Aerospace Bushing Deburring and Finishing
JOB NO. 301
BUSHING DEBURRING W/ROBOT LOADER
APPLICATION
A manufacturer of aerospace components needed inside/outside diameter deburring solutions for a large family of brass aircraft bushings. Burrs were created during the machining of grooves and lubrication ports. The wide range of ring diameters required a large custom tooling package, from quick change drive tooling, to brush tooling to accommodate the various brush sizes needed. The customer was in contact with an outside company to provide a work stacking machine that would feed our application. The customer preferred to load/unload each station with a long reaching robot. Due to the size of the application at hand, an industrial fence would have to be placed around the work area along with any/all required safety implements.
SOLUTION
Machine Base
This application utilizes an off-the-shelf base design provided by one of our many available contract fabricators. The ability to use a pre-fabbed base saves capital for all parties involved.
Processing
- OD burrs are treated with a 14” nylon brush directly driven by a large D.C. motor. A pivot assembly is used to bring this brush to the work and home positions. When engaged, vertical and horizontal motion is controlled by a pair of electronic linear slides. Utilizing Auto Amp Compensation, the PLC program will use amperage feedback from the brush motor to determine cut pressure.
- ID burrs are treated by a similar nylon brush, but in a wide range of diameters. This brush is driven by an output shaft and collet. The collet assembly is driven by an electric motor via offset belt drive. This process utilizes Auto Amp Comp as well.
- All feeds/speeds pertaining to brushes, work rotation and cutting head travel are adjustable within the program via HMI screens.
- Part drive assemblies are outfitted by pneumatically actuated Kitagawa chucks outfitted with custom quick-change clamp tooling. This tooling is designed to maximize the ability to process various part family members without changeover, while being accessible and easily adjusted when necessary.
- With a number of personnel trained in FANUC robot programming, we are able to teach the robot loader to work with the customer’s preferred work stocker and teach all robot program logic in house. CDMC is also capable of manufacturing custom End of Arm Tooling for FANUC robots.
Safety
Any manual door/machine panel that does not require a hand tool to remove is equipped with electronic safety interlocks. Braking this interlock will stop/fault the machine instantly.
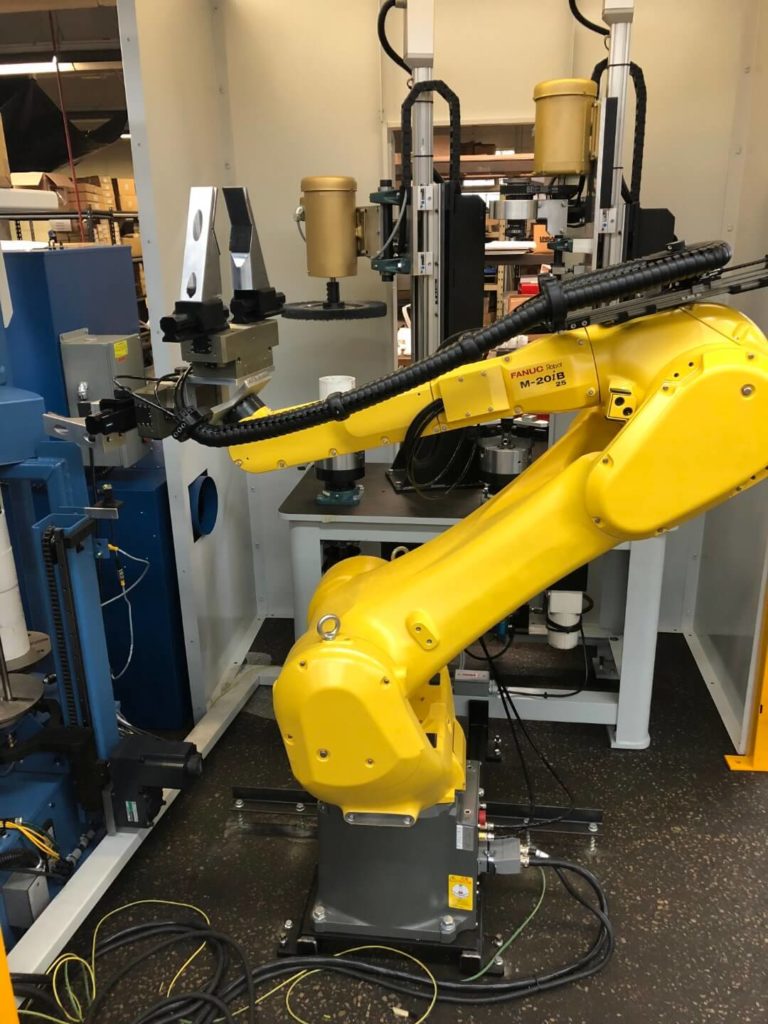
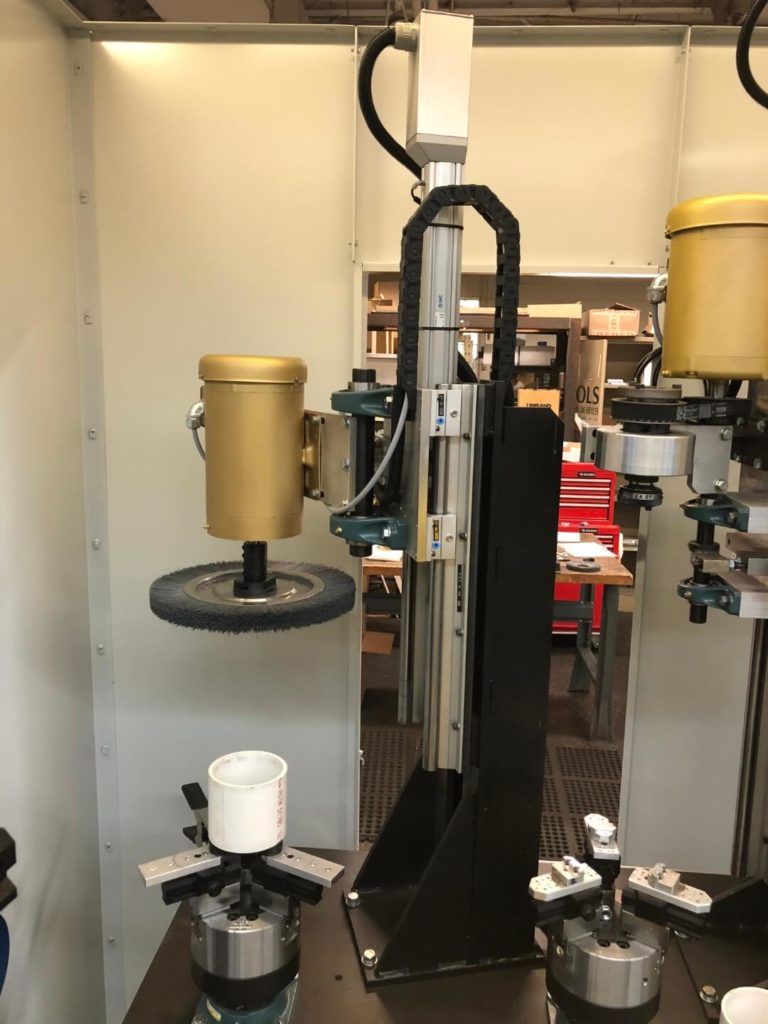
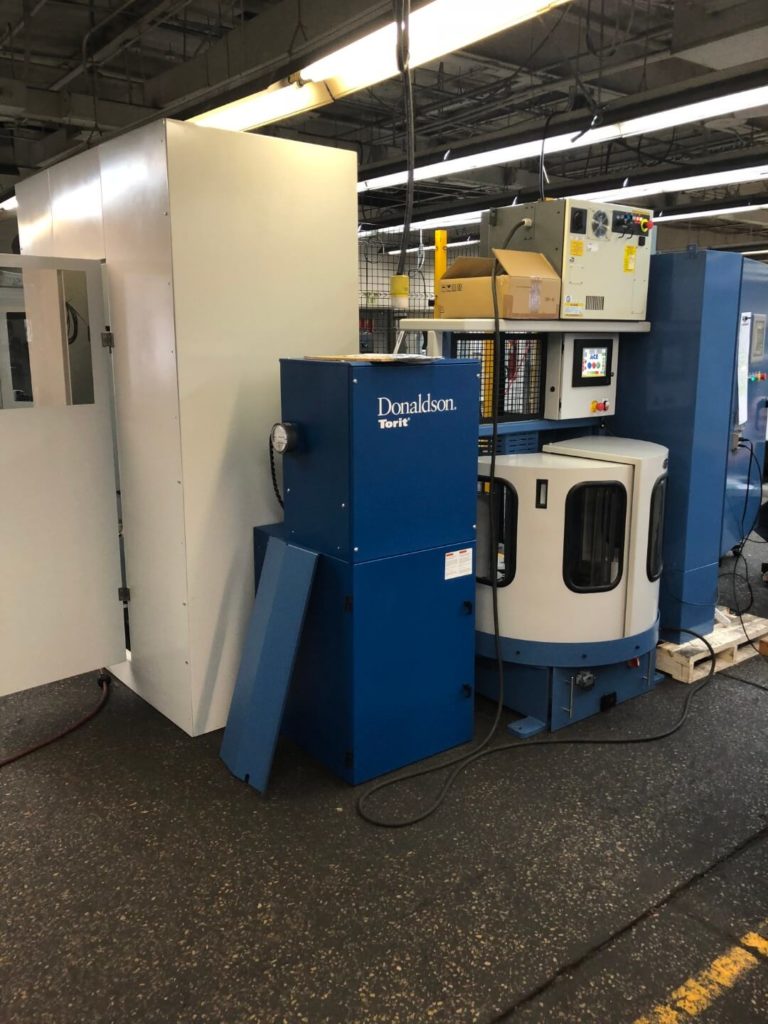
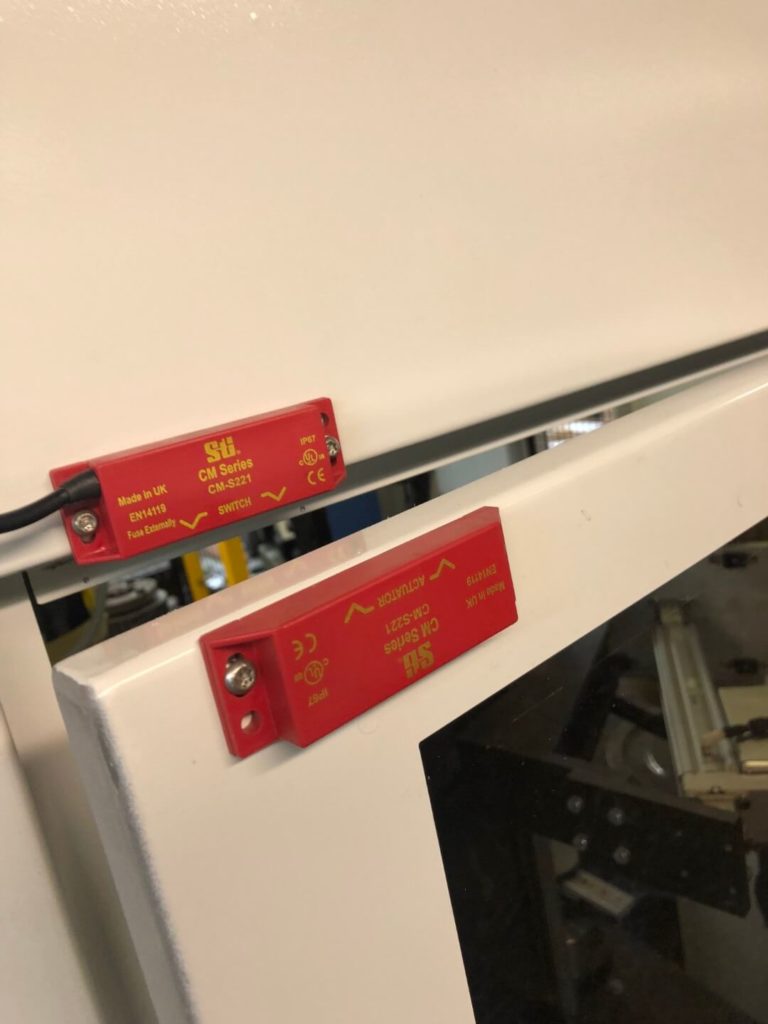
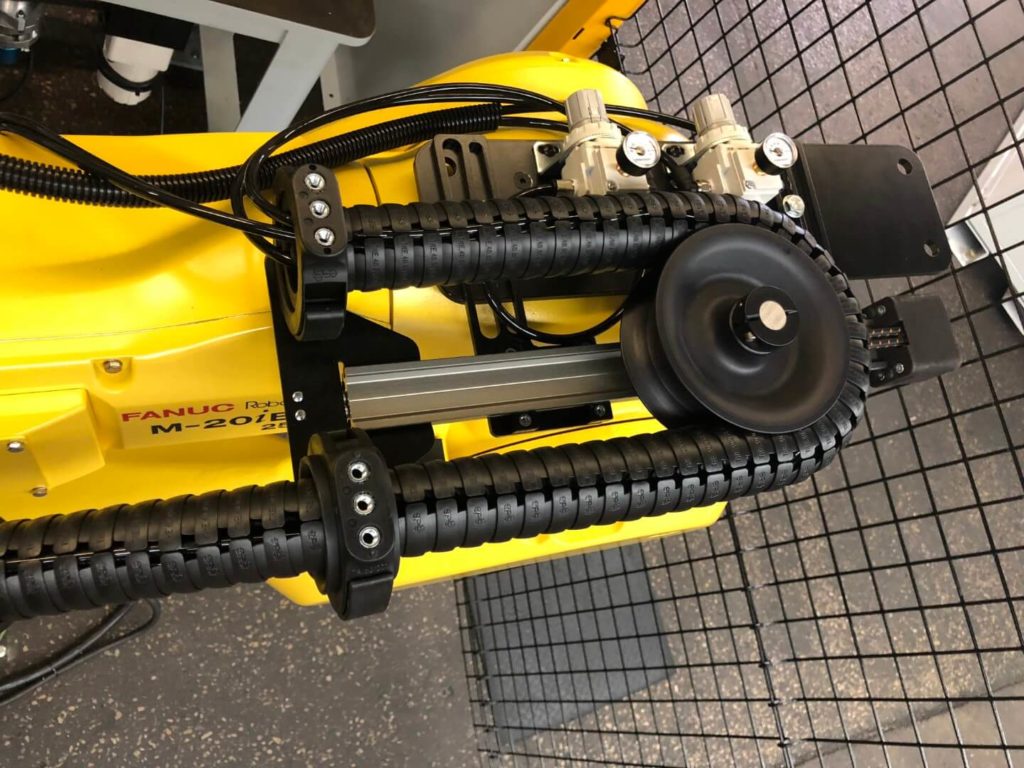
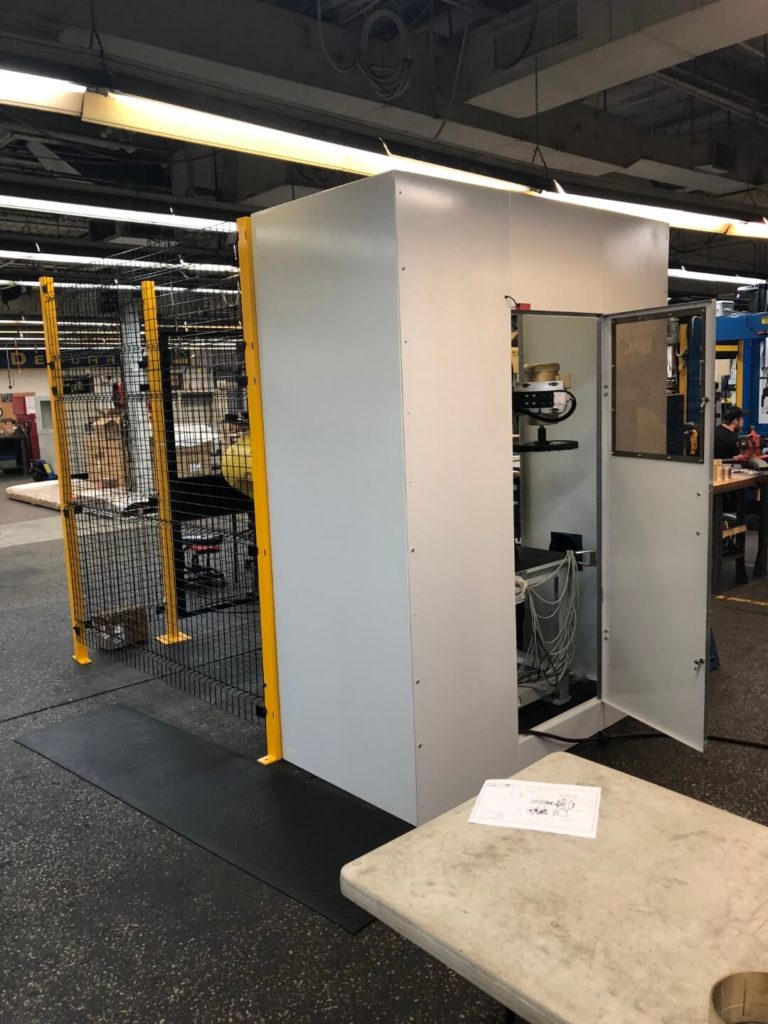
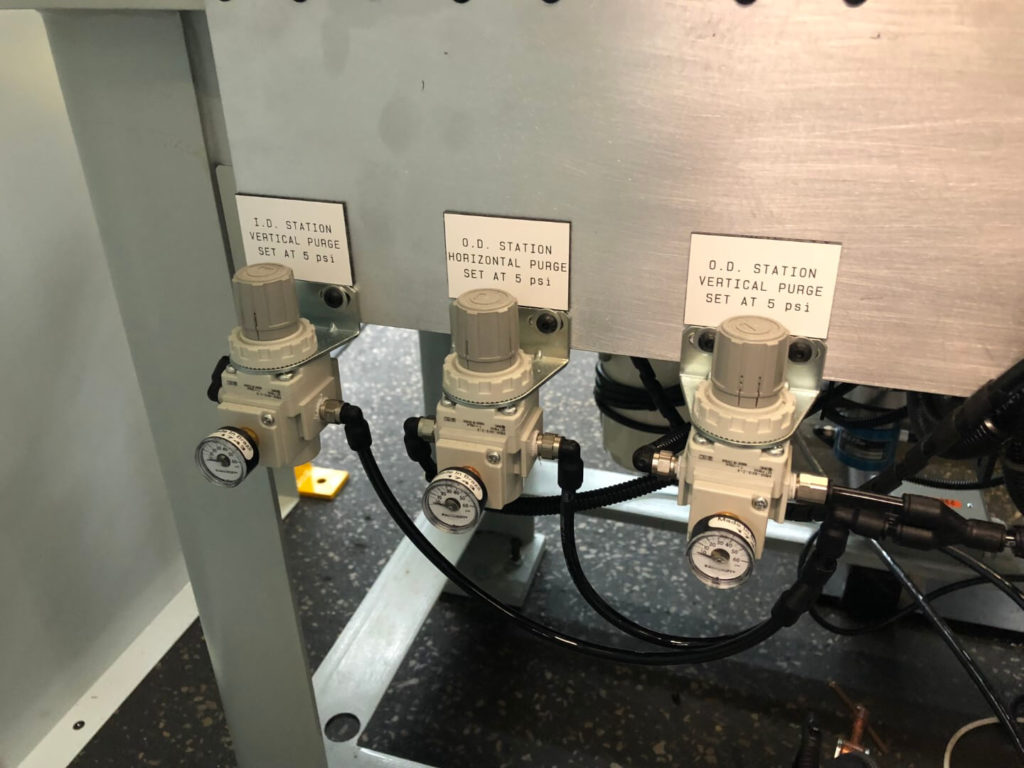
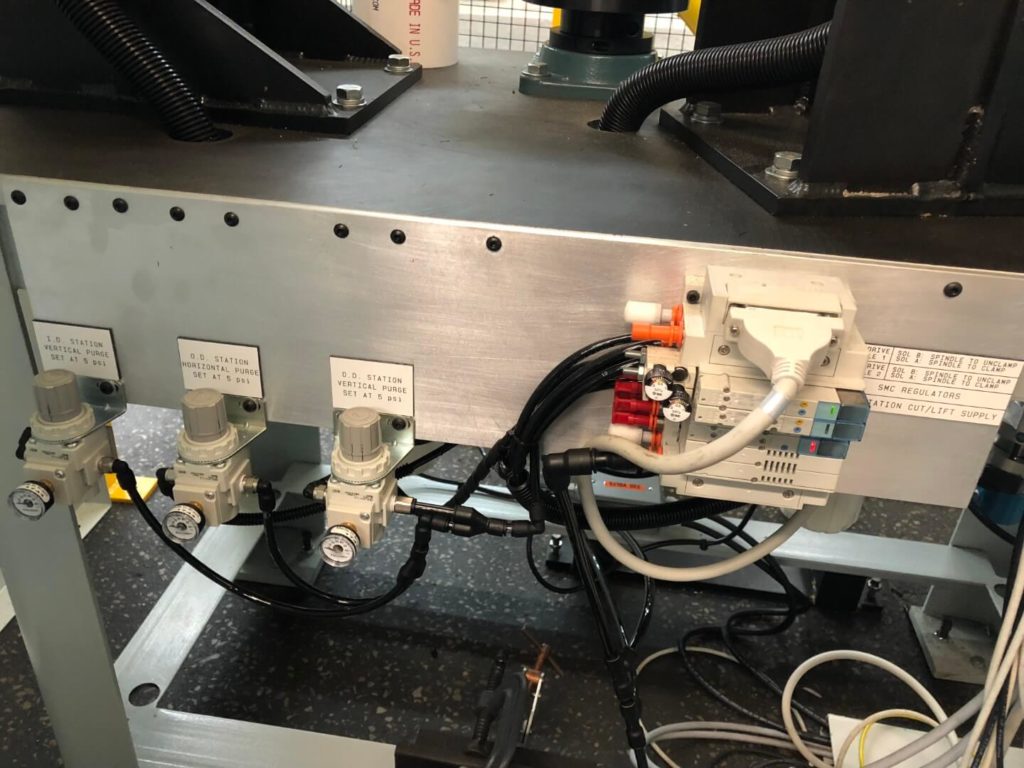
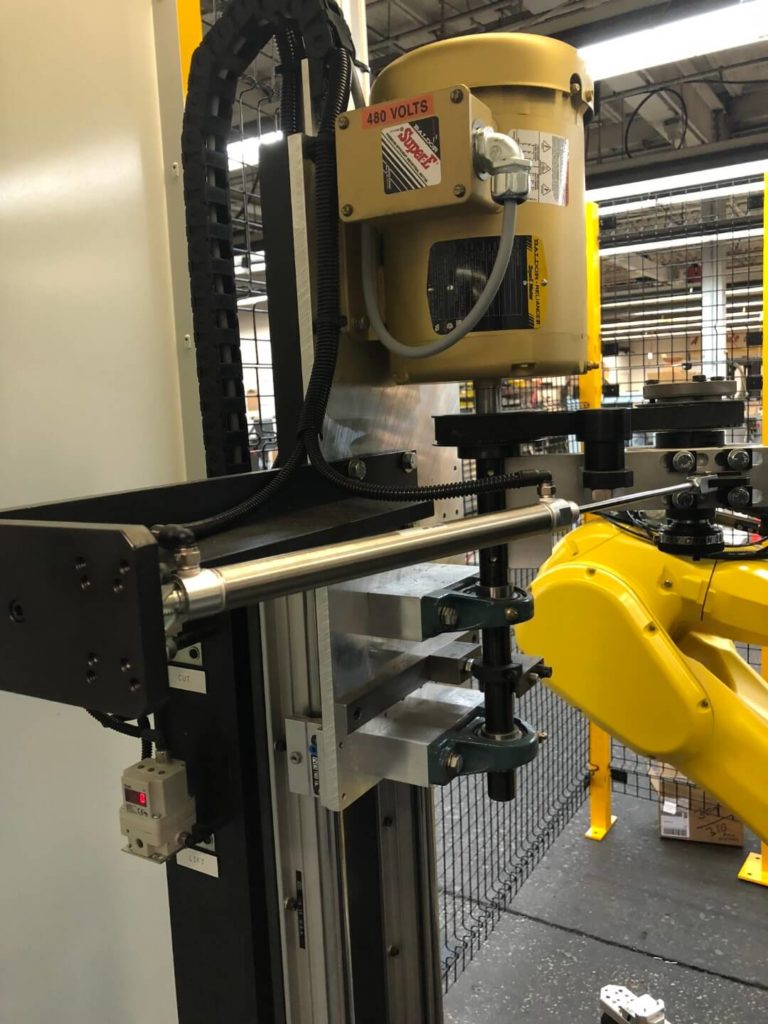
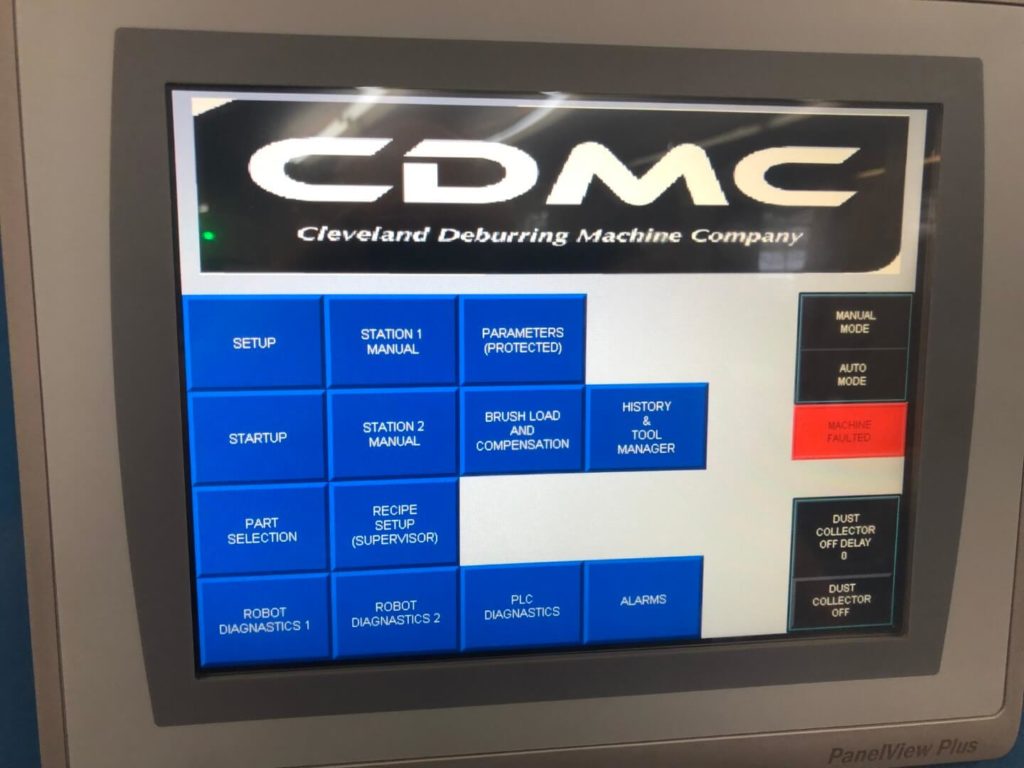
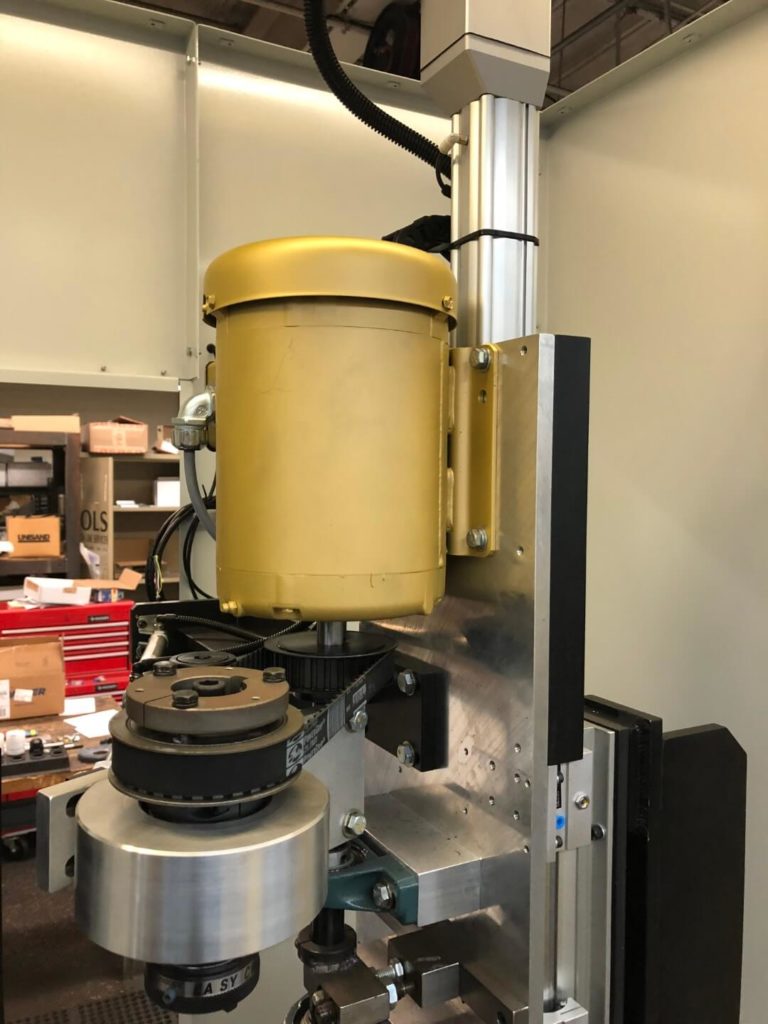
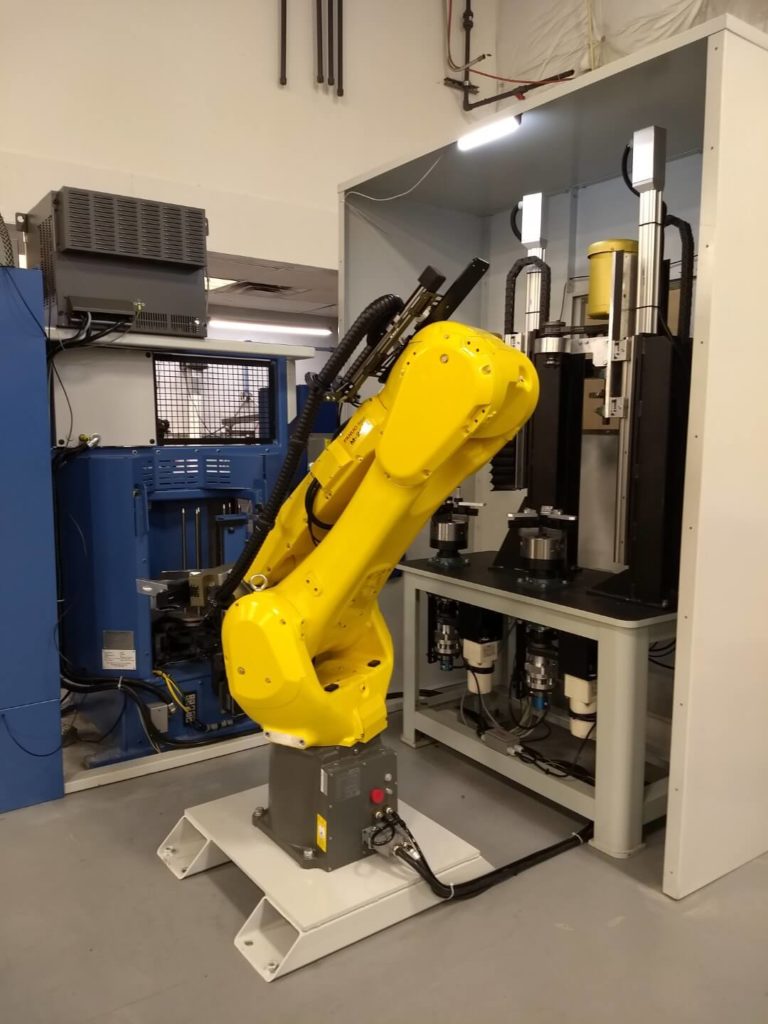
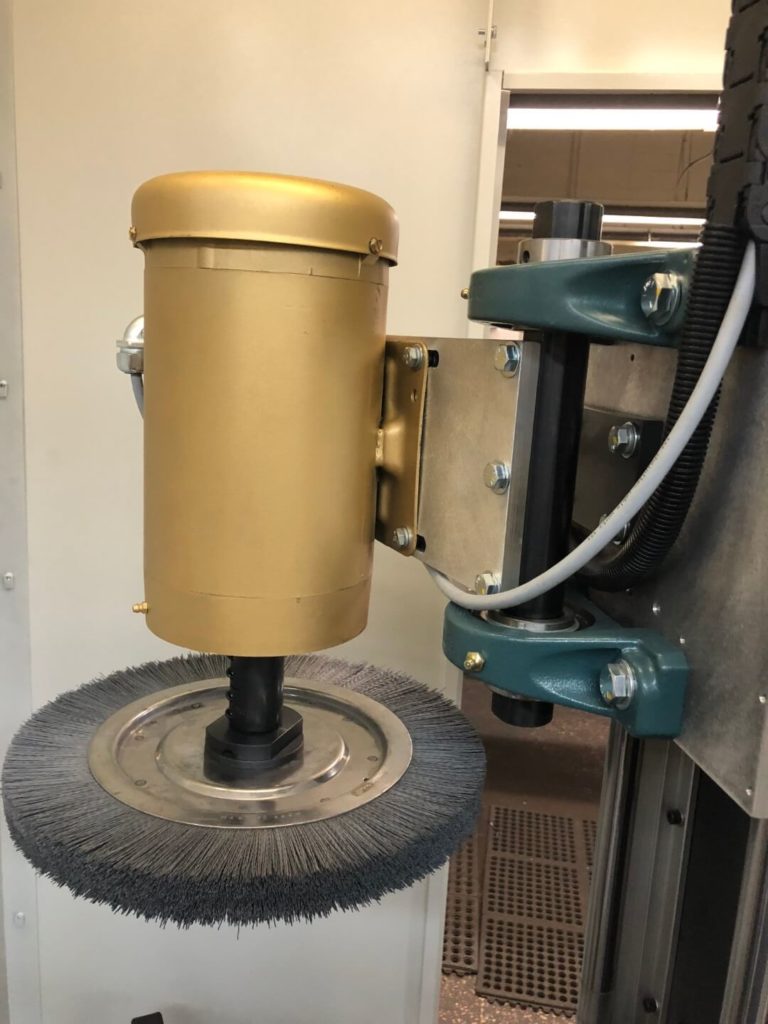
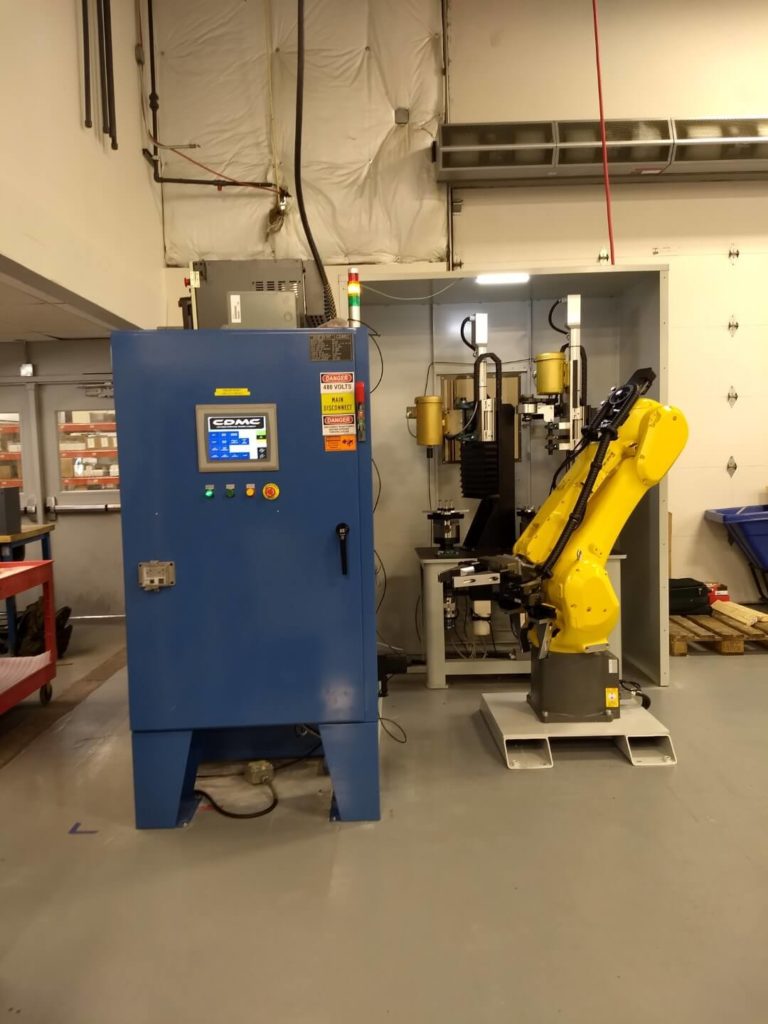
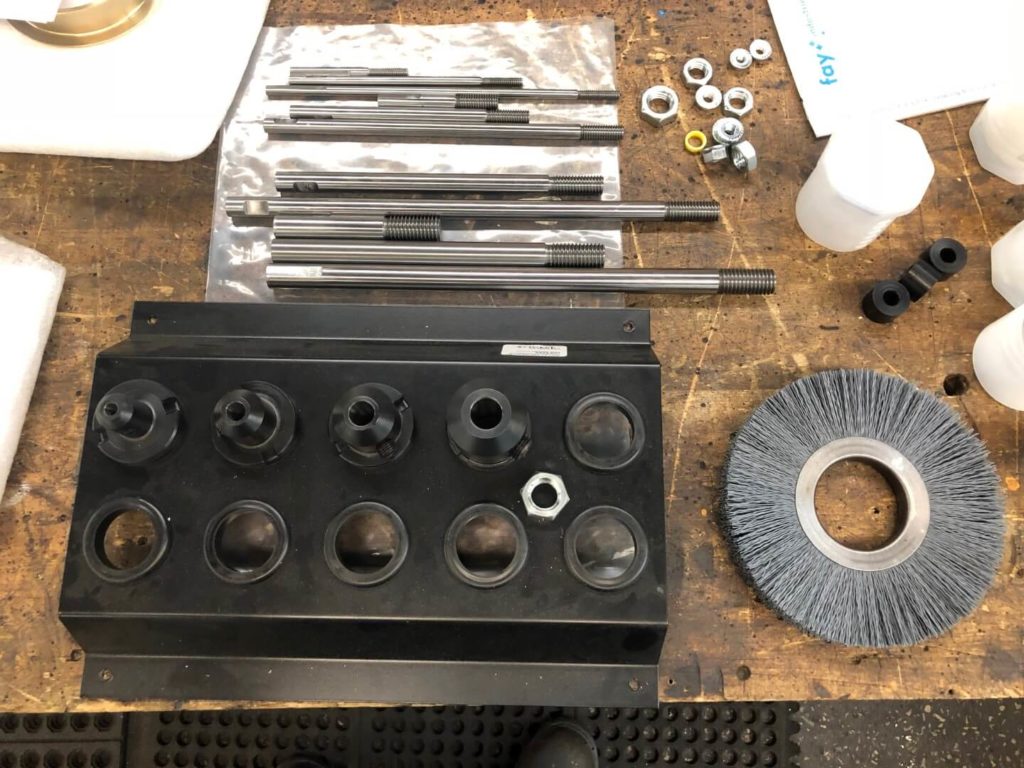
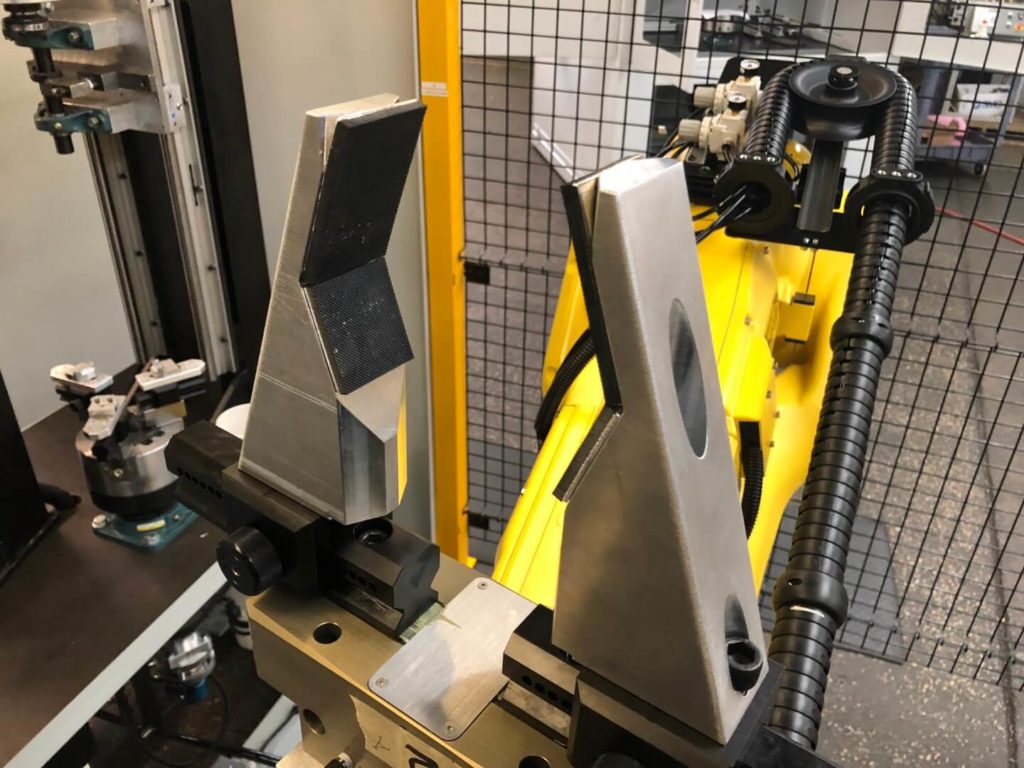
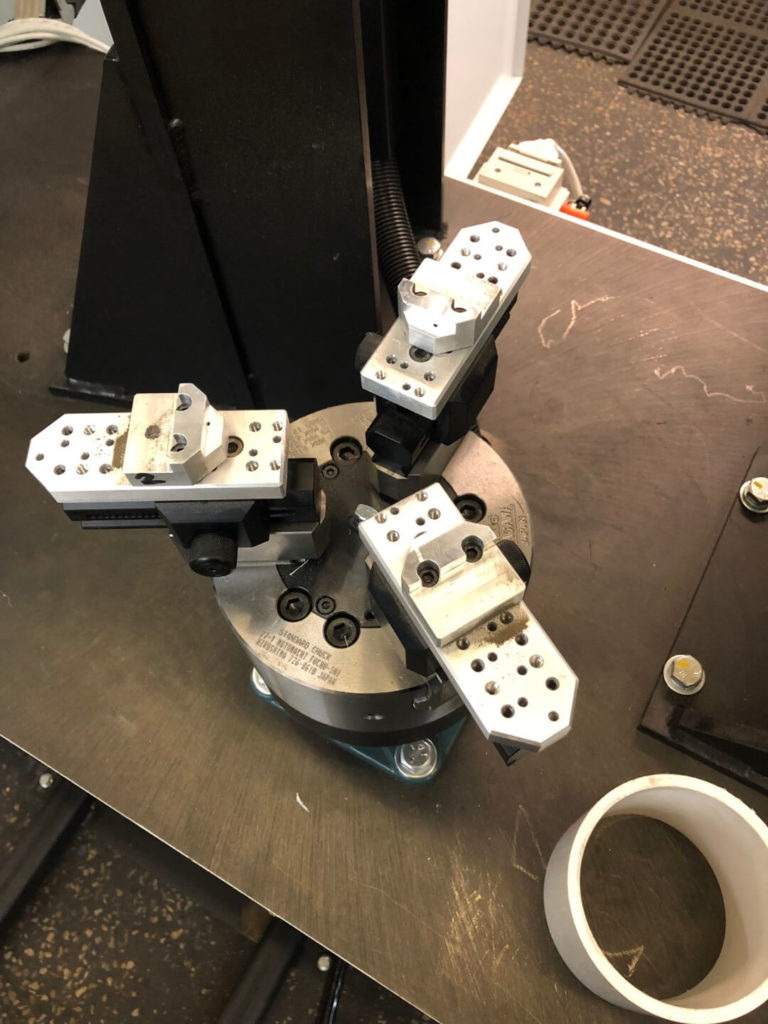
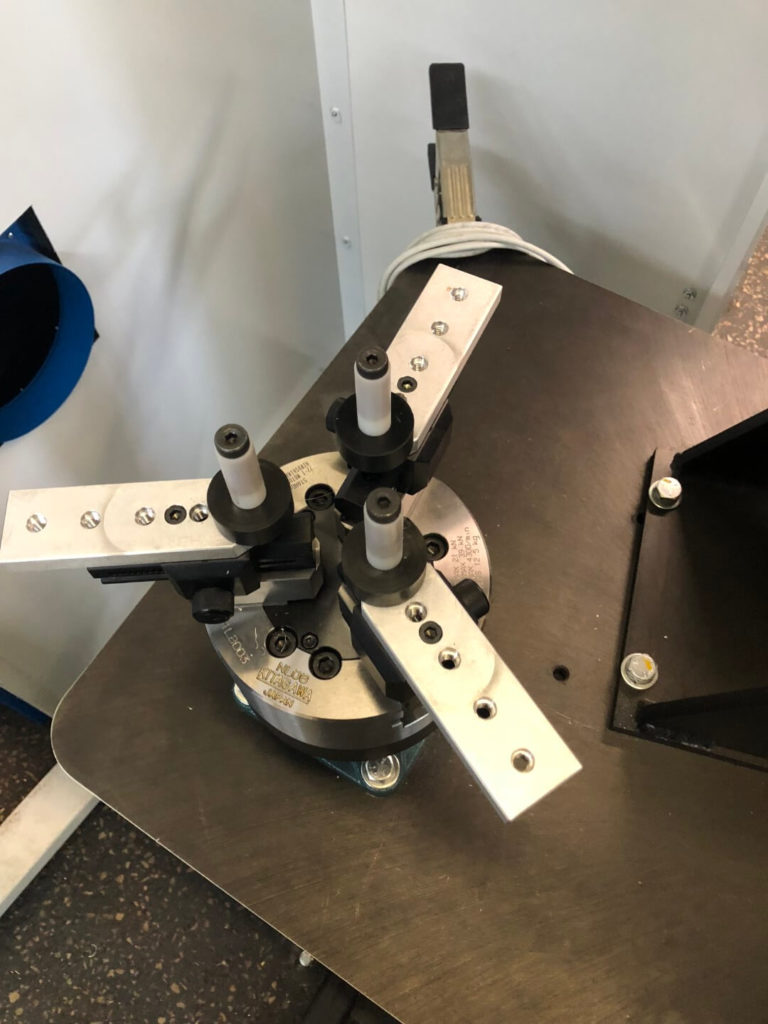
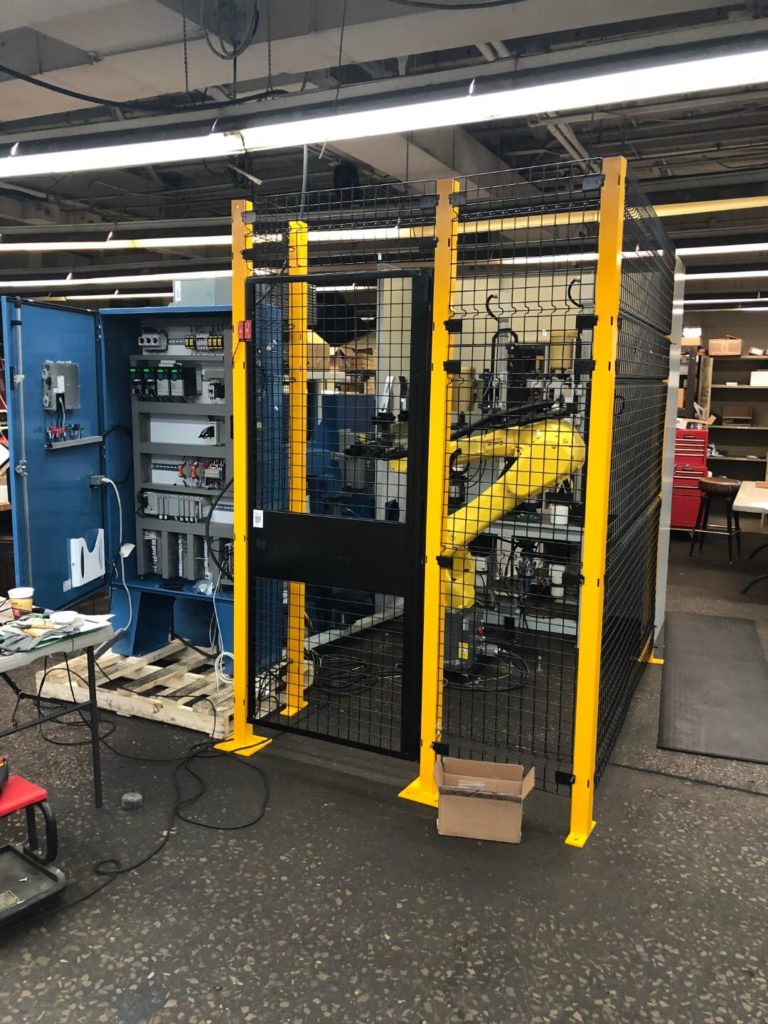
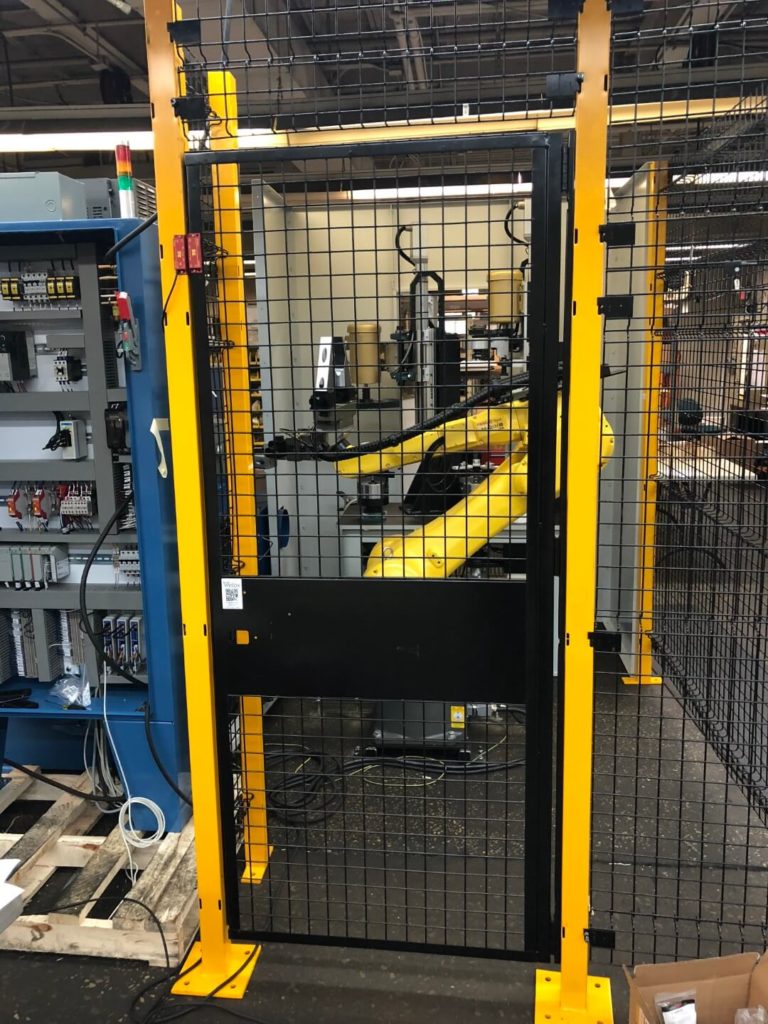