Carbide Saw Side-Grinding
Case Study B
JOB NO. 322
CARBIDE TOOTH GRINDING
Application
A top manufacturer of cutting tools required carbide reinforced blade teeth to be ground within a tight tolerance. This machine would have to be rigid enough to support large grinding heads and the operation they’d perform. The grinding operation required a large mist collection unit, a high-flow system to distribute cutting oil to each work surface and a wash-down system that would span the entire base floor. This machine was to be robot loaded.
The customer required a custom, free-standing electrical cabinet, an HMI pendant that would travel the length of the machine and a custom paint job. An internal fire prevention system was also needed.
Mist collector and fire prevention systems were purchased by the customer from outside sources. CDMC was responsible for getting them integrated into the main assembly.
Solution
Machine Base
- The main assembly is an open design, allowing for the top “shell” to be removed if necessary. The lower base is made from ¾” steel plate reinforced with ¾” structural angle iron. The lower base is designed to resist flexing under the weight of the 2 ton grinding stations.
- Lower base is water-tight to prevent oil leakage, with drain channels and a gutter system built in.
- Lower base is on heavy-duty adjustable wedge pads. The pads are tool-adjustable and allow the machine to be leveled.
- A skeleton made of steel tubing rests above each grinding station and supports the machine’s outer housing.
- Wall panels are ¼” steel and attach to the ¼” steel housing. Wall panels have provisions for access doors and a gutter system built in.
- Cutting heads are supported by 1” steel welded riser assemblies weighing upwards of 2,500lbs each.
Processing
- Work pieces are robot loaded to/ unloaded from a large dial plate clamp fixture via load station located in the front machine panel. A blow-off system rests above and below load location to remove as much cutting oil as possible prior to unloading the work piece.
- The 1” ground aluminum dial plate is mounted to a large CAMCO indexer. The CAMCO indexes the blade to a “set” station to be pushed into place as it is briefly released by the clamp fixture.
- A total of 8 diamond cup grinding wheels gradually cut the required material away via horizontal passes as the work piece is indexed from station to station. Cup wheels are powered by SETCO spindle slide assemblies. All feeds, speeds and depths of cut are adjustable via the HMI.
- Each grinding head riser is mounted directly onto a surface ground into the lower machine base. Adjustments to cutting location can be made via 1” jack screws at the bottom of this assembly.
Lubrication System
- A large reservoir tank coupled with a high capacity pump circulates cutting oil throughout the machine. Adjustable precision spray nozzles are located near each cut point. Large aluminum extrusion manifolds containing spray heads are built into the lower assembly to wash debris from the floor into the gutter/filtration system. This system requires significant pressure to be effective.
- Each spindle slide is continually greased by a LINCOLN pump assembly. These assemblies are located on the base exterior and feed grease to adjustable manifolds before the allotted amount of grease is sent to the slide units.
Safety/Customization
- This machine is equipped with a fire prevention system purchased from an outside source by the customer. CDMC is willing to work with contractors at our customers’ requests.
- The main electrical enclosure is customized with windows that allow electrical systems to be monitored safely by machine operators and management.
- The base has been sent out to one of our painting contractors per the customer’s paint spec. CDMC is willing to comply with most specs for a cost.
- This machine is equipped with an HMI on a swinging pendant/linear rail system. This allows operator access to the interface from a wide area.
- A customer-owned mist collection unit was shipped to/integrated by CDMC.
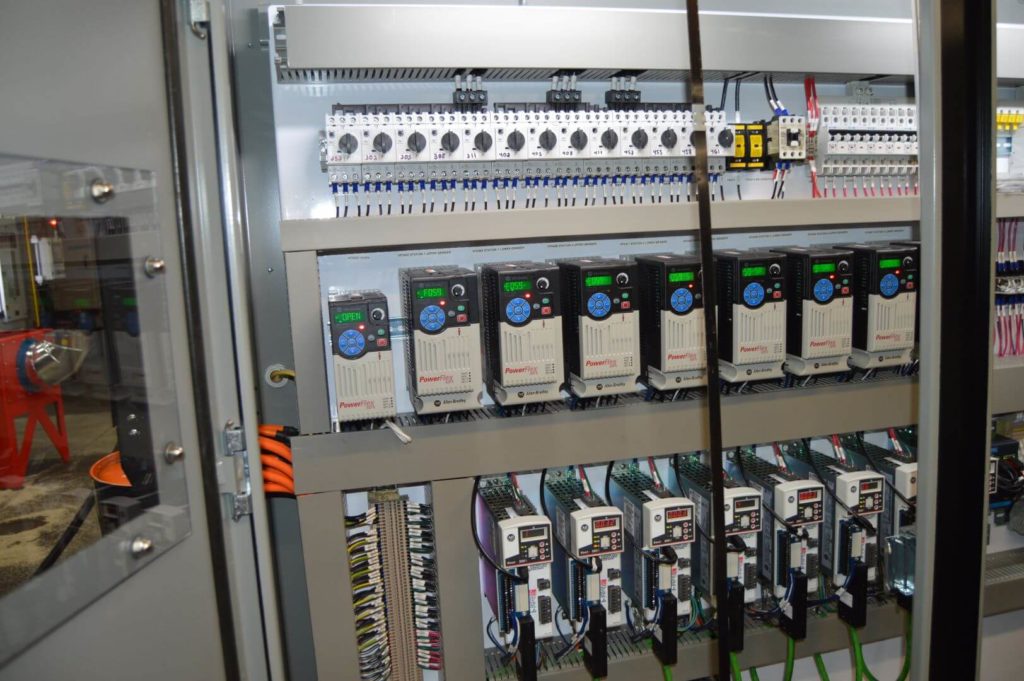
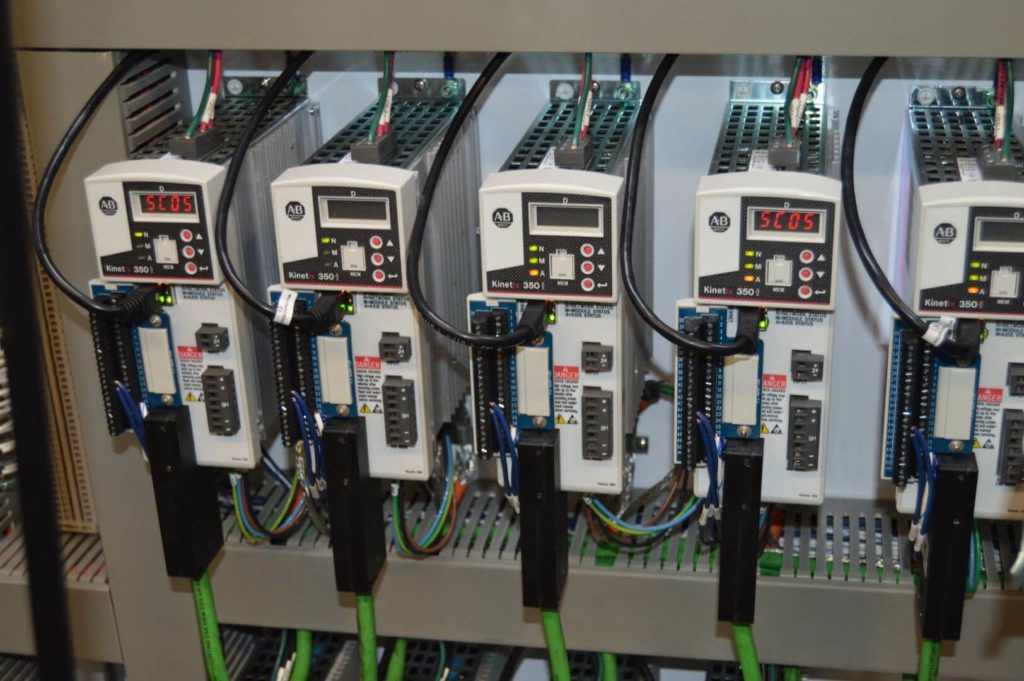
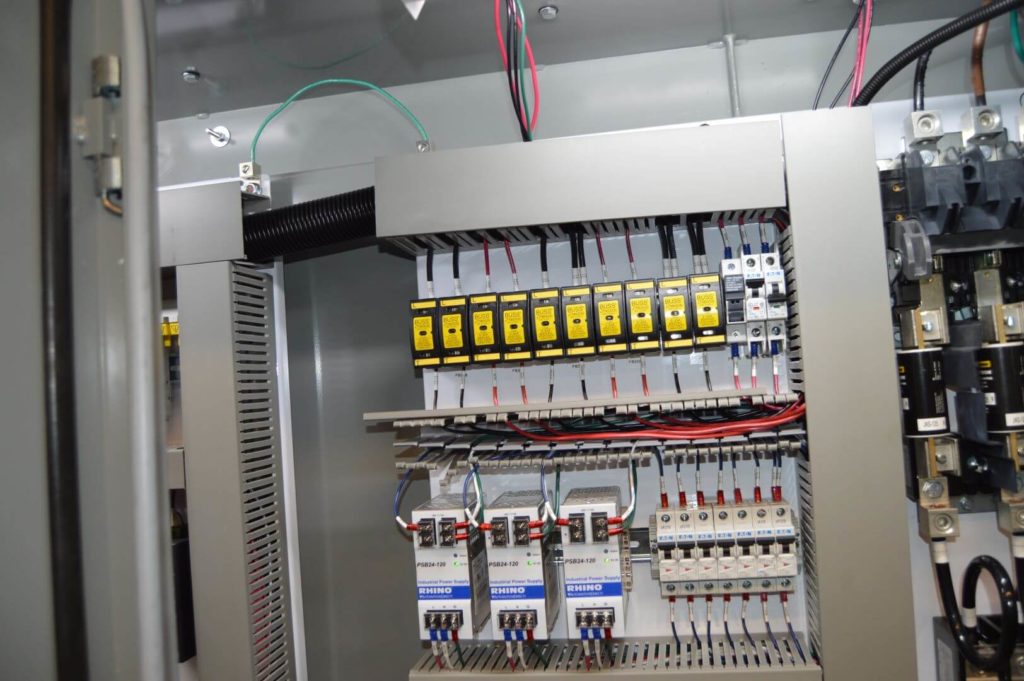
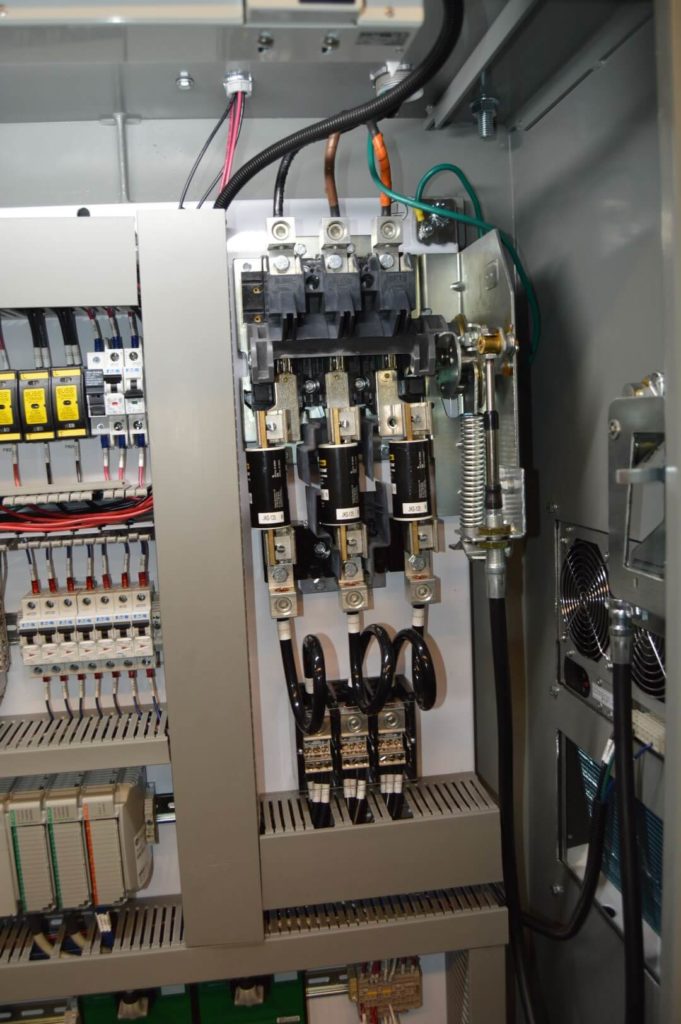
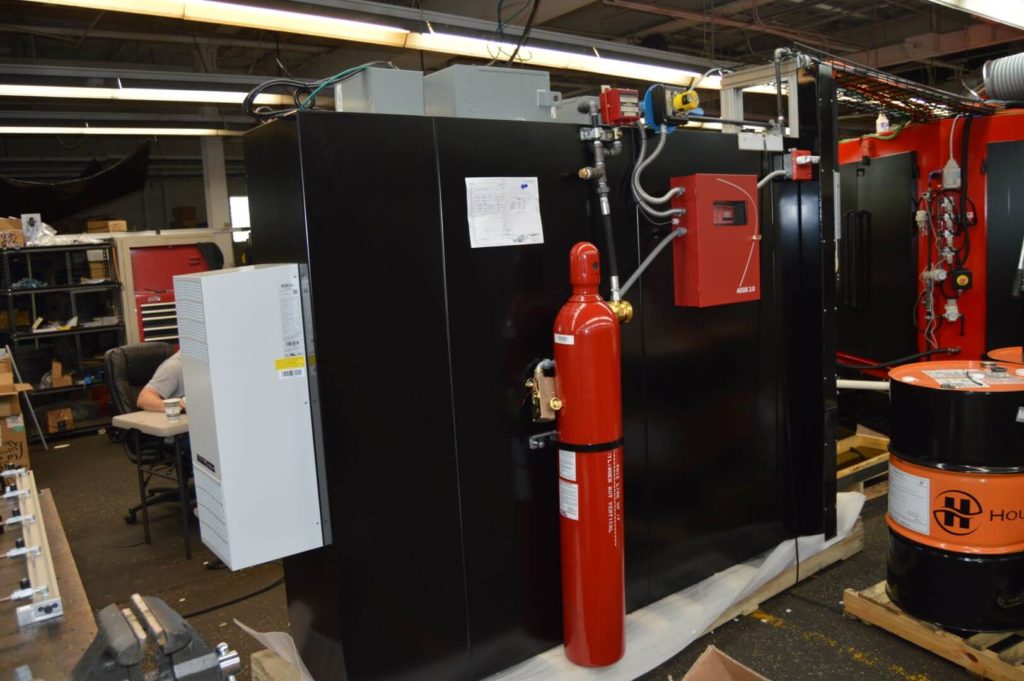
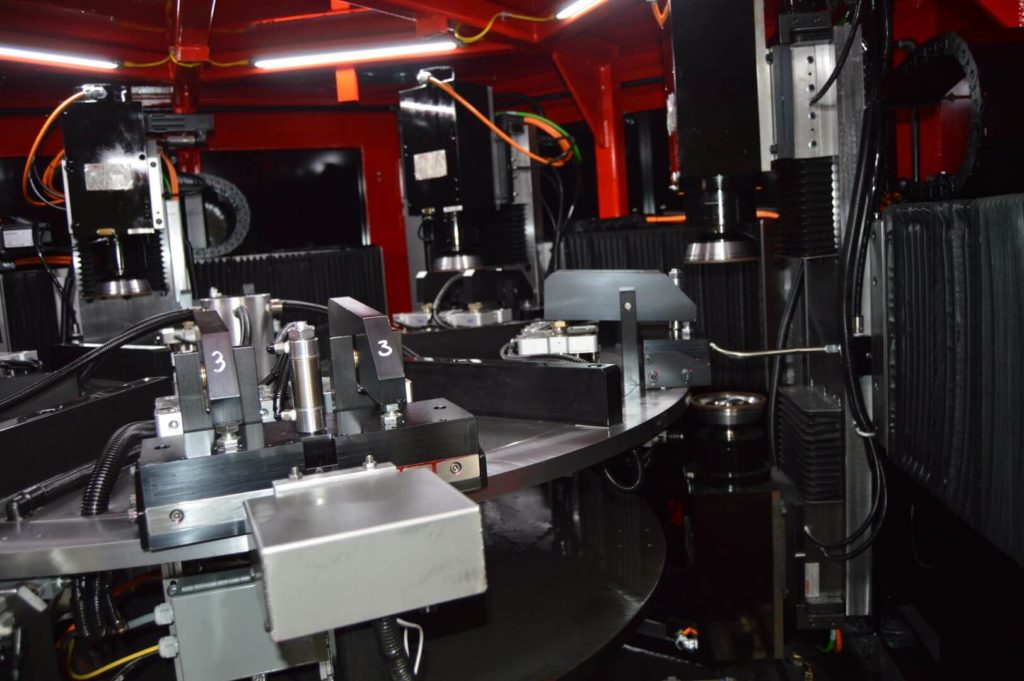
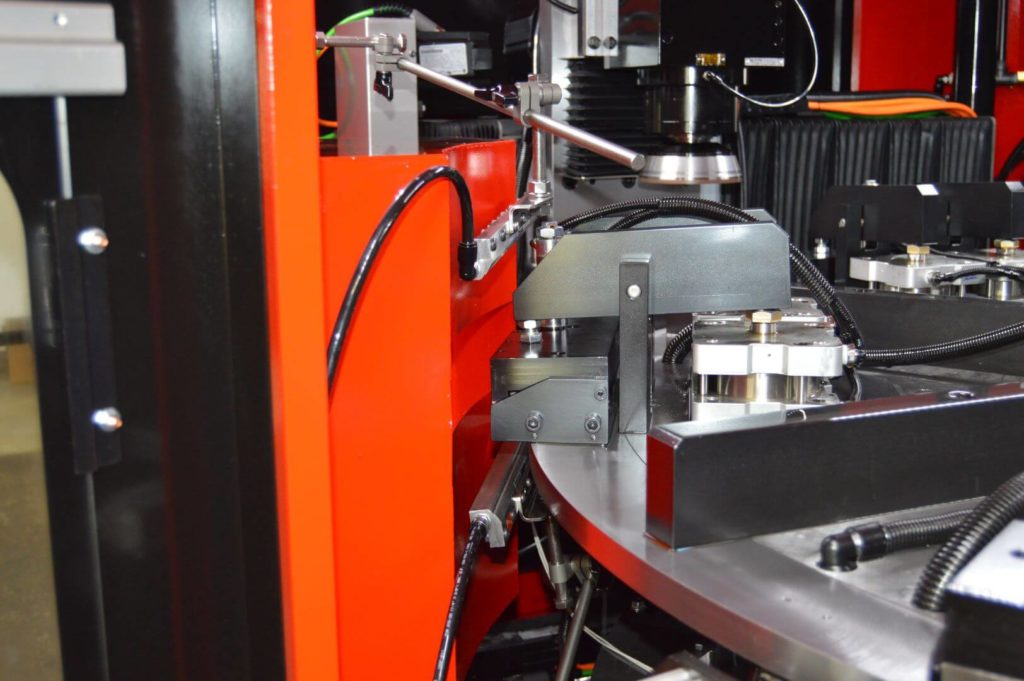
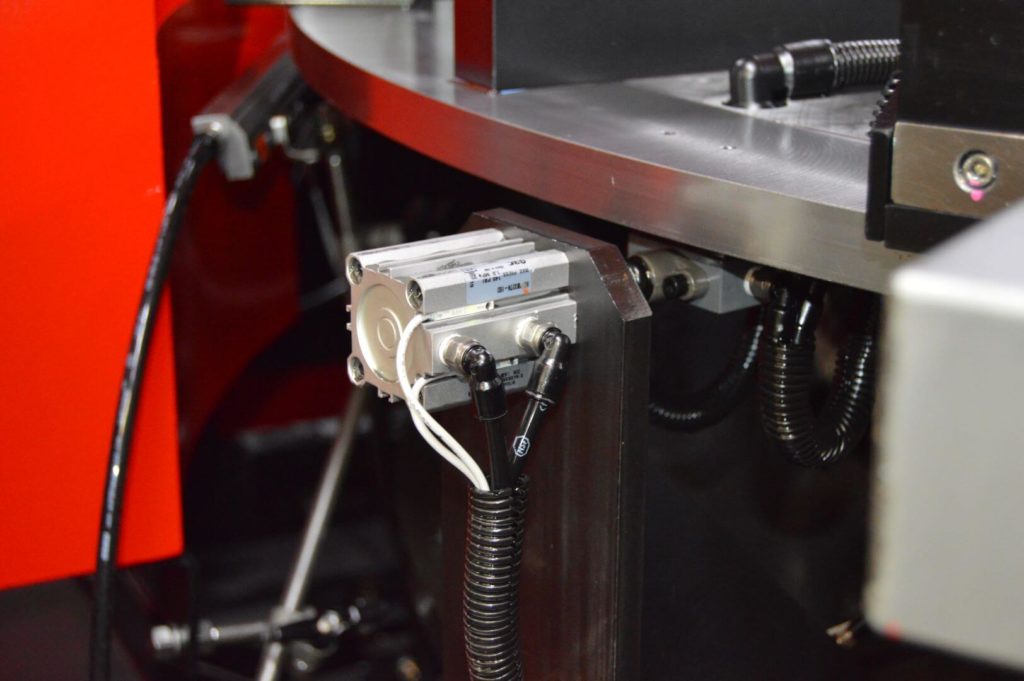
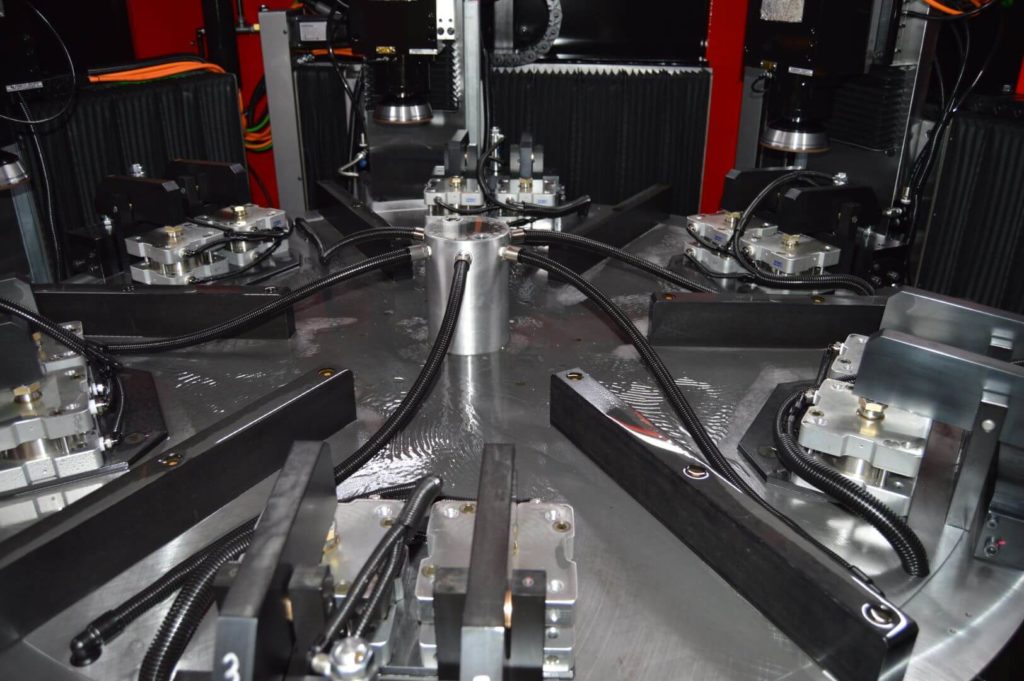
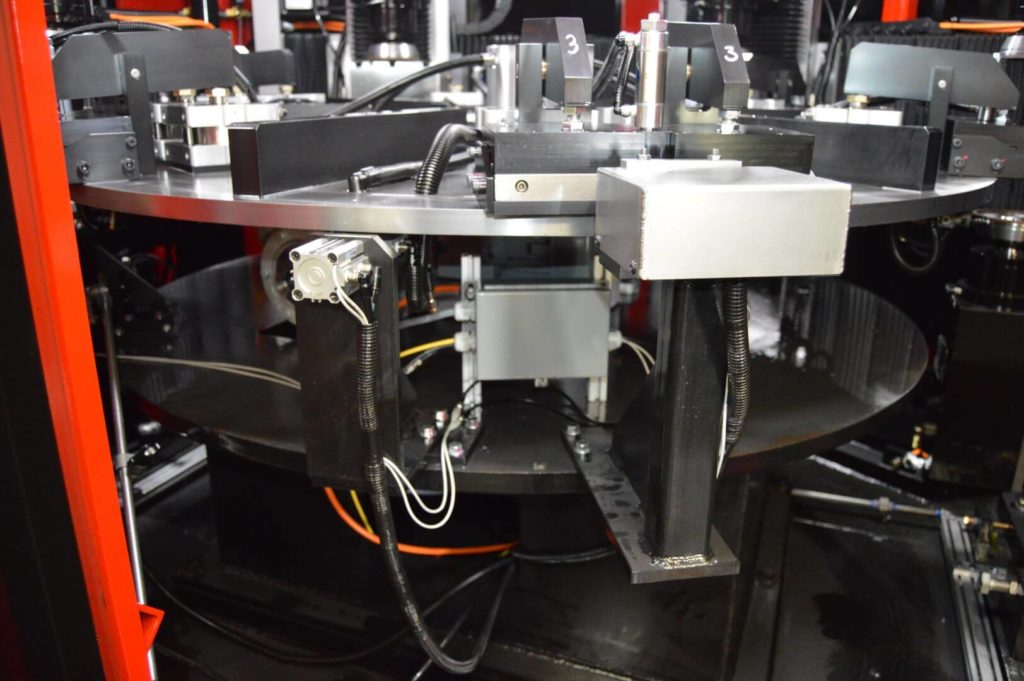
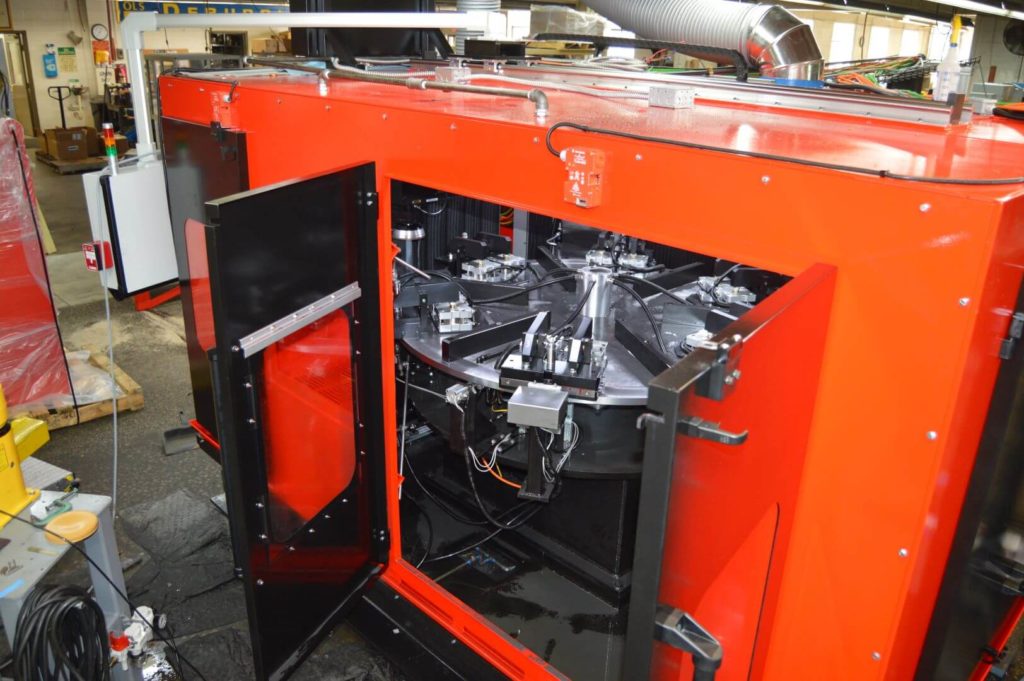
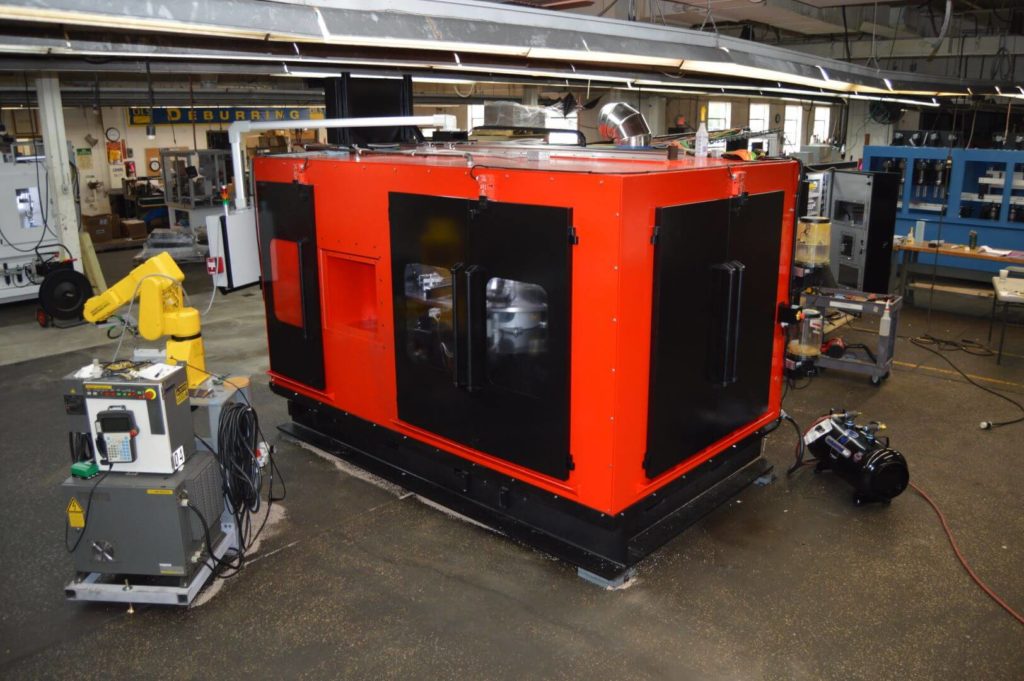
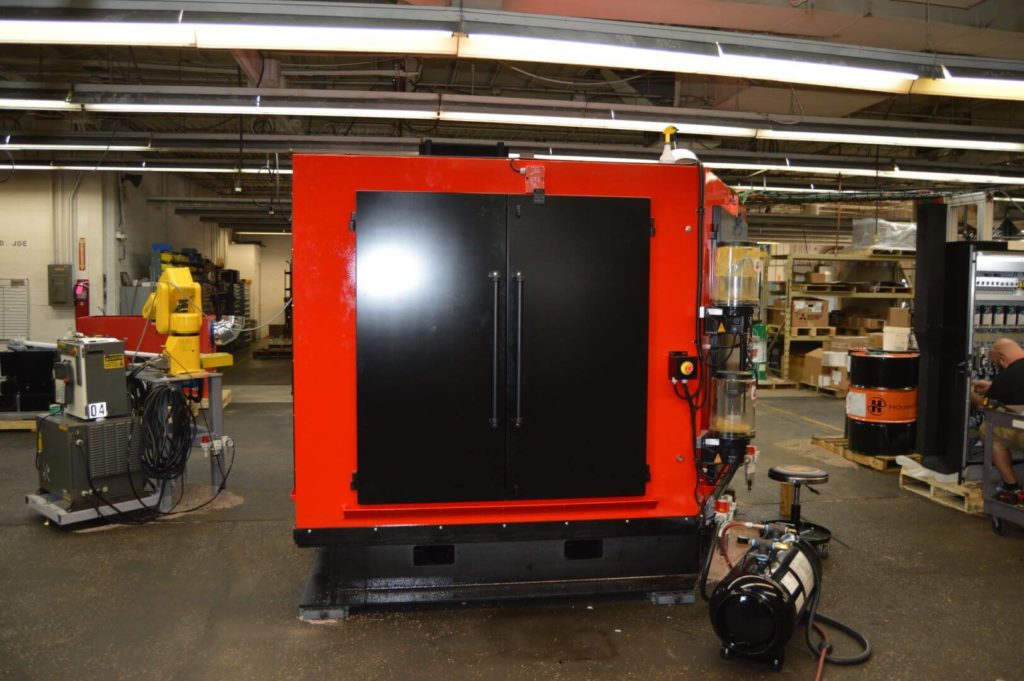
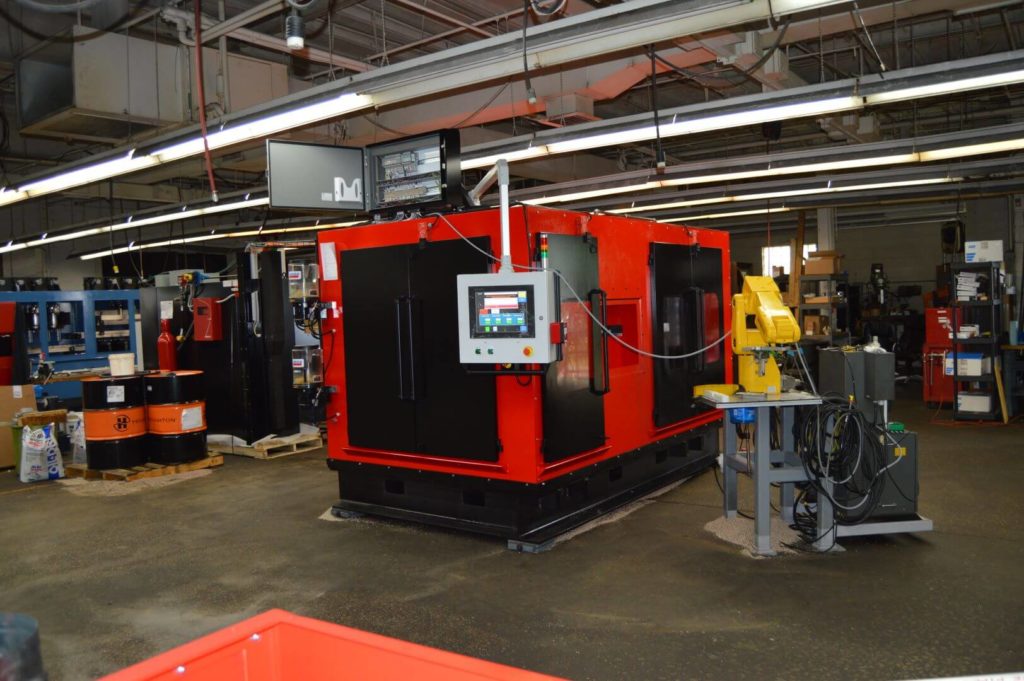
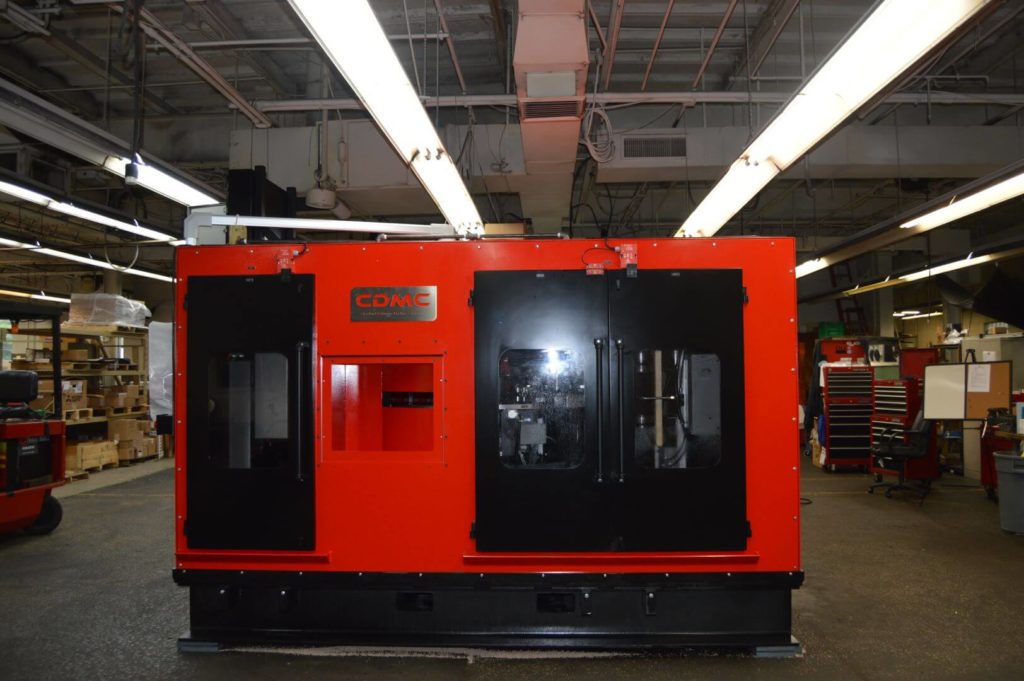
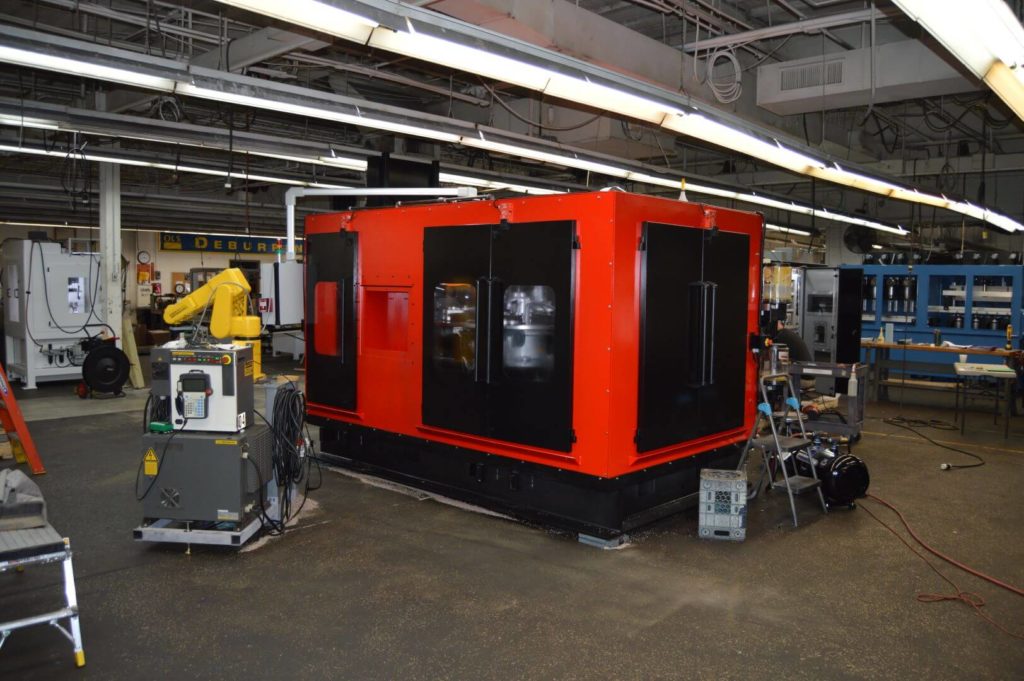
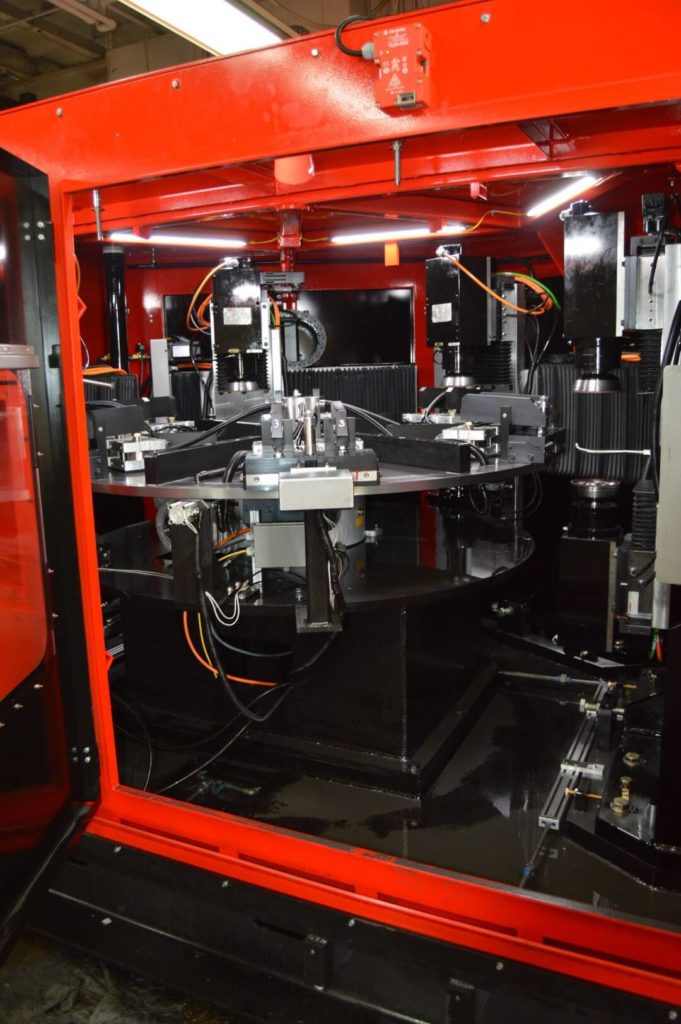
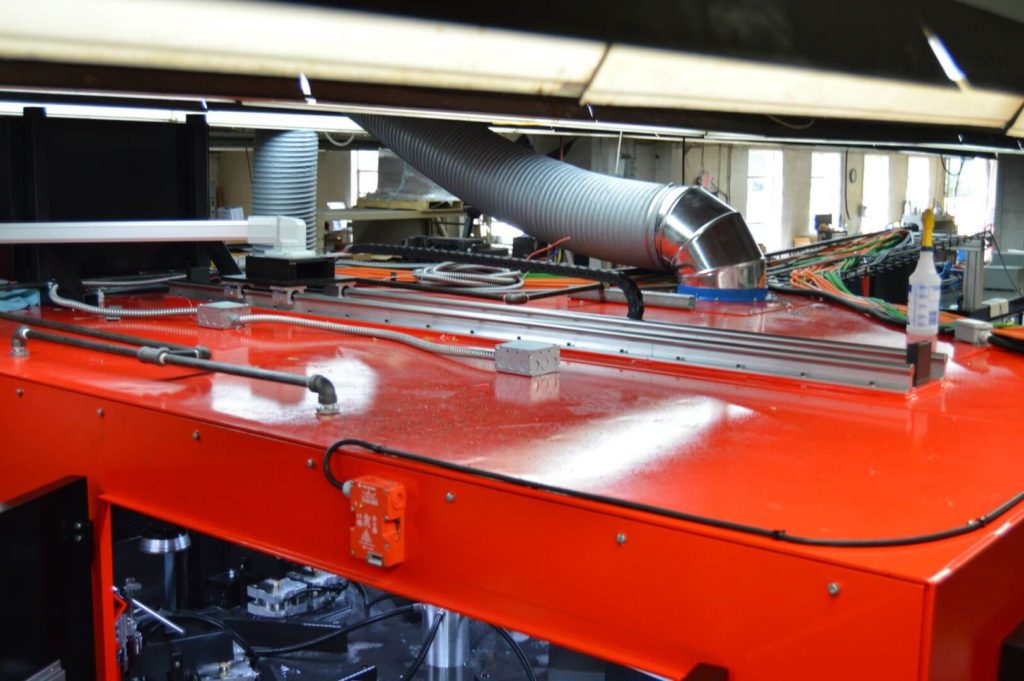
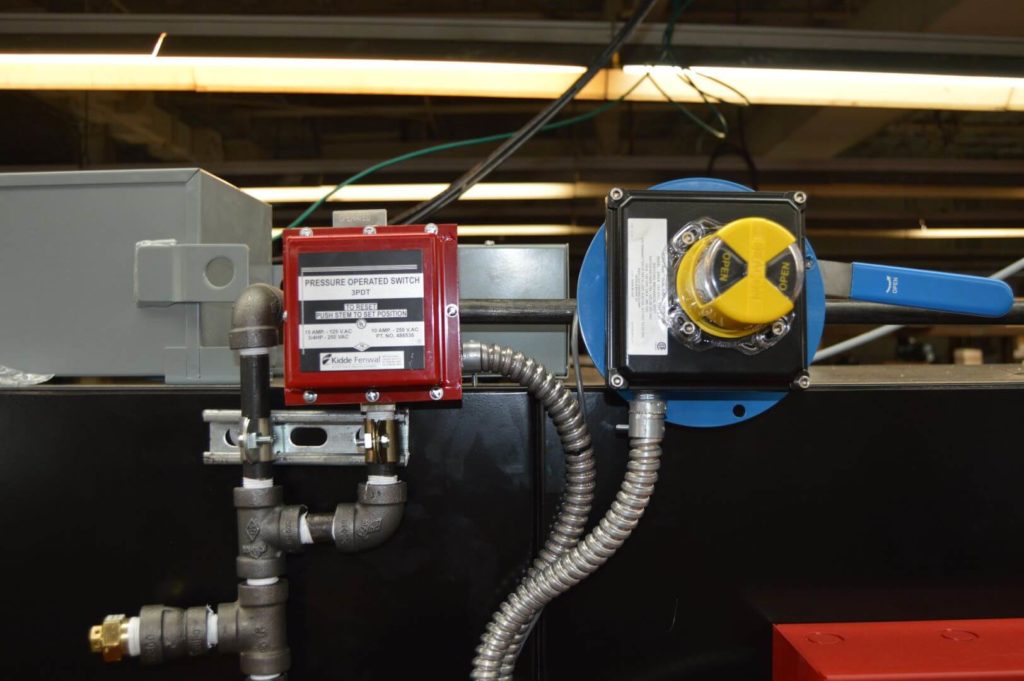
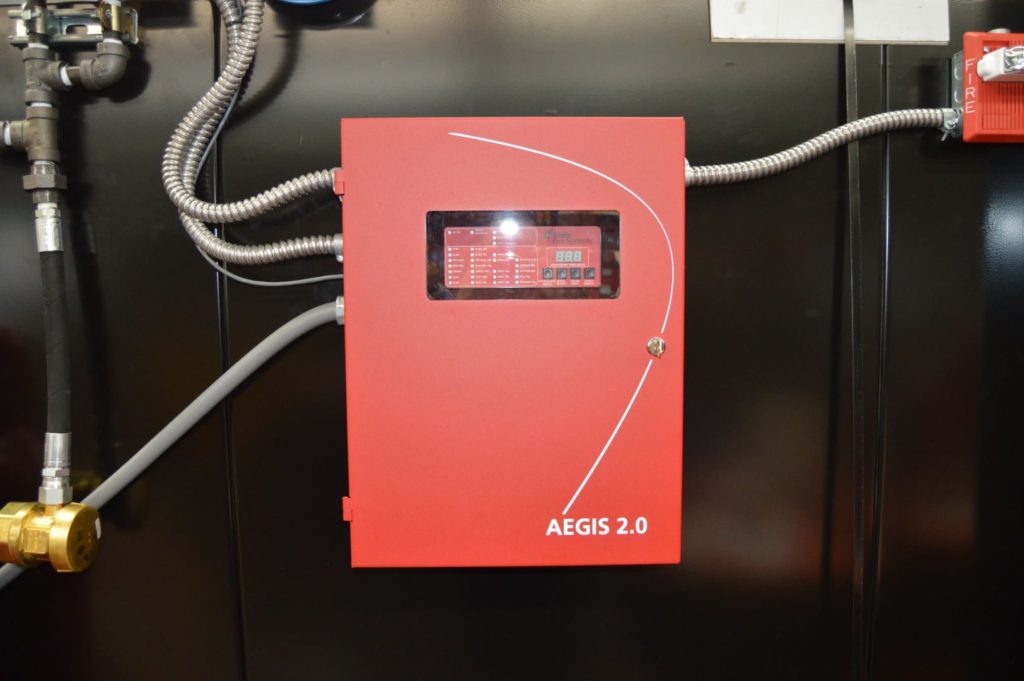
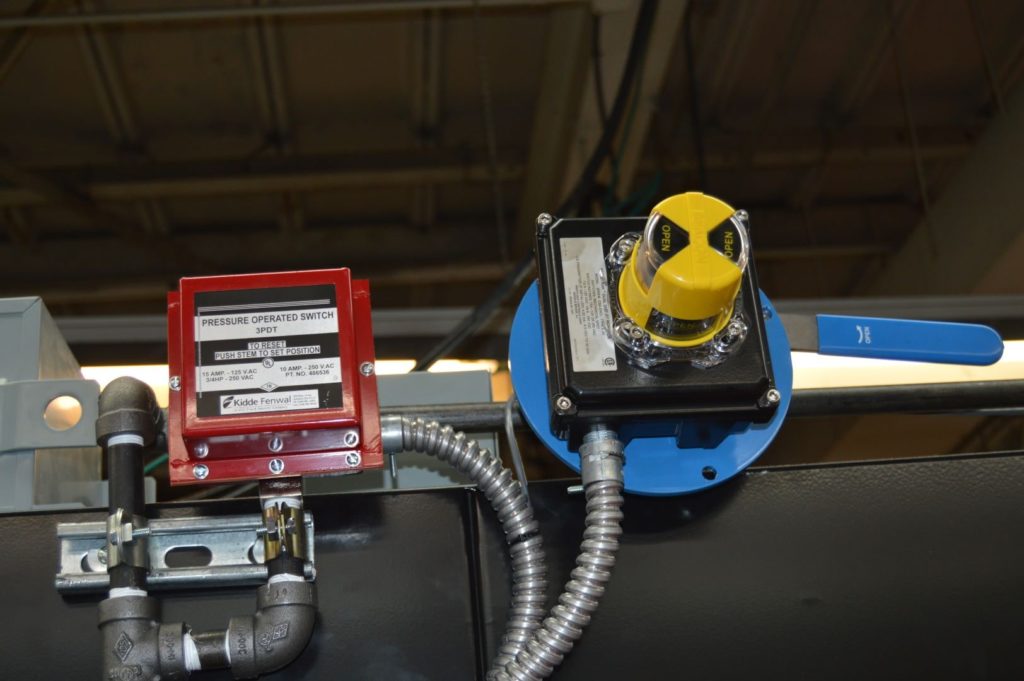
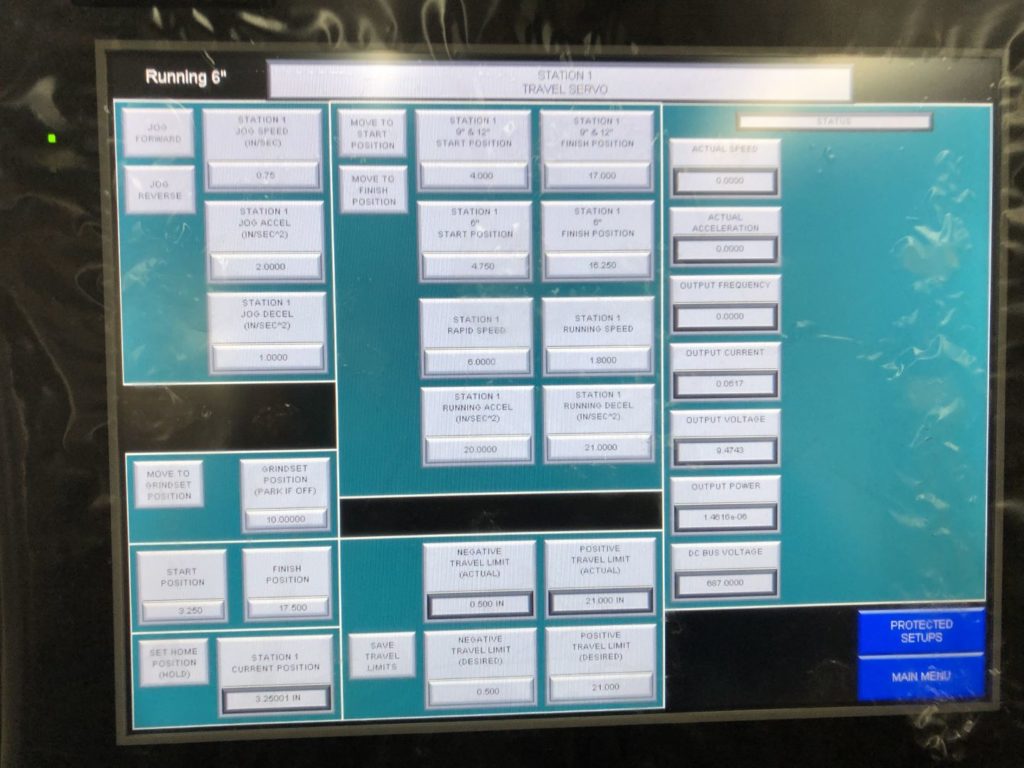
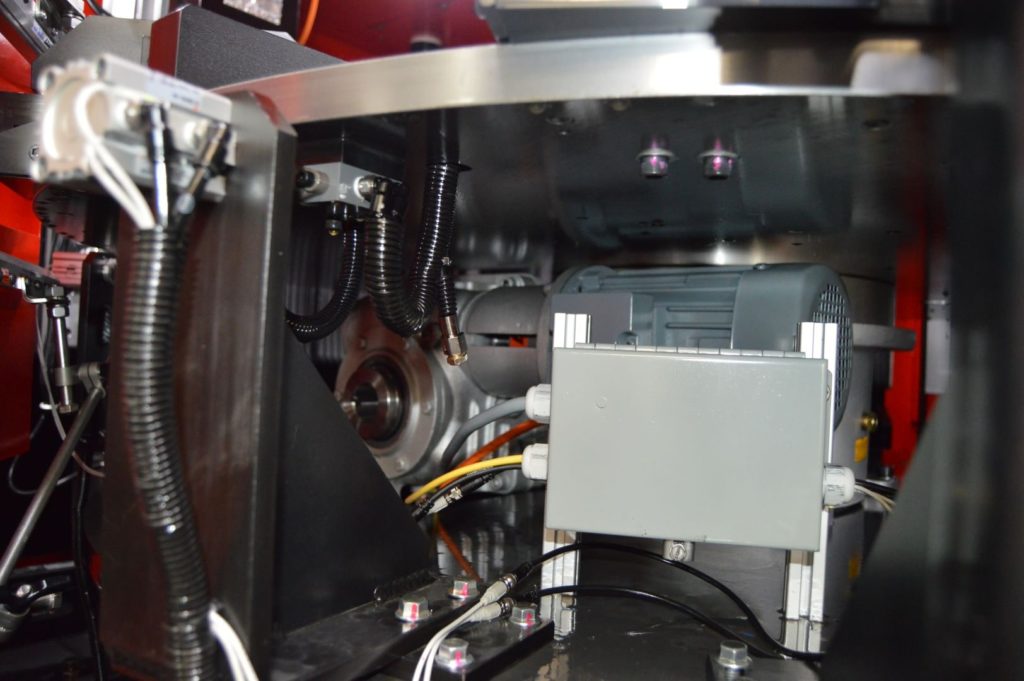
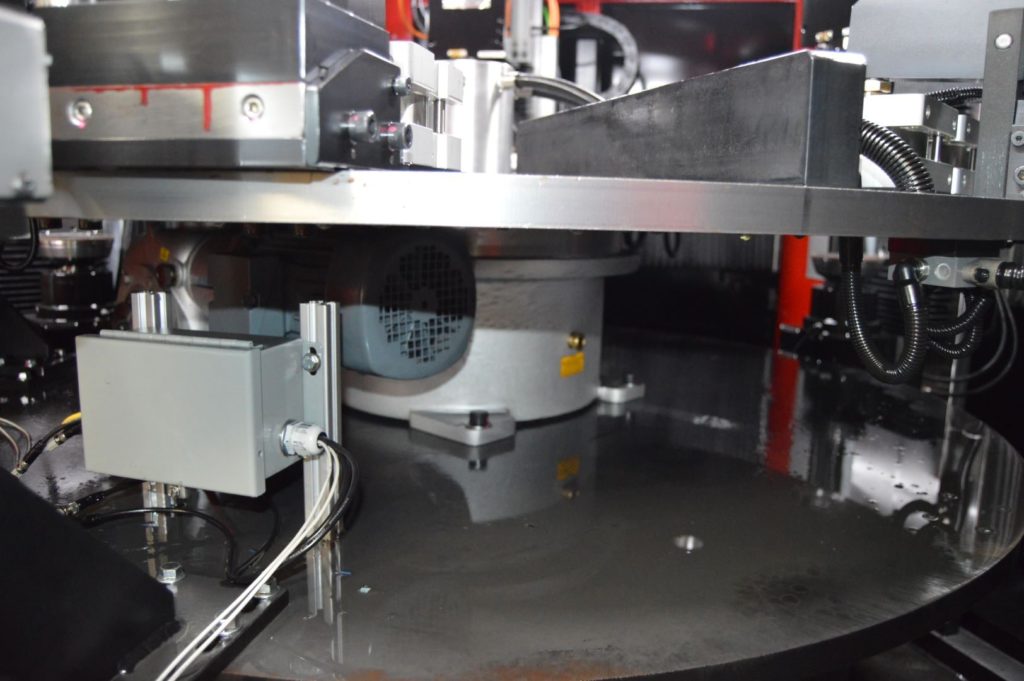
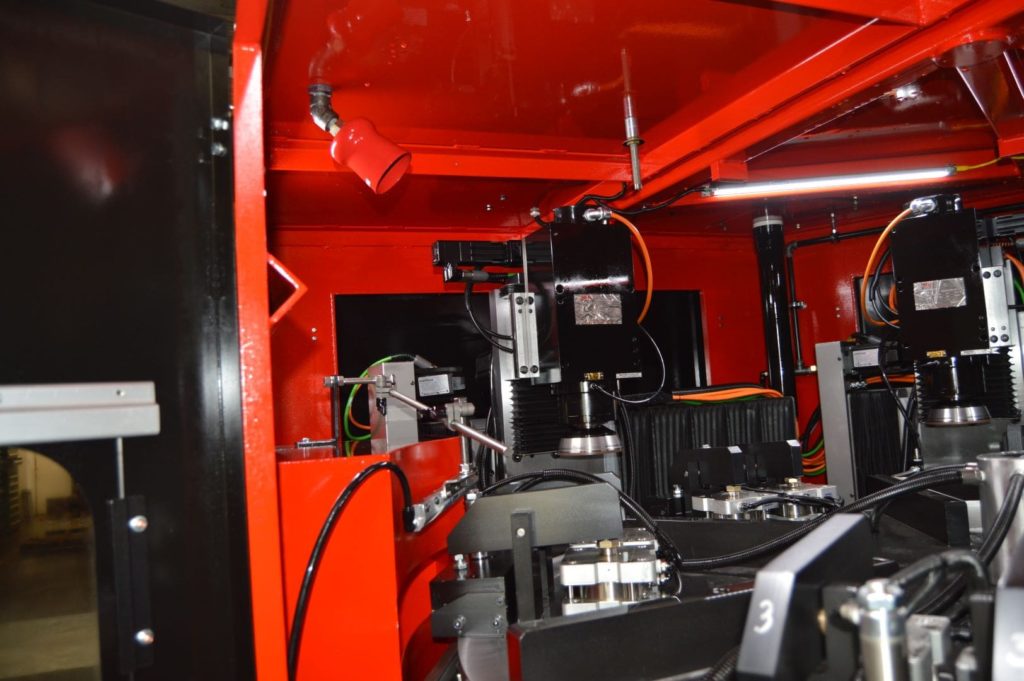
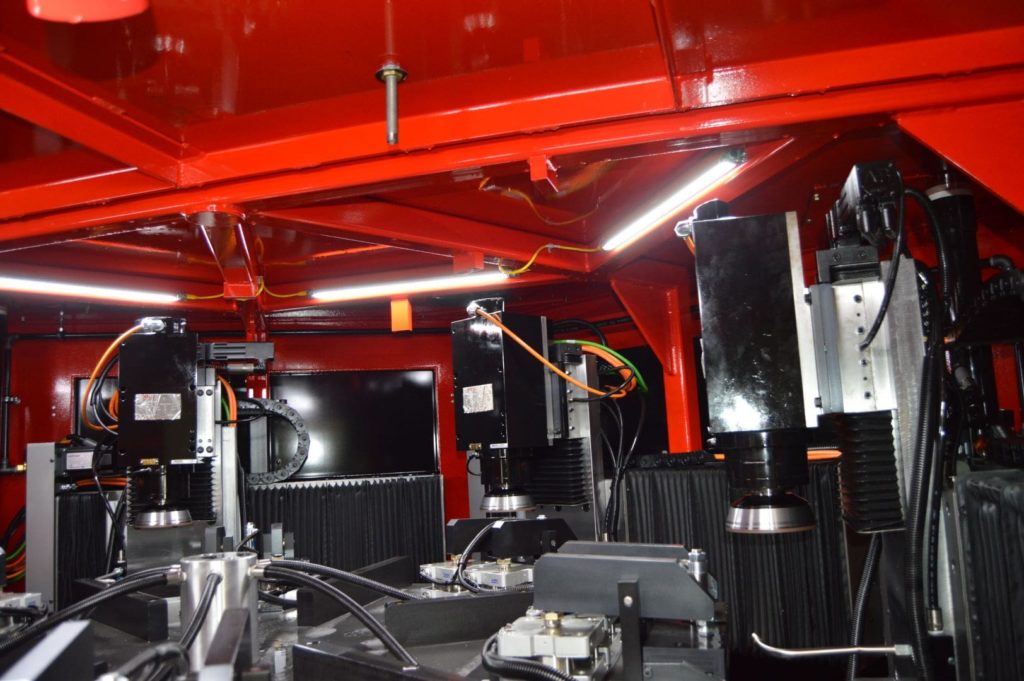
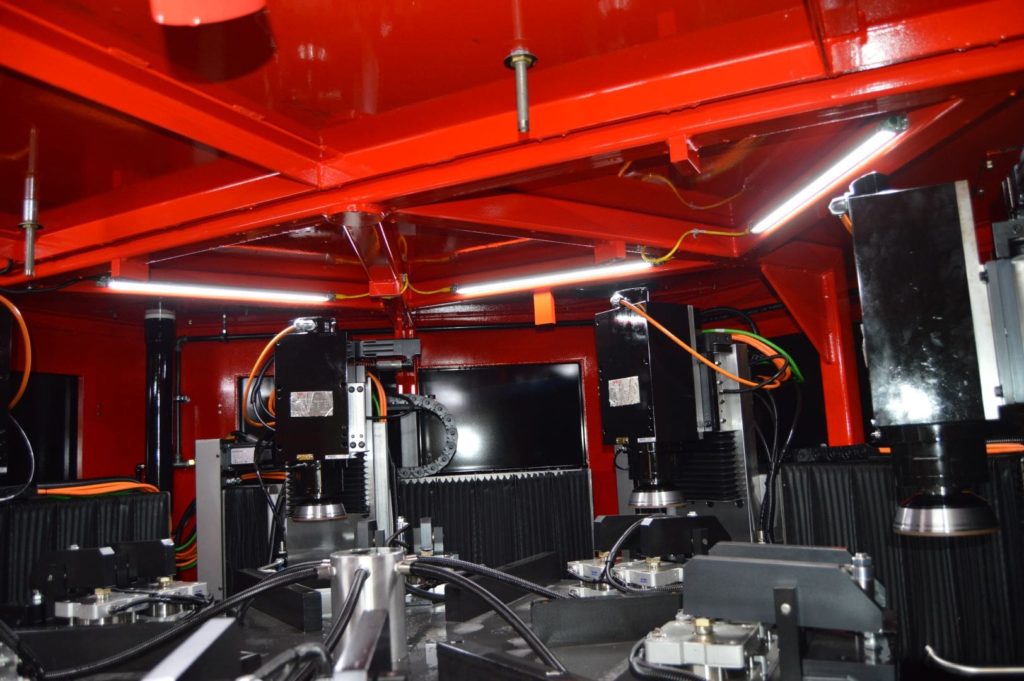
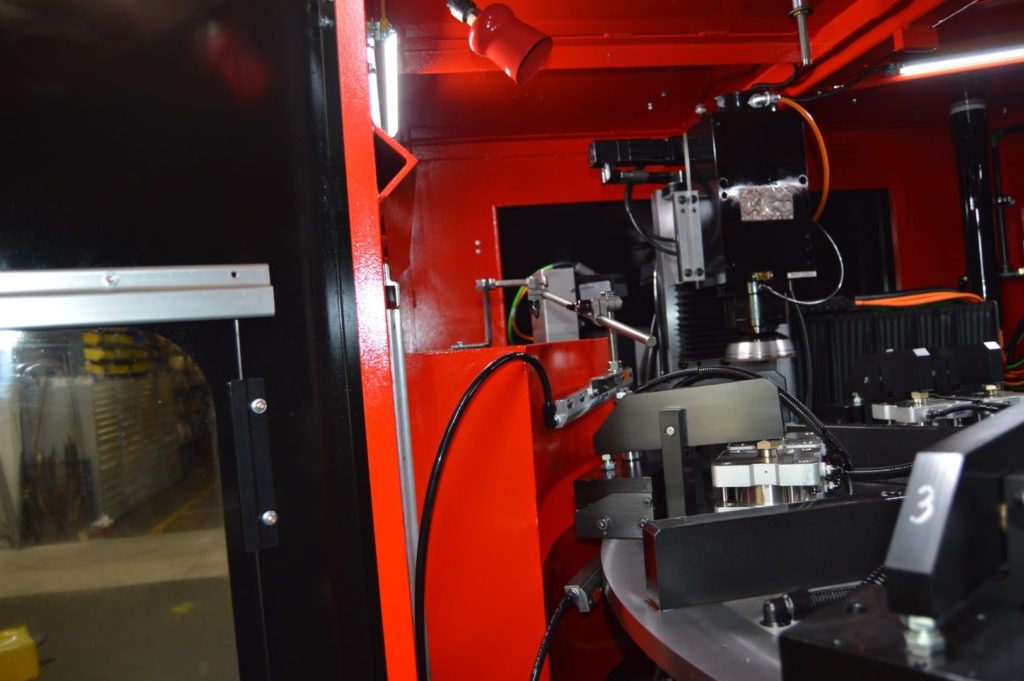
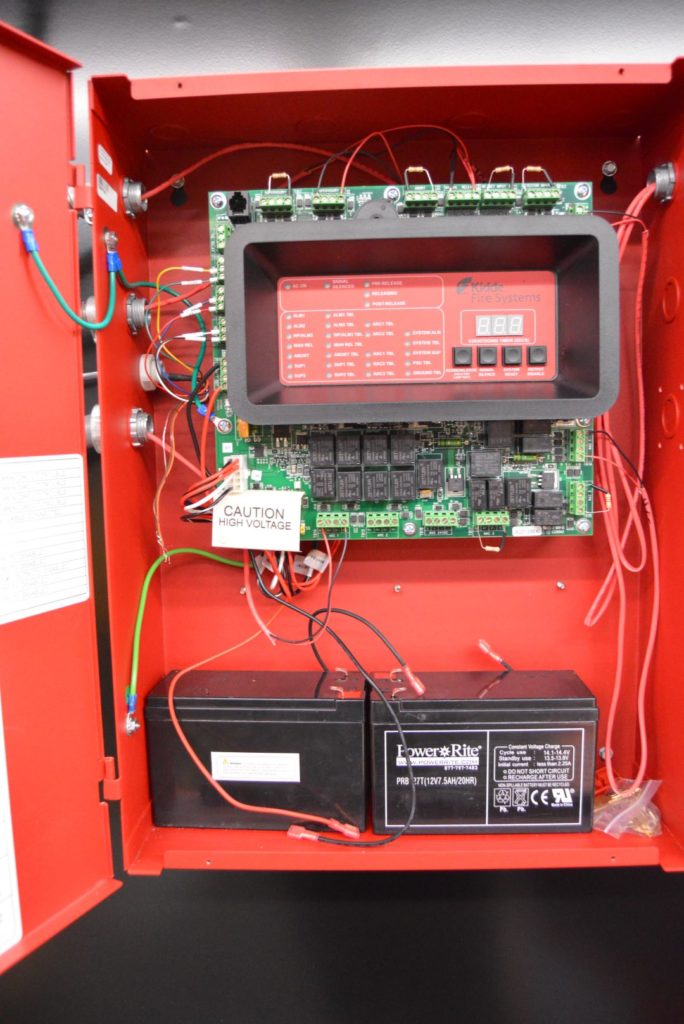
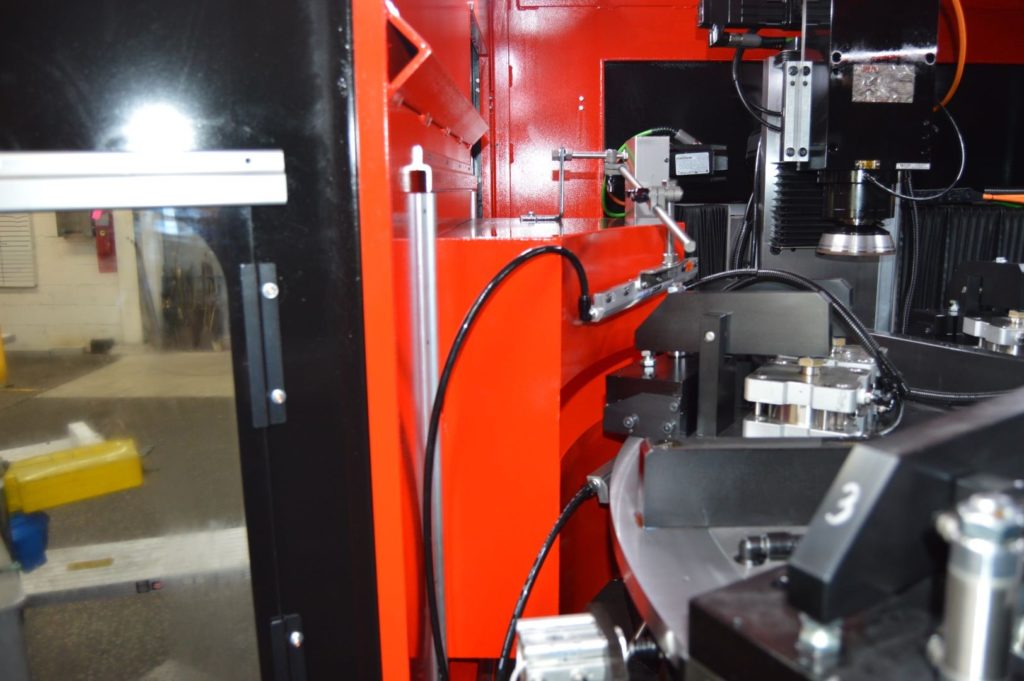
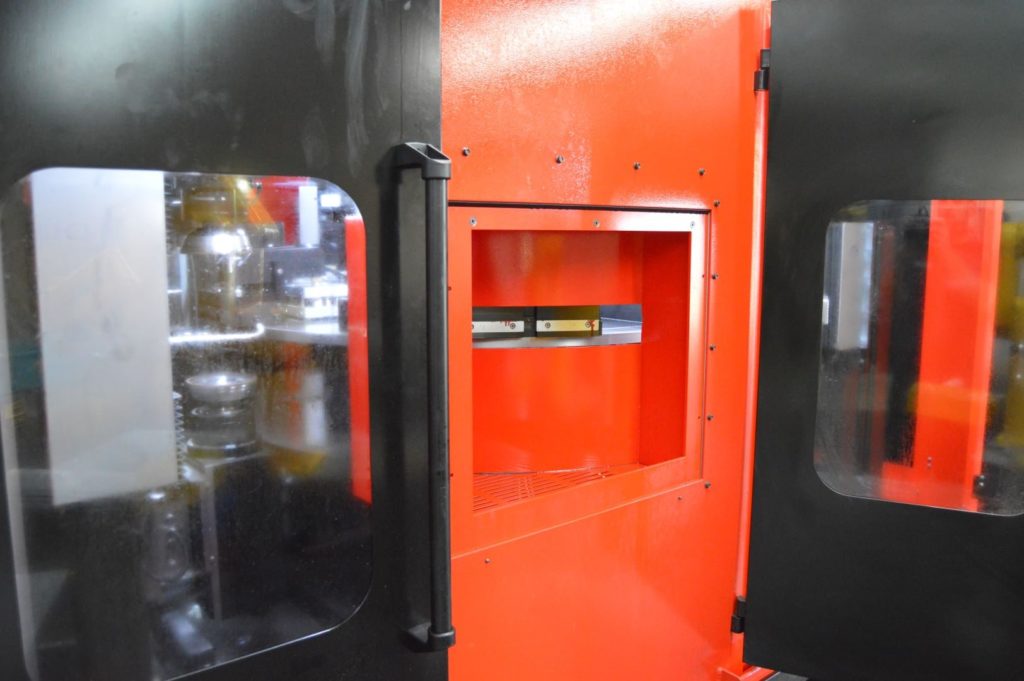
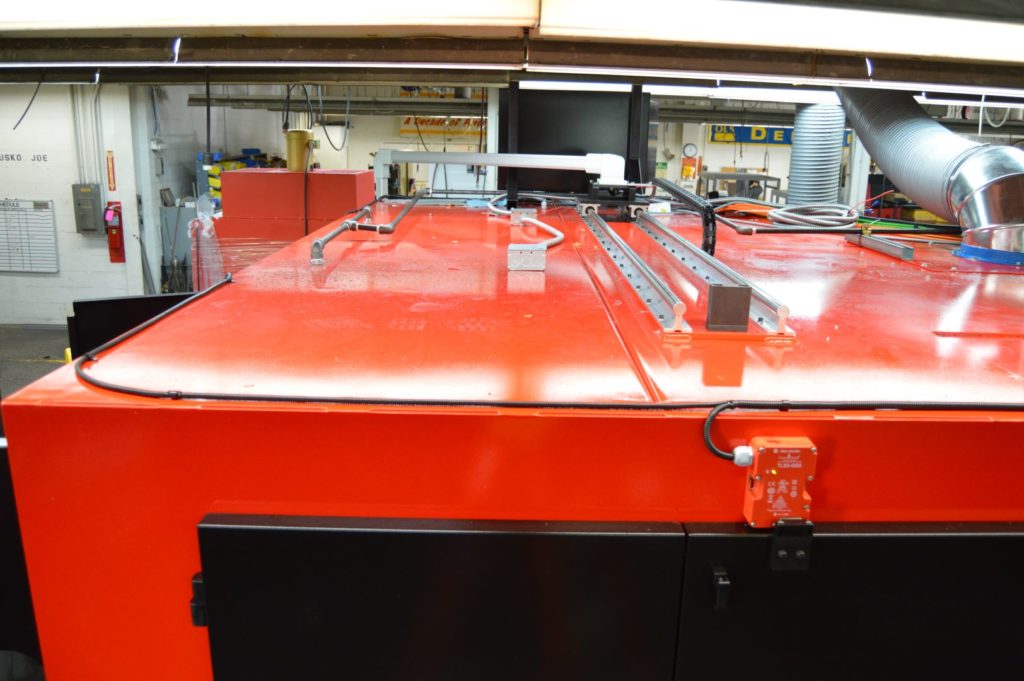
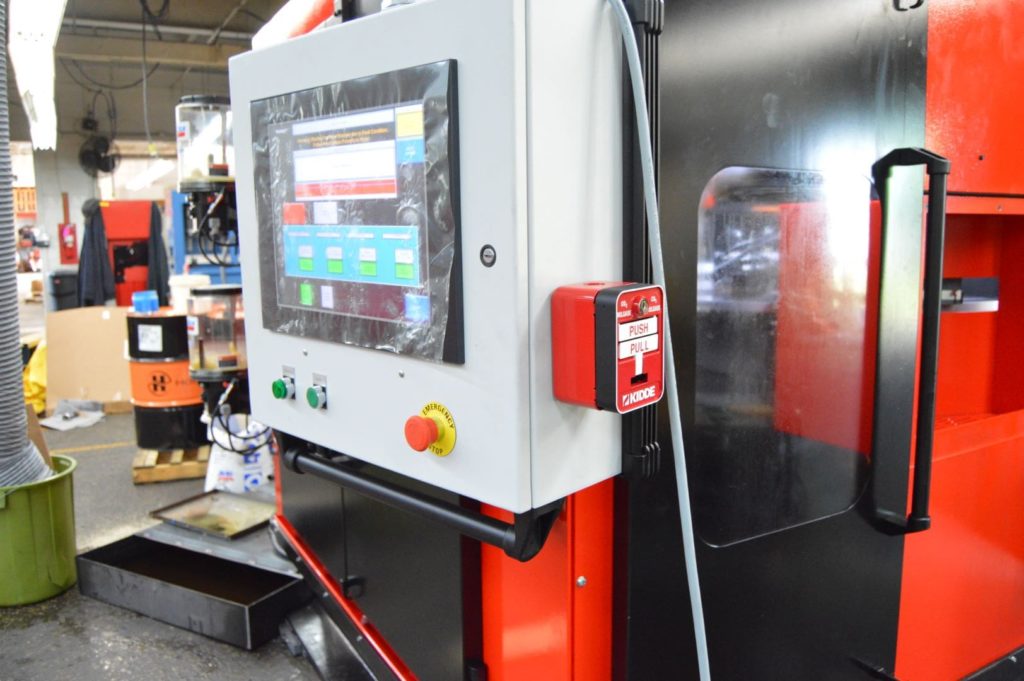
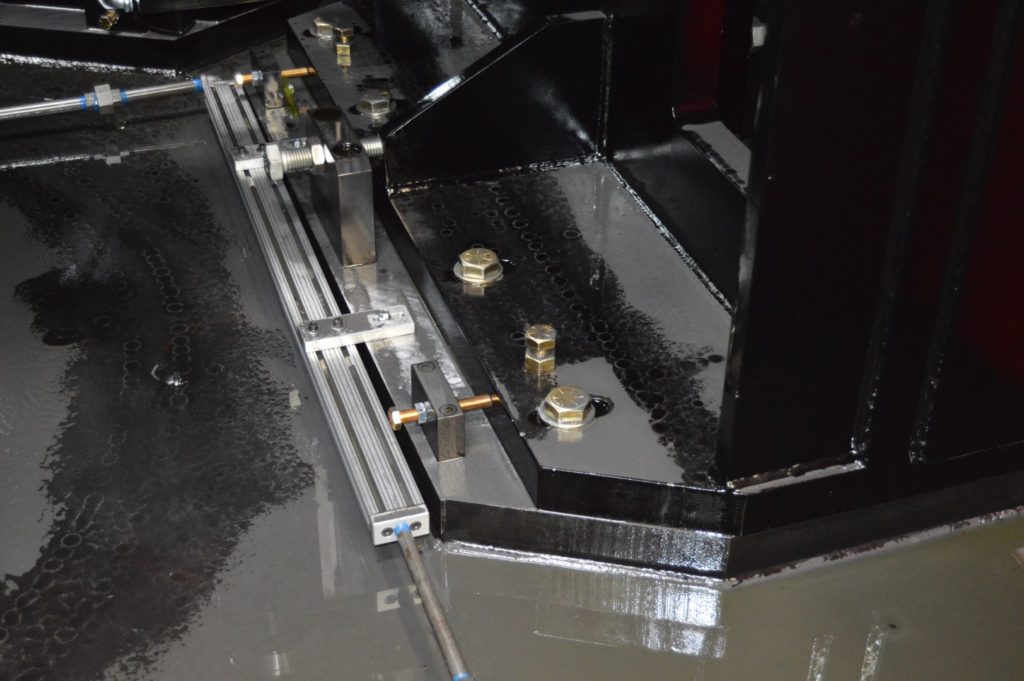
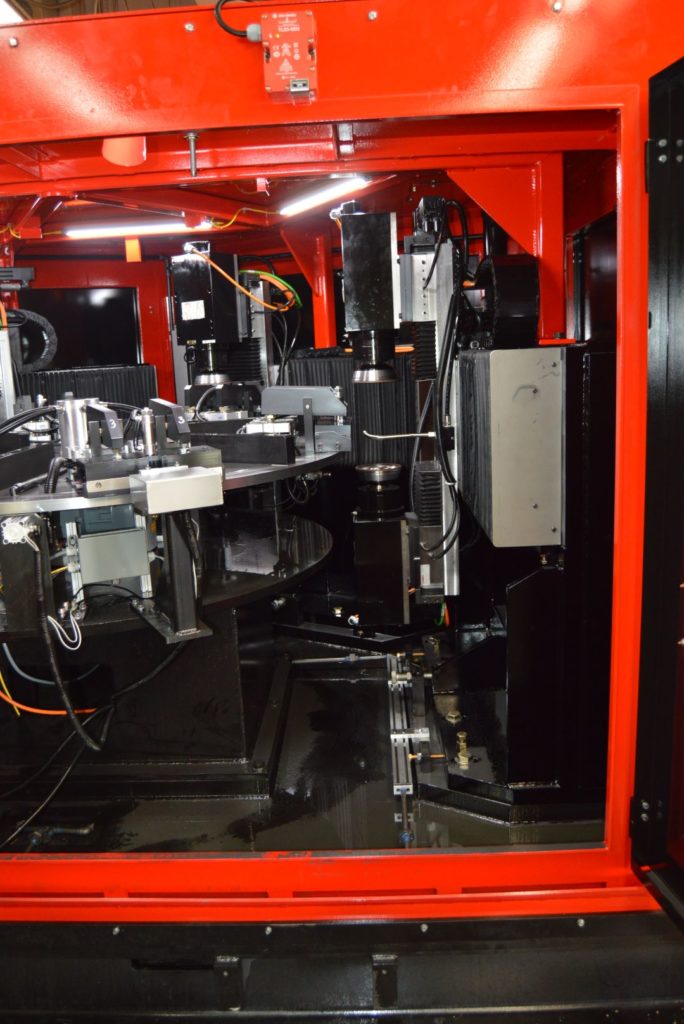
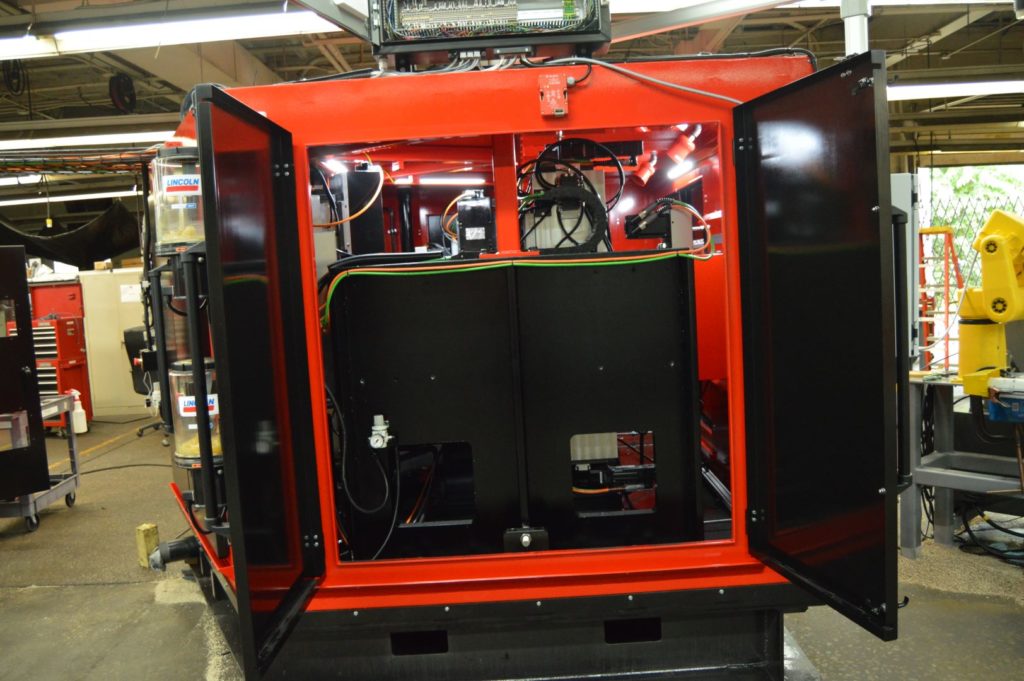
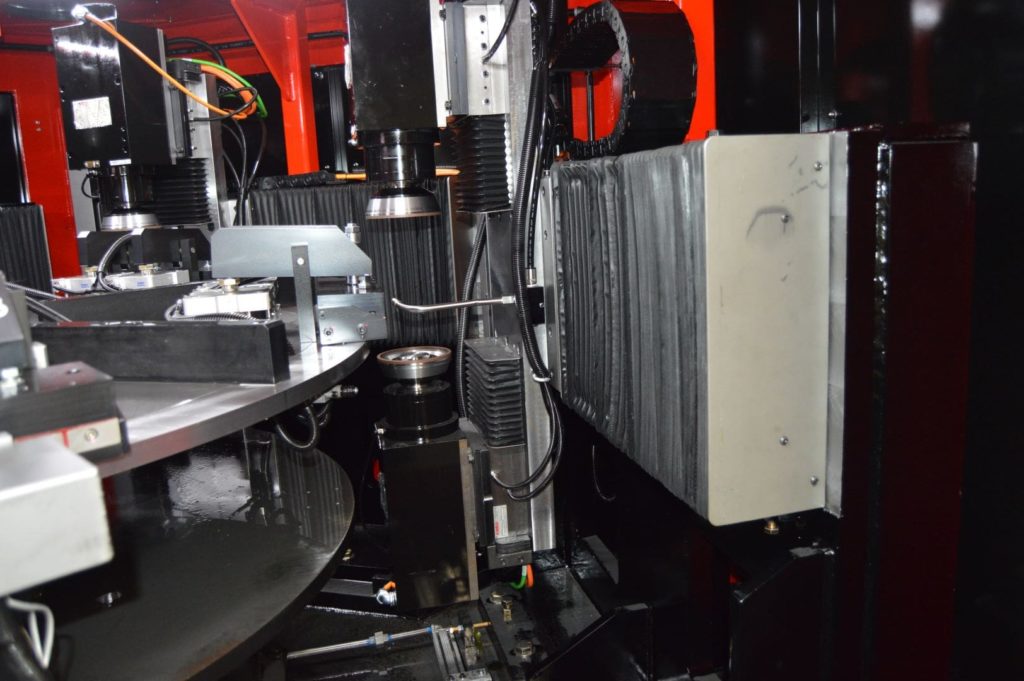
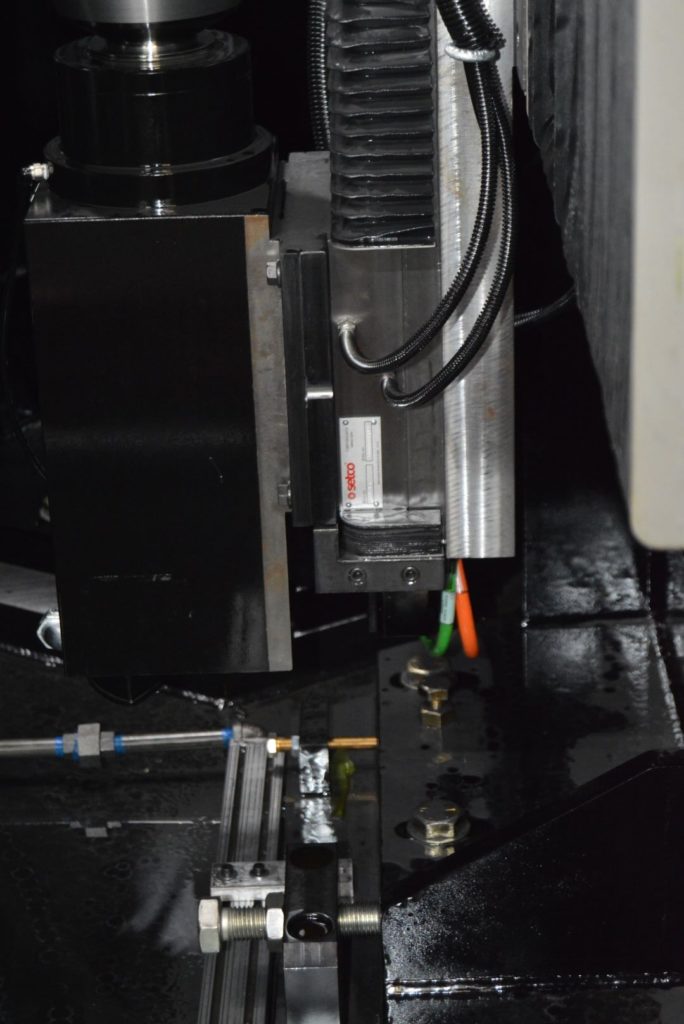
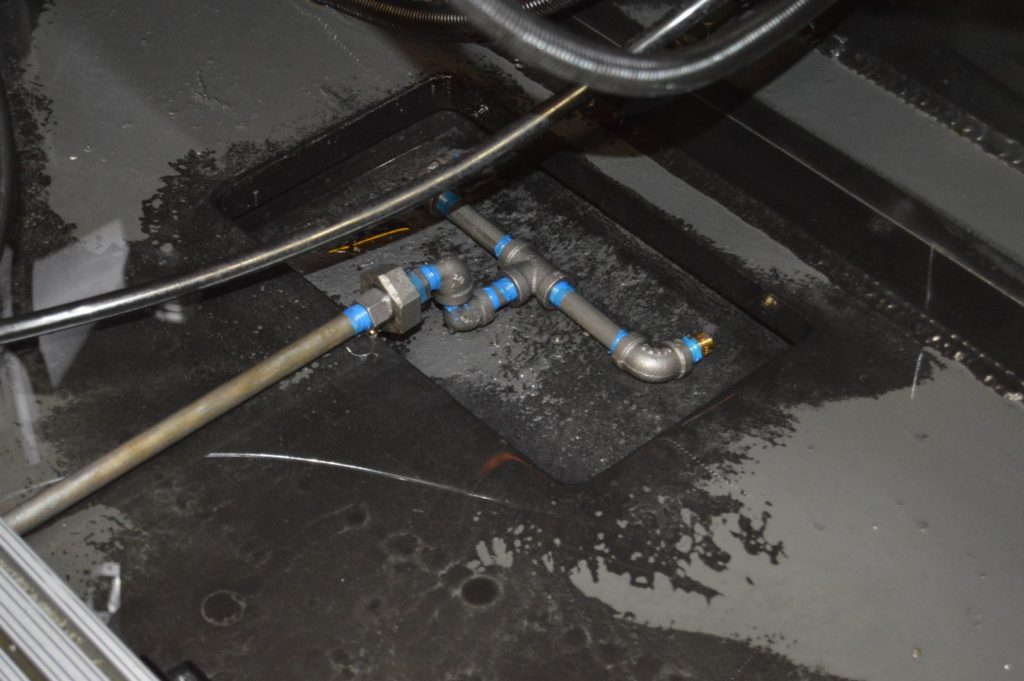