John Deere
JOBS NO. 186/195
NON-MAGNETIC THROUGH FEED GEAR DEBURRING
APPLICATION
A manufacturer of small & heavy agricultural equipment required a light edge break to multiple sharp corners of gear ID and OD. The customer’s cycle time requirement dictated that inside and outside diameters must be processed in tandem, preventing the ability to hold/drive the work piece in a traditional fashion. The customer also required more advanced safety implementations.
SOLUTION
Work Holding
- In order to process ID and OD, we implemented a roller/ball bearing system to carry the part through the machine.
- Upon arrival at the “work” position, parts are engaged by 2 directly driven roller wheels, each on an independent pivot assembly. The pivot rollers push the part into 2 stationary rollers. When encapsulated, work pieces are driven the desired direction by all 4 roller wheels.
Processing
- A cut-out in the center of the work area allows for an air motor-driven wire cup brush and a 14” D.C. direct driven wire knot wheel to access the desired work area from underneath the roller system.
- Once fully deburred, parts will exit the machine onto a more traditional roller conveyor.
Safety
- The operator side of the machine is equipped with a two-hand start system, meaning that both must be activated by touch for the machine cycle to start.
- The opposing end of the machine is monitored by an active light curtain system. If the space between curtain uprights is broken, the machine will stop immediately and enter a fault state.
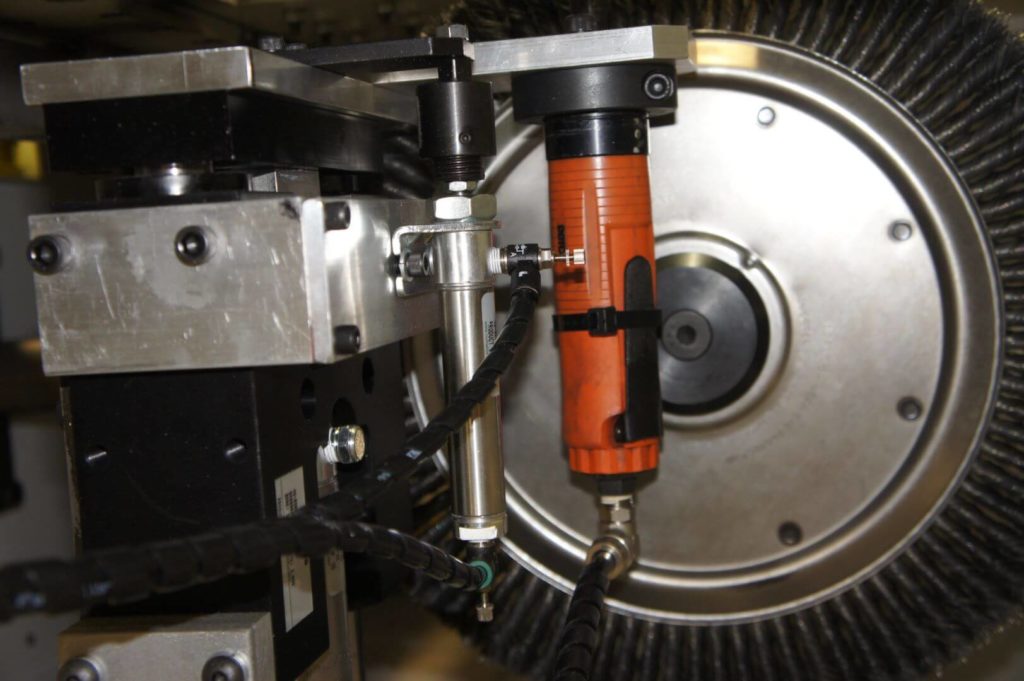
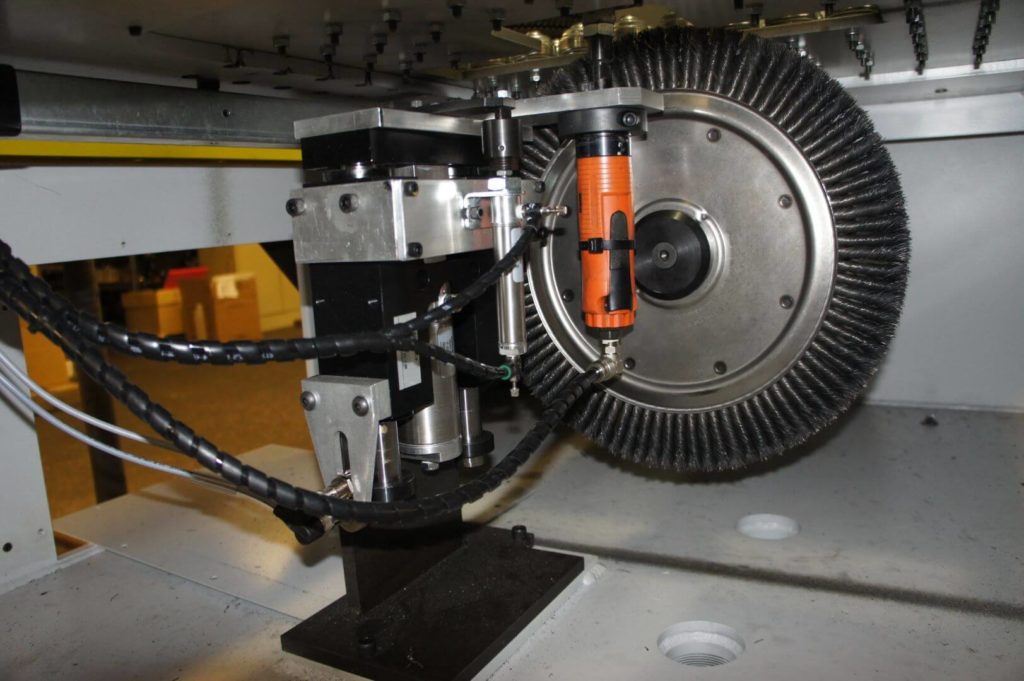
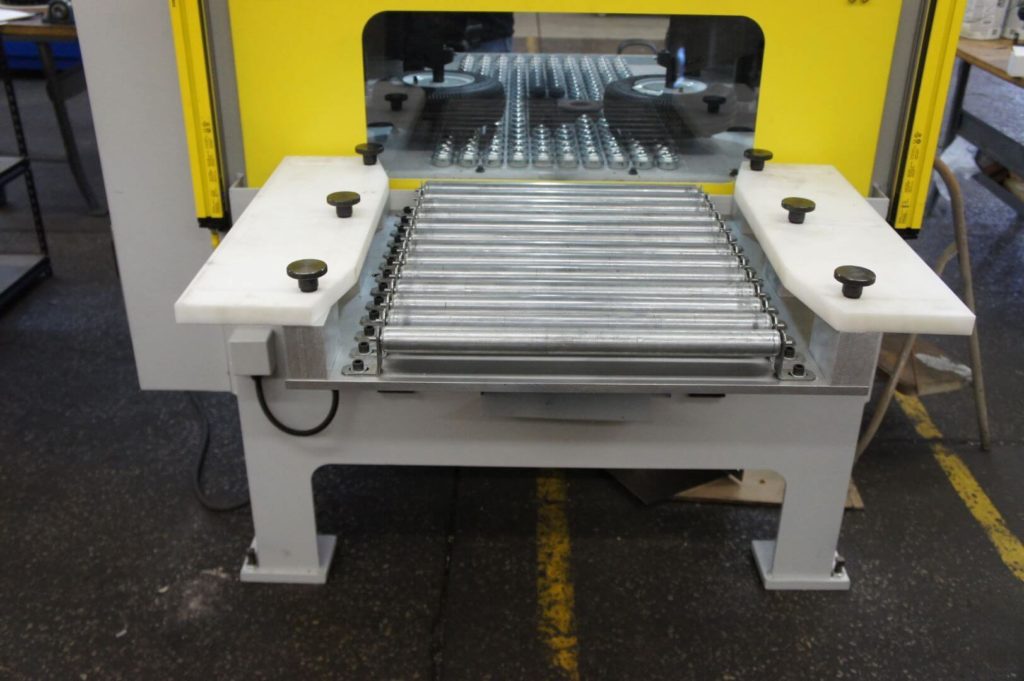
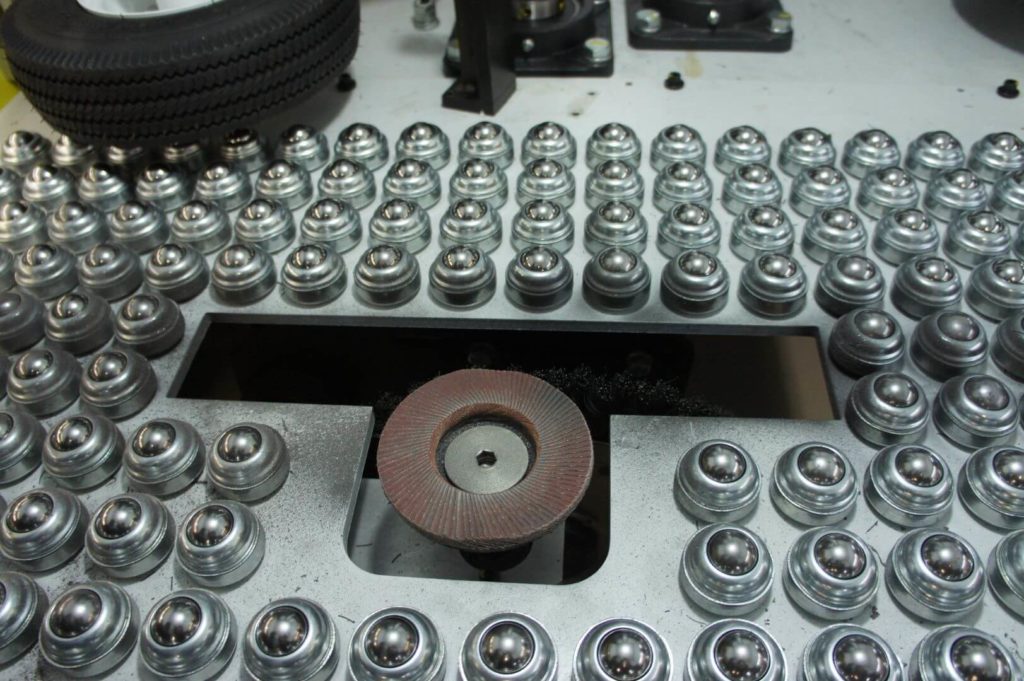
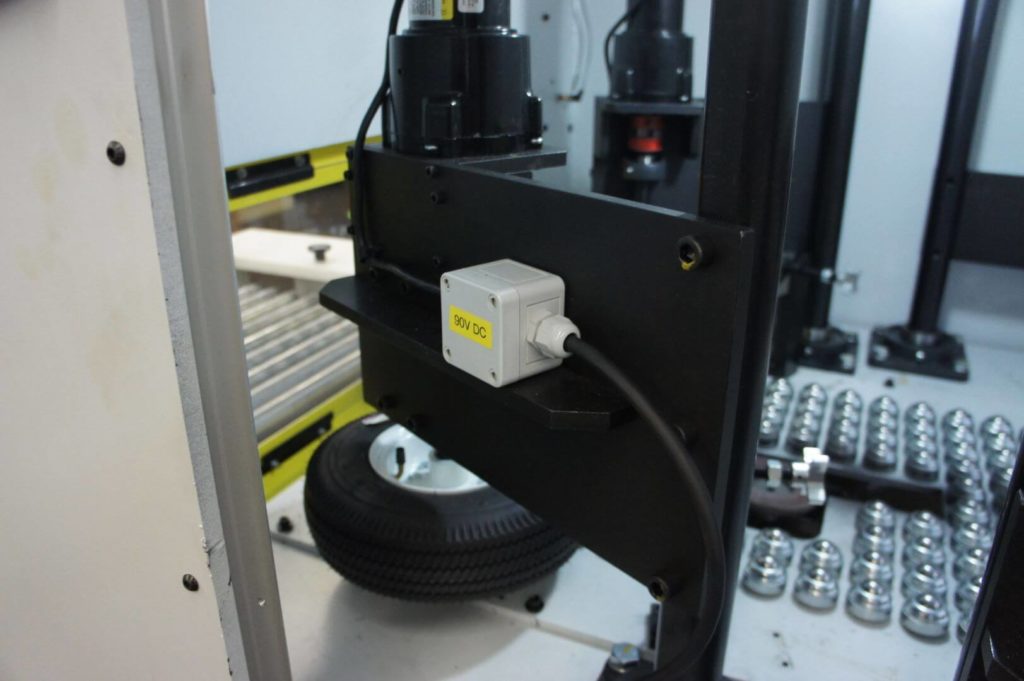
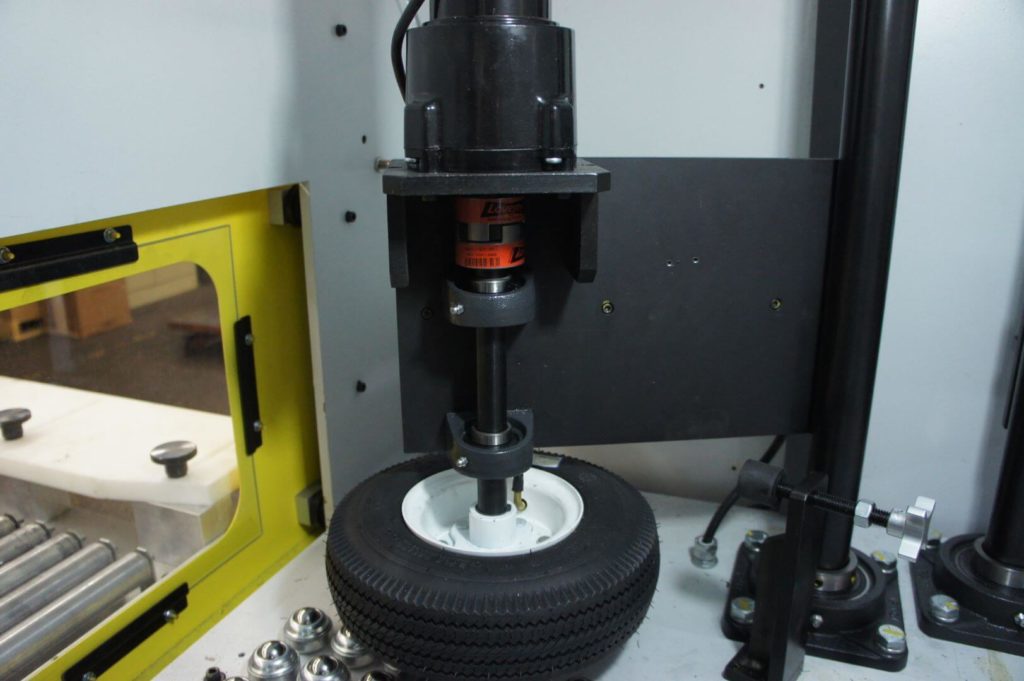
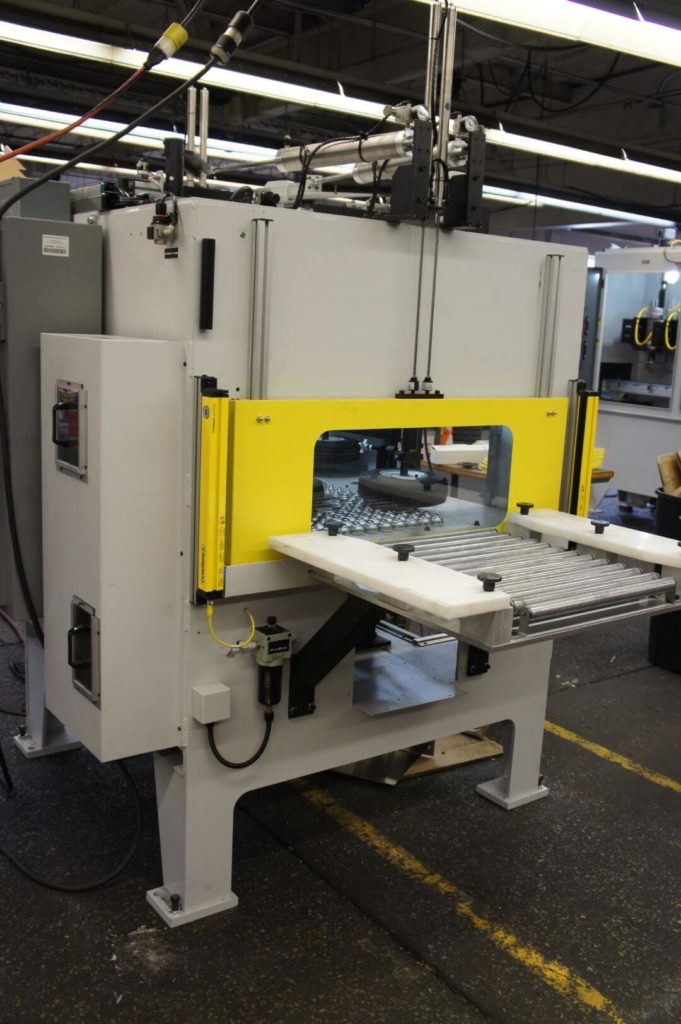
Results
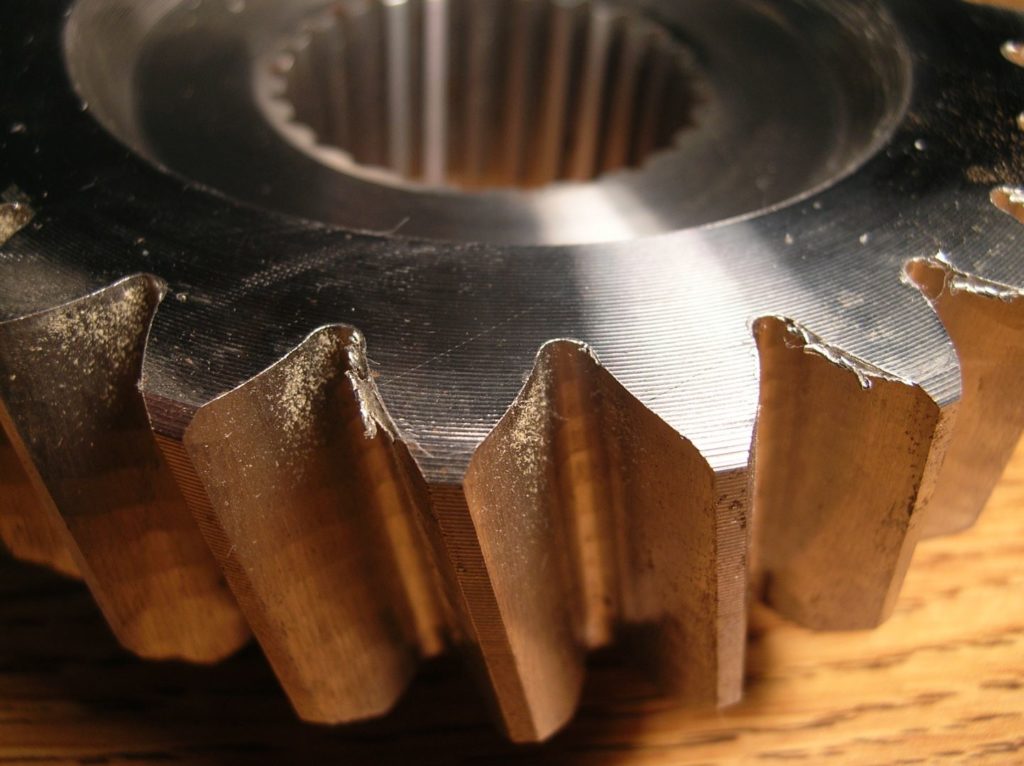
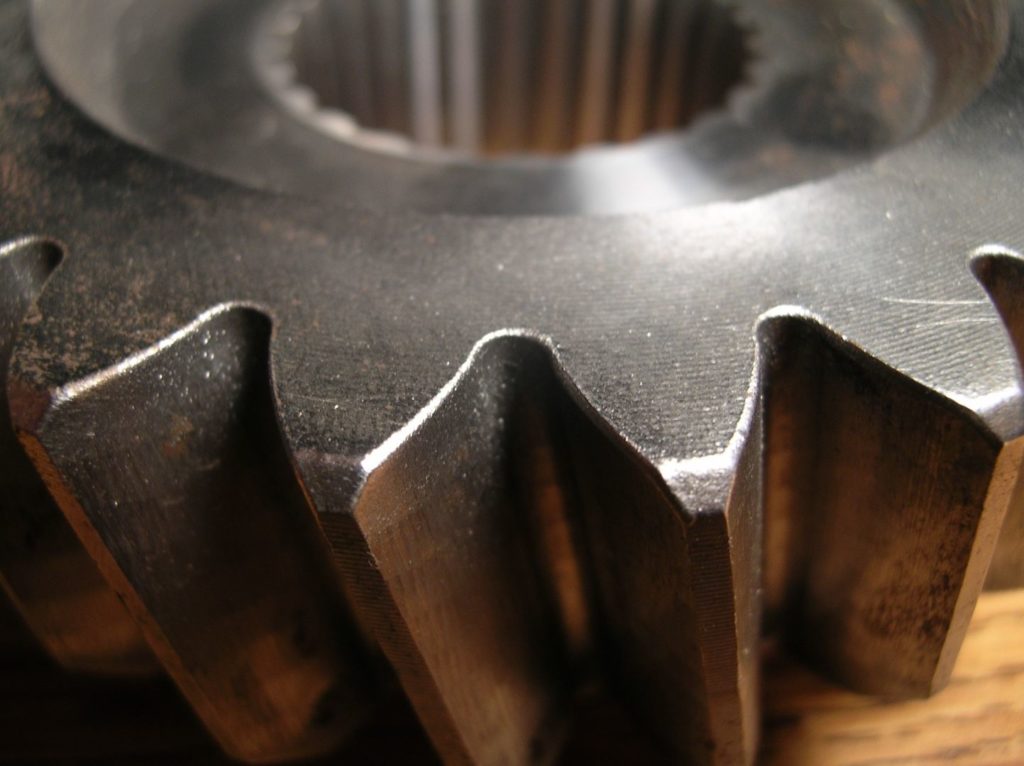