Planetary Gear Deburring
Case B
Application
A manufacturer of variable cam timing components needed large scale deburring solutions for two separate parts. These machines had to be robust and capable of processing hundreds of thousands of pieces within a short cycle time per piece. Wet and dry applications were both required along with any plumbing/dust collection, respectively. Any exterior part transfer must be safety guarded.
Solution
Machine Bases
- In order to process high quantities with multiple ops in a small footprint, medium sized rectangular bases are used. A clearance at the machines’ roofs allows for a 2” index shaft to move work spindles from op to op.
- 3/8”-1/2” steel plate walls must be used to support any heavier assemblies that will be under pressure/performing deburring ops.
- The wet application’s base must be welded water-tight while the dry application’s base does not have to be completely sealed.
Processing (Machine B)
- Work pieces arrive via customer conveyor system and are transferred onto the machine conveyor. After passing through a series of pneumatic feed escapements, the work arrives at a stationary resin load nest. A pneumatic 2-axis SMC linear slide assembly uses custom tooling to pick up the incoming work and transfer it to a collet/base assembly.
- Four spindle assemblies are installed into a 1” aluminum dial plate. A CAMCO four-station indexer unit located on the machine’s roof brings each spindle to one of two work stations and load/unload stations with excellent repeatability.
- Spindles are independently driven at each cut station by a pivoting drive gear assembly. This gear is directly driven by a high torque A/C motor and is always engaged, meeting the corresponding gear on each spindle as it is indexed in place.
- Once loaded, the work is indexed to two 15” diameter long trim crimped steel wire radial brushes. Brushes are directly driven by large frame D/C motors on tool adjustable pivot assemblies. Brush work and home positions are controlled by a 2”-3” pneumatic cylinder and linear rail system, while fine adjustments to cut feed/retract are controlled by an intelligent linear actuator utilizing Auto Amp Compensation.
- After station 3 brushing is complete, the work is indexed to station 4 for unload where it is brought from part drive spindle to conveyor by another 2-axis slide assembly.
On Site Requirements
- A custom hinge and lock design is used to allow the machine’s electrical cabinet to be pivoted away, allowing maintenance access.
- Coolant piping and nozzles routed to the work area can be used to aid in cutting, for wash-down of critical components or both. In most wet applications, a sprayer system is also used at the machine floor to wash debris toward the filtration system along with a manual wash down for PM. Cleanliness implementations such as magnetic separation, oil skimming and bag filtration are available upon request.
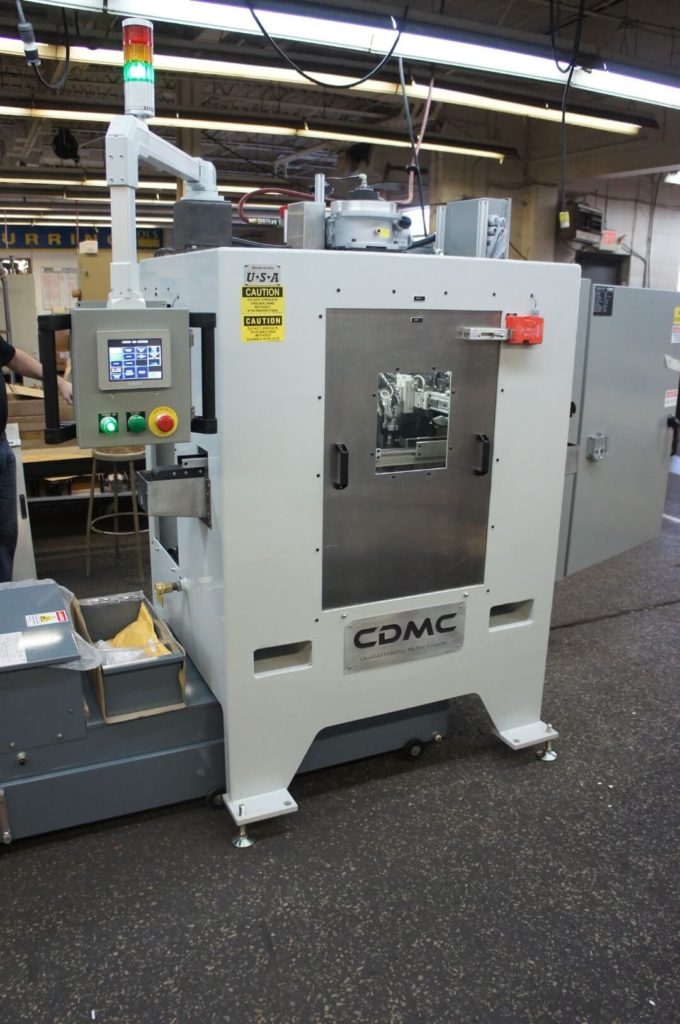
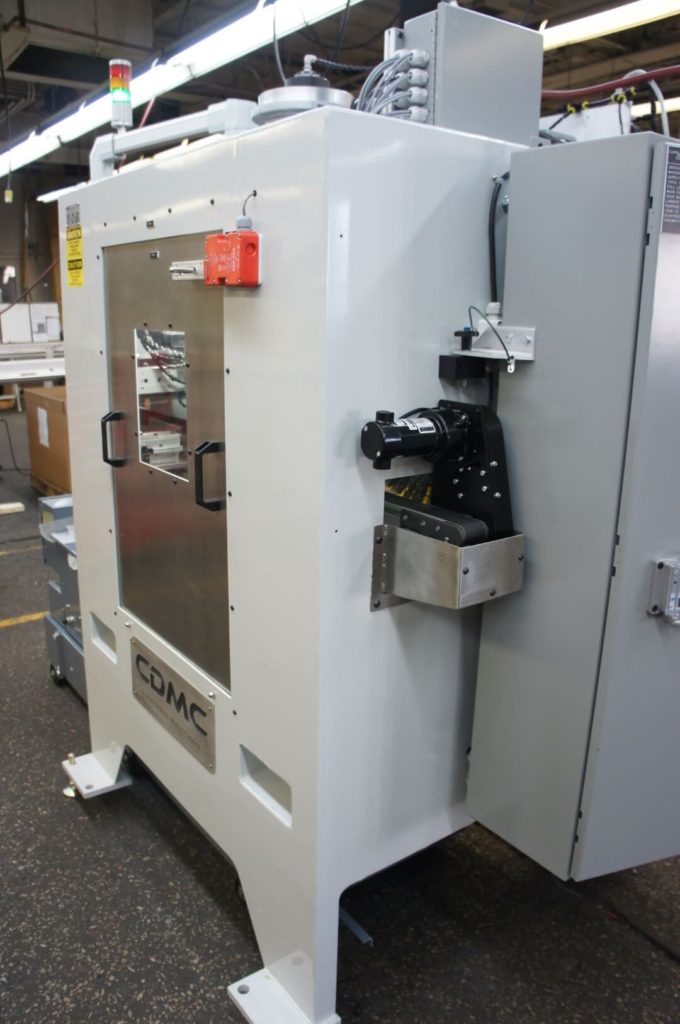
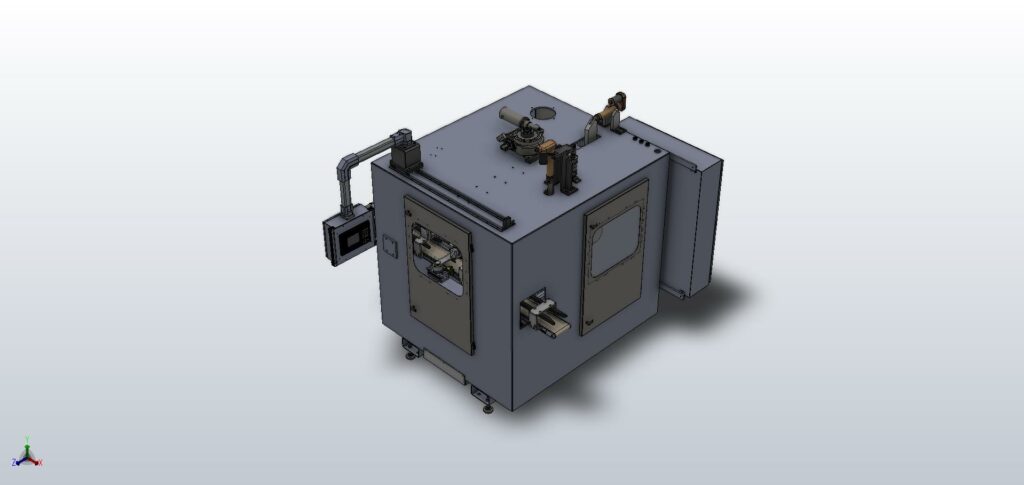
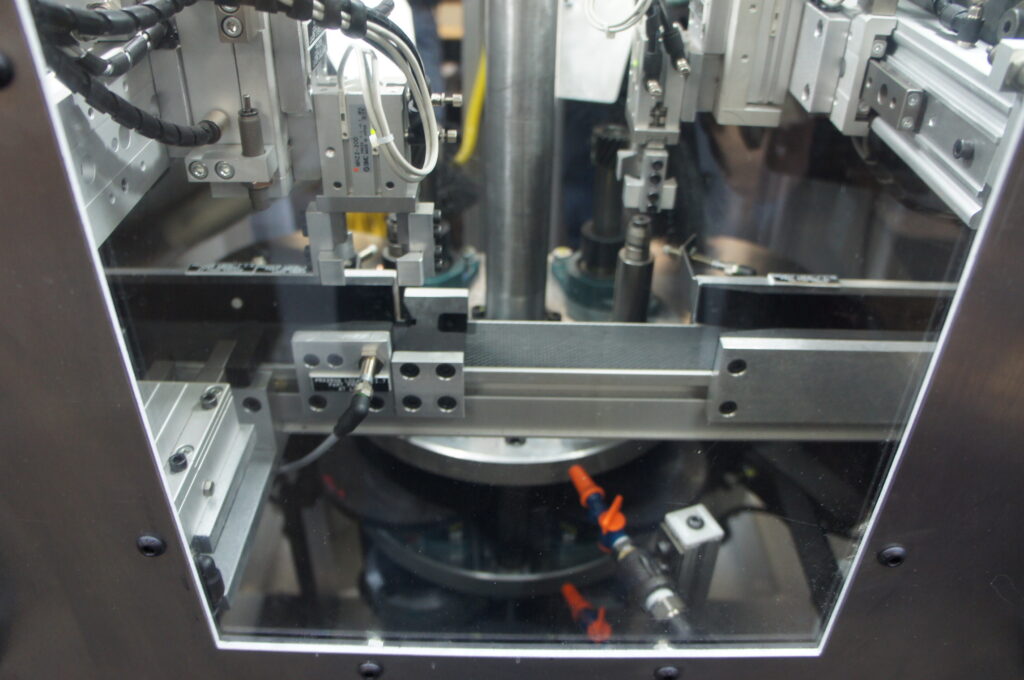
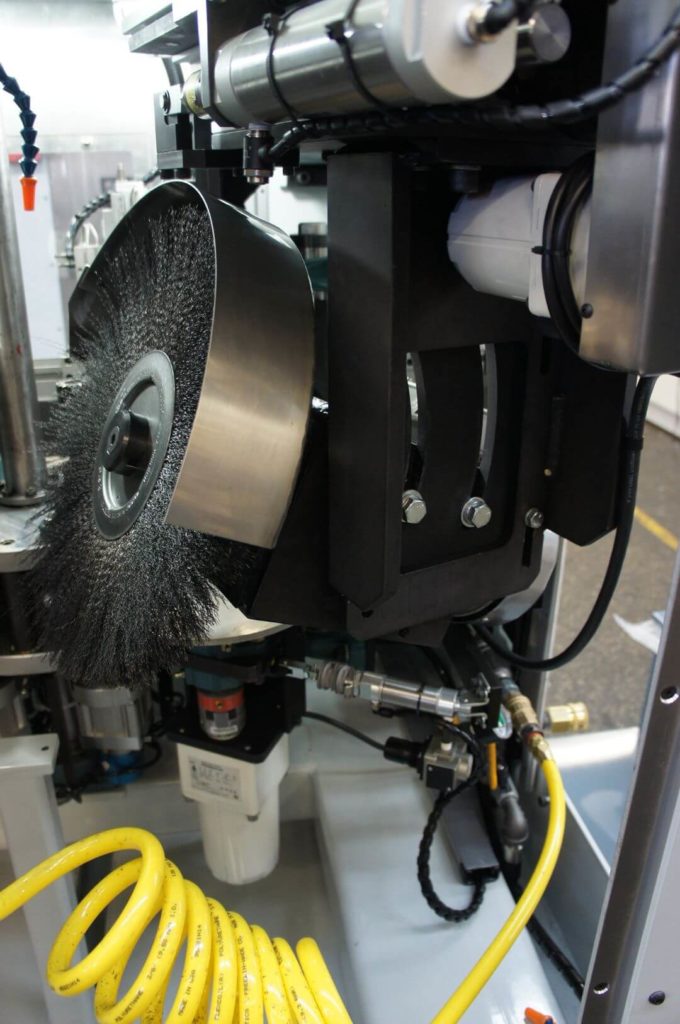
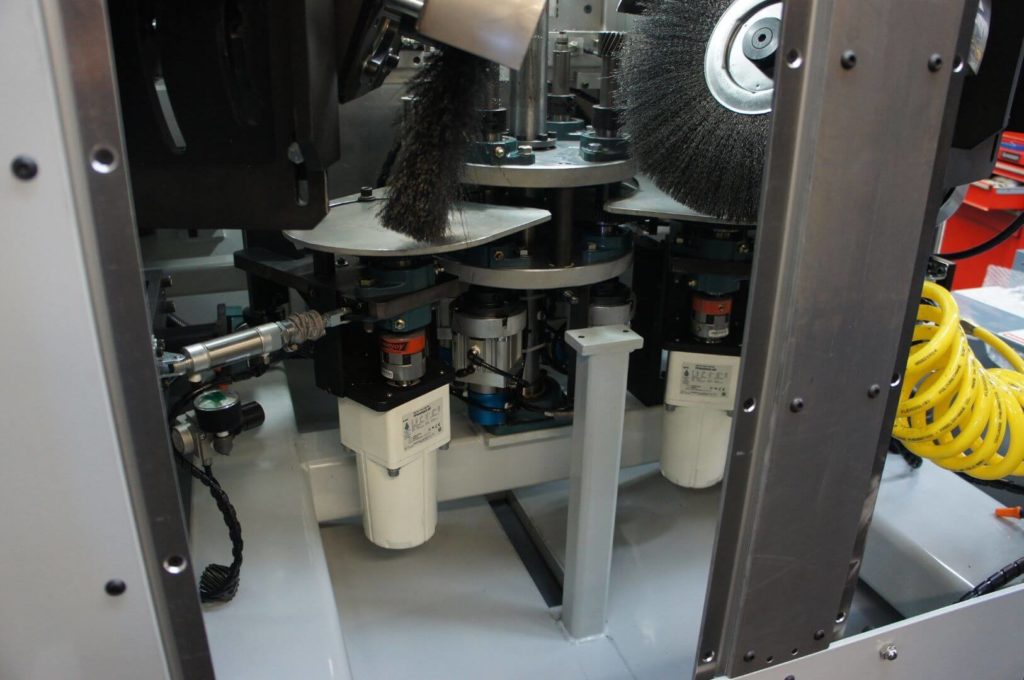