Deburring Case Study Powdered Metal
The Challenge
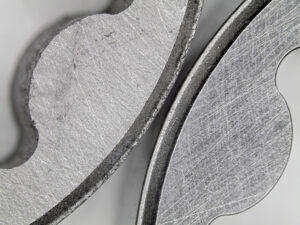
Our customer is a major contract manufacturer of powdered metal parts pressed into a wide variety of shapes. Their products are used in many automotive and fluid power applications. Many of the parts are low-profile and need deburring on both faces. The old method utilized nylon disc brushes monitored by operators. The parts were hand-flipped to the opposite face, sometimes resulting in quality issues. This customer wanted to grow their business, and they simply needed a much better way to fulfill their requirements. Deburring cost per part was $.04. CDMC conceived, designed, and delivered the following solution.
The Solution
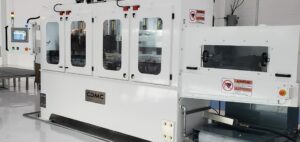
The Mag 8 is an in-line deburring machine that consists of two production platforms, essentially two machines side-by-side. This platform incorporates three magnetic conveyors. The first one receives parts on its upper surface and conveys them under four nylon abrasive brush heads rotating in opposing directions. The second conveyor captures the parts on their upper face, exposing the opposite face to four brushes approaching from below. The third conveyor captures the bottom face and passes the part through a de-magnetizer. In-house conveyors then carry the parts to the next process.
The Benefits
Using larger diameter brushes and an integrated coolant system greatly reduced the cost of brushing media. Incorporating Auto Amp Compensation allowed the machine to automatically (and in real-time) adjust the brushes to compensate for wear. Our unique and proprietary system squeezes the maximum life from the brush cores and produces consistent, repeatable deburring results, for better quality and less scrap. Brush changes and new part set-ups are a snap thanks to the Auto Set-up screen in the user interface. Easy access and easy-to-use software greatly reduce downtime. Variable speed brush motors allow for optimization of the process to accommodate different parts. Parts are deburred in one pass and move directly to the next process. After a brief optimization period, our customer’s costs dropped from 4 pennies per part to eight parts per penny. That’s right, 1/8 of a cent per part! A huge 3200% savings.
Before
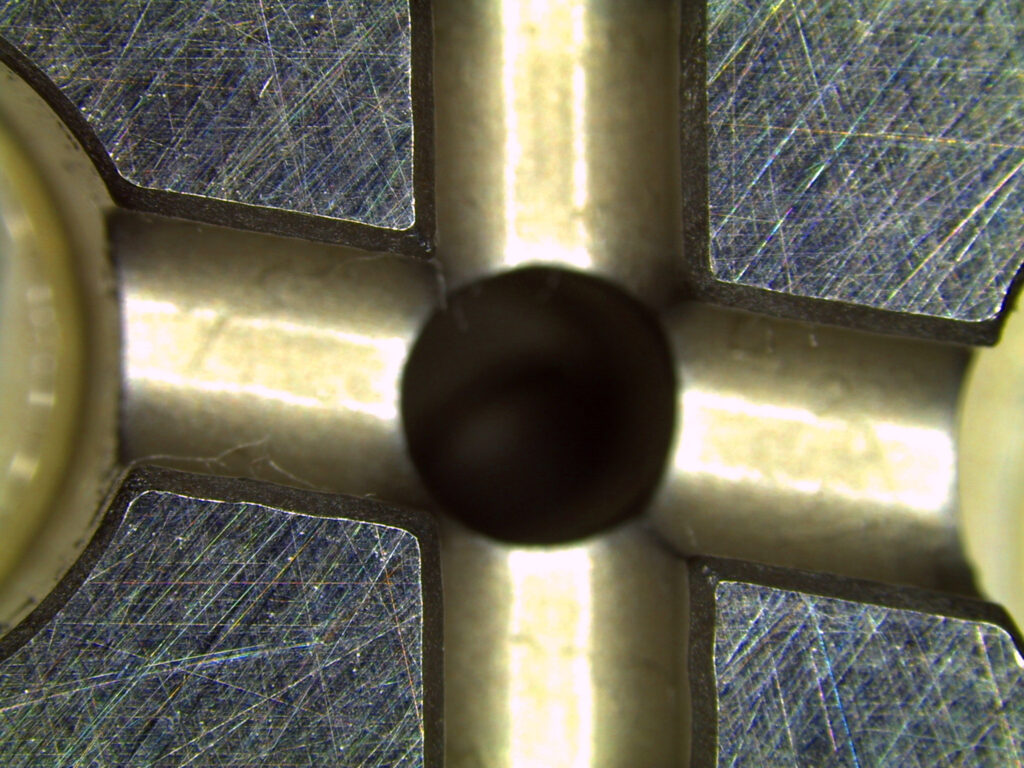
After
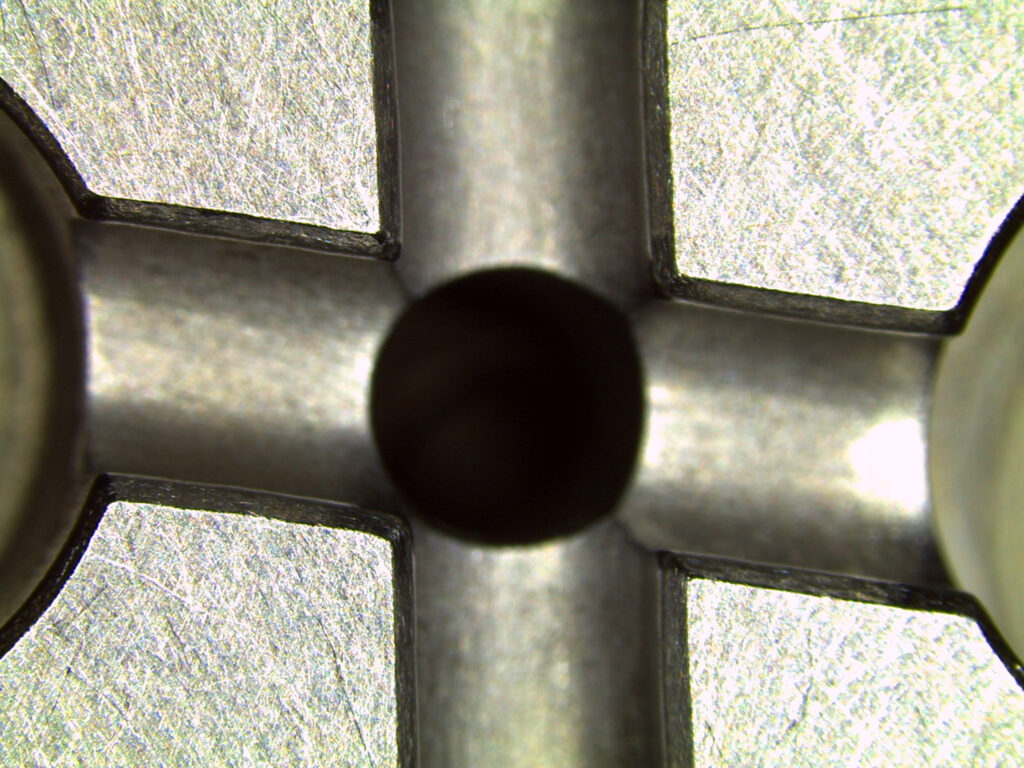