Parallel Axis Gears Case Study
The Challenge
Our customer is a major manufacturer of heavy machinery and they needed a solution to the problem of deburring moderate quantities of many different parts. Their main concern was the wide variety of deburring methods and machines in their plant. Many of the same types of gears were deburred in many different ways. Hand deburring imposed a steep learning curve on new employees. Inconsistent quality and output led to high inventory costs. The customer was re-organizing production into cellular modules and needed a comprehensive solution to implement the change. CDMC built and delivered six machines
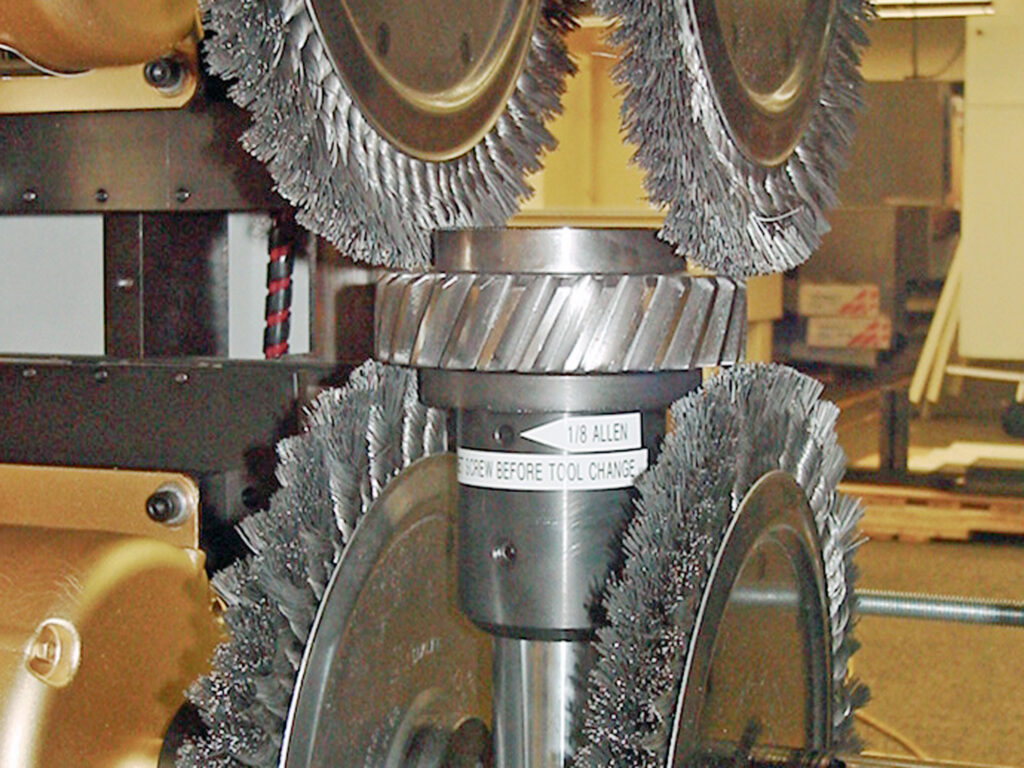
The Solution
- Allowed for manual or robot loading
- Eliminated the subjectivity and variables of many different processes
- Part is placed on spindle and is completely deburred top and bottom without flipping
- New setups can be achieved in about five minutes; stored setups can be recalled with the touch of a button
- Auto Amp Comp monitors and adjusts brushes for wear automatically for consistent quality and maximum brush life
- A set of brushes produces tens of thousands of parts!
- Rugged, dependable, predictable output
- Easy maintenance
The Benefits
The savings and efficiencies gained cut across many business metrics, and so are hard to quantify. Suffice it to say that our customer was so satisfied with the result that they ordered six more Model 5000’s, for a total of twelve. And the orders just keep comin’.
Before
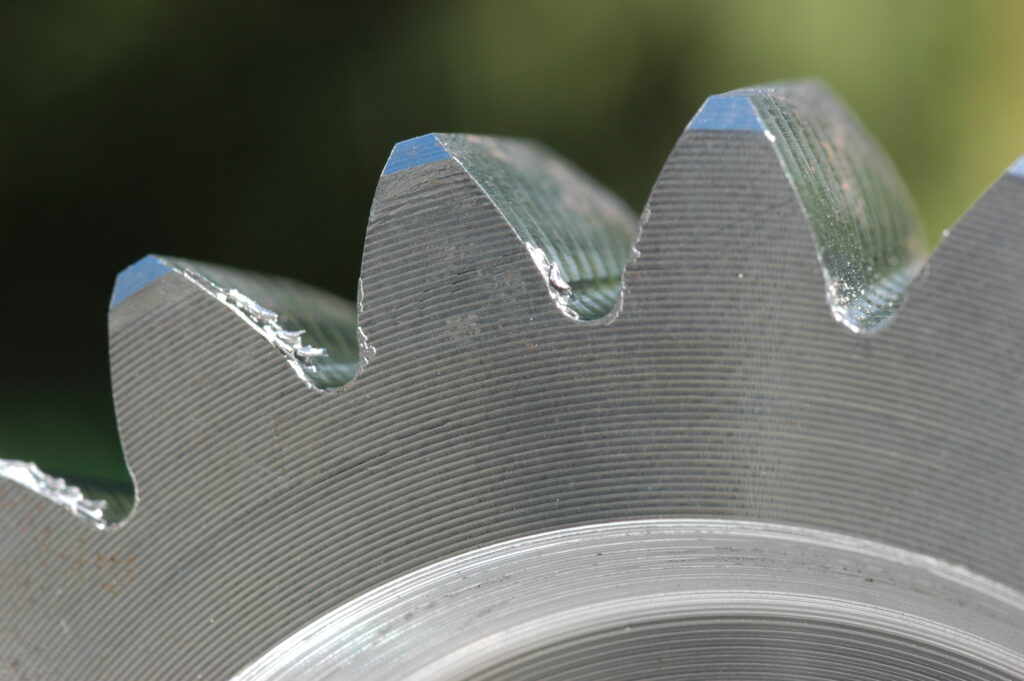
After
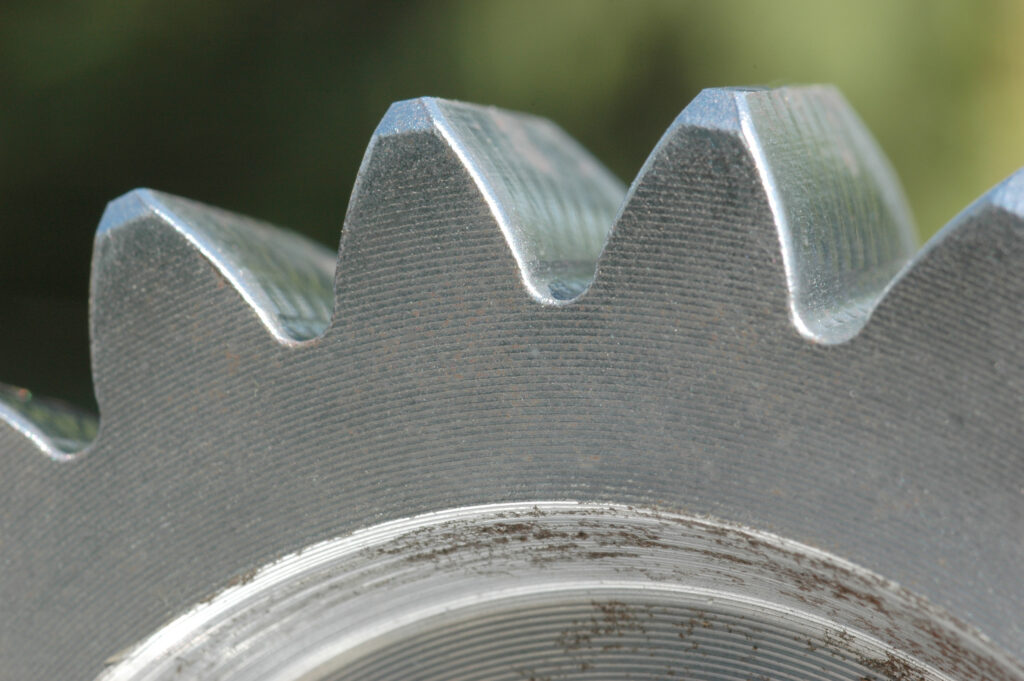