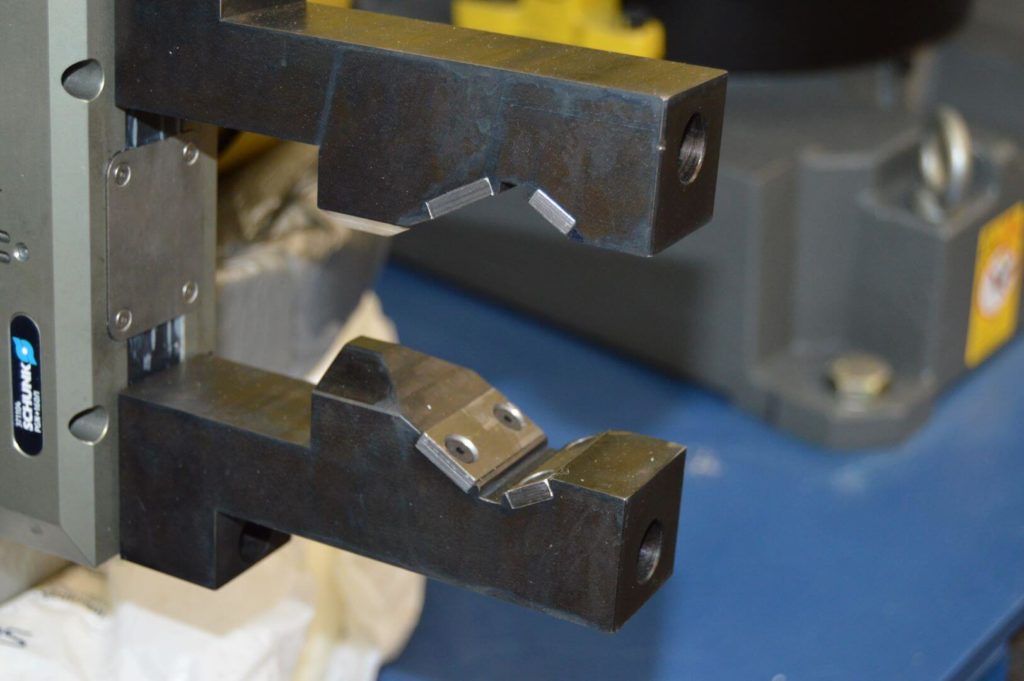
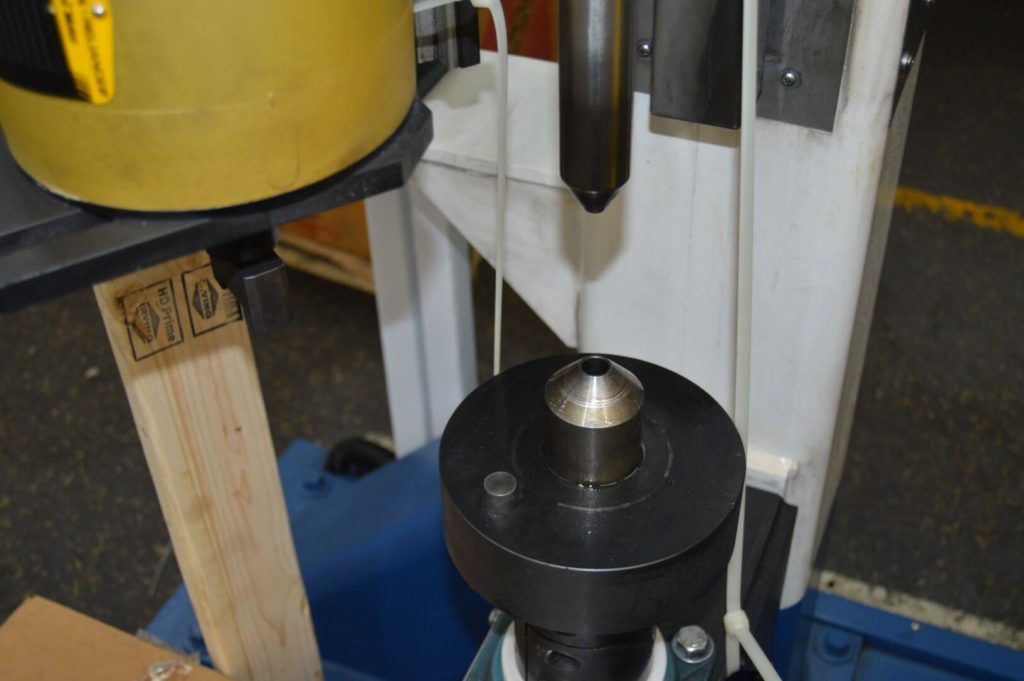
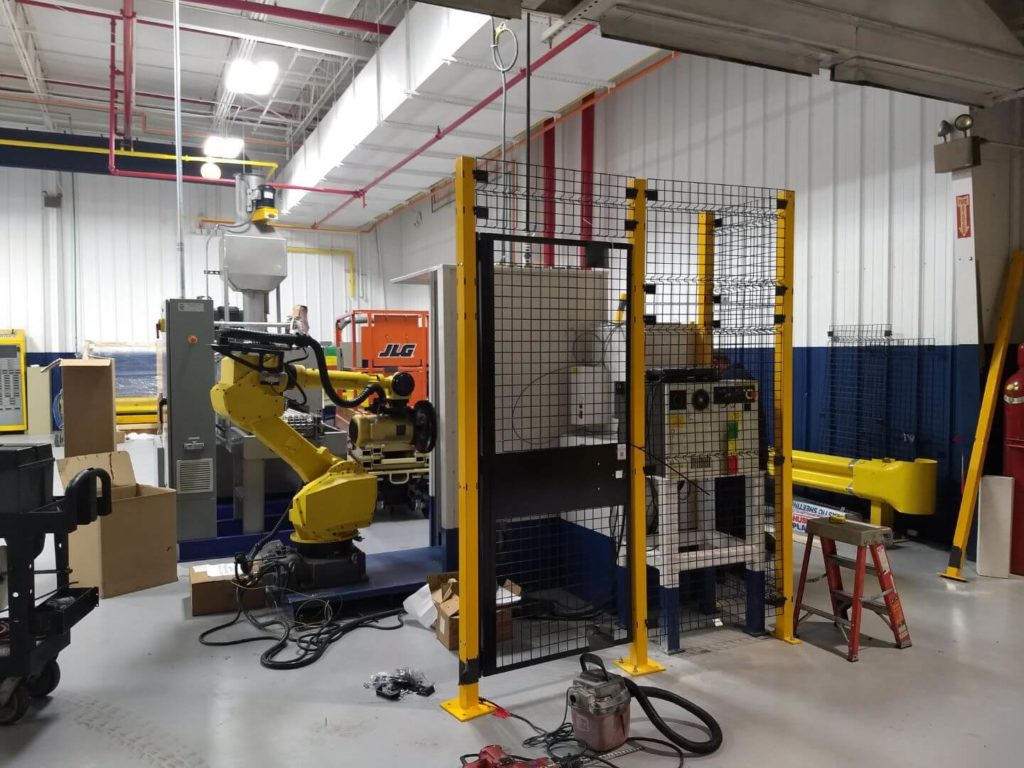
Results
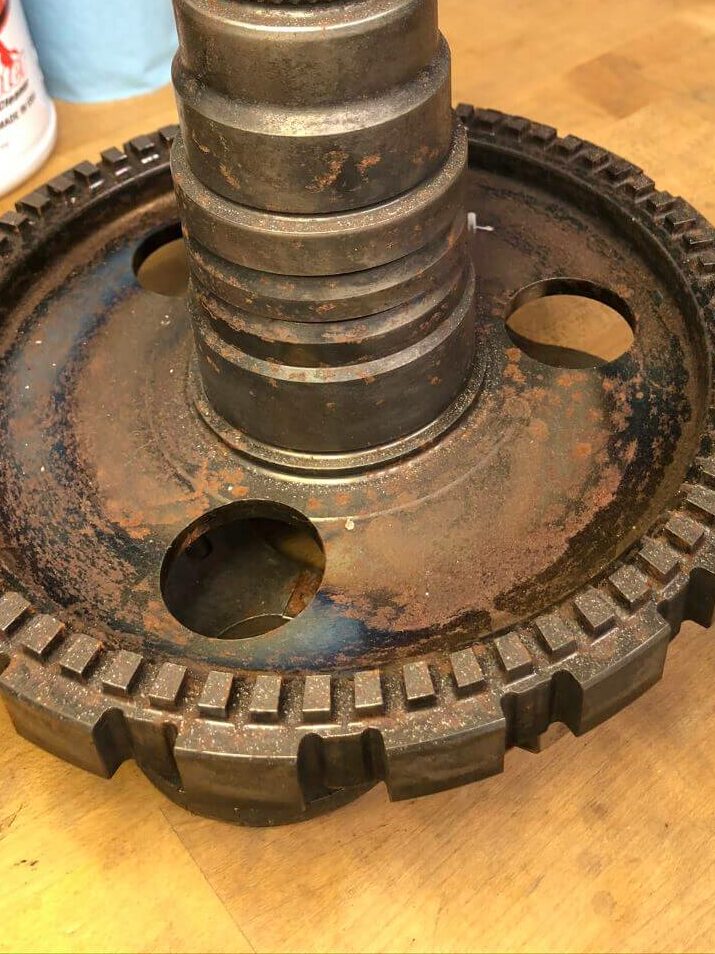
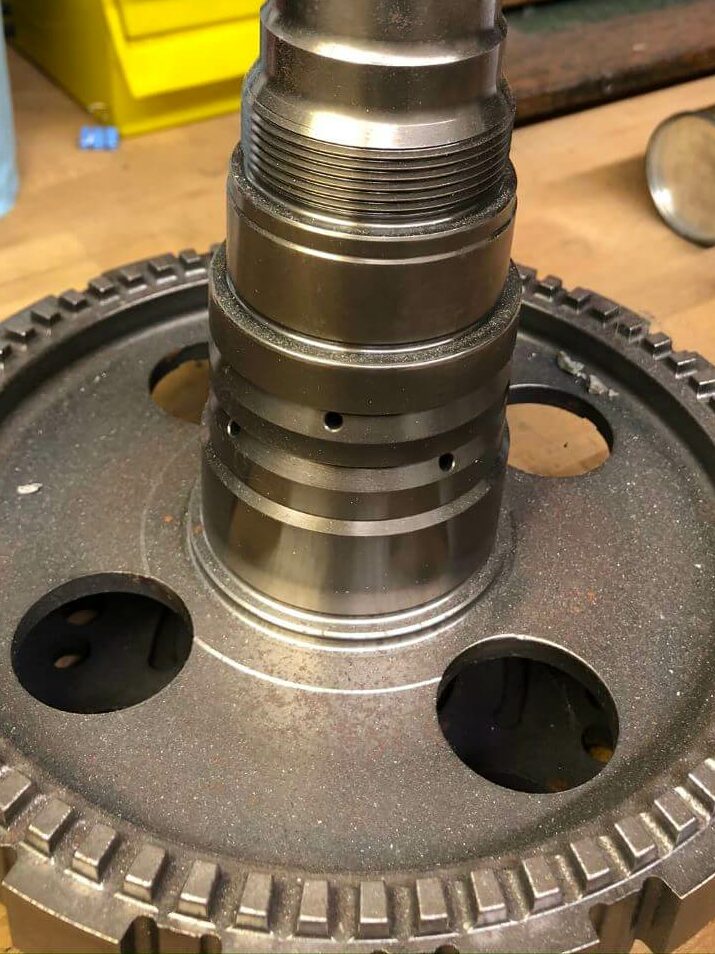